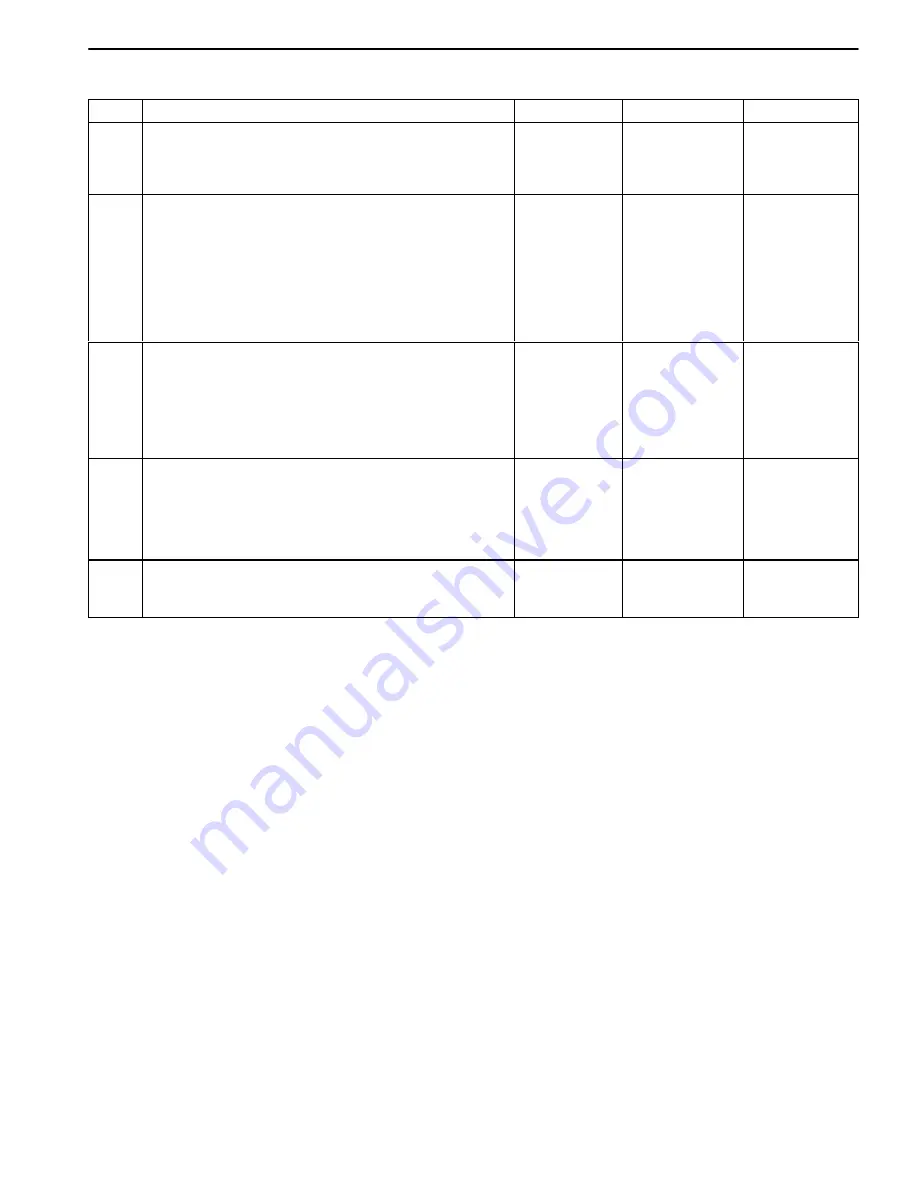
ENGINE CONTROLS 1F – 105
DAEWOO M-150 BL2
DTC P0141 – Heated Oxygen Sensor Heater Malfunction
Step
Action
Value(s)
Yes
No
1
Perform an Euro On-Board Diagnostic (EOBD)
System Check.
Is the system check complete?
–
Go to Step 2
Go to
“On-Board
Diagnostic
System Check”
2
1. Turn the ignition switch to LOCK.
2. Disconnect the Heated O2 sensor connector and
engine control module (ECM) connector.
3. Check the Heated O2 sensor heater wire
between the Heated O2 sensor connector
terminal 4 and ECM connector terminal 35 for an
open or short to ground.
Is the problem found?
–
Go to Step 3
Go to Step 4
3
1. Repair the wire of the connector terminal as
needed.
2. Clear the DTCs from the ECM.
3. Road tests the vehicle.
4. Perform the diagnostic system check.
Is the repair complete?
–
System OK
–
4
1. Turn the ignition switch to LOCK.
2. Replace the Heated O2 sensor.
3. Road tests the vehicle.
4. Perform the diagnostic system check.
Is the replacement complete?
–
Go to Step 6
–
5
Check if any additional DTCs are set.
Are any DTCs displaced that have not been
diagnosed?
–
Go to
applicable DTC
table
System OK
Содержание MATIZ
Страница 4: ...DRIVELINE AXLE CONTENTS SECTION 3B MANUAL TRANSAXLE DRIVE AXLE ...
Страница 6: ...TRANSAXLE CONTENTS SECTION 5B FIVE SPEED MANUAL TRANSAXLE SECTION 5C CLUTCH ...
Страница 9: ...RESTRAINTS CONTENTS SECTION 8A SEAT BELTS SECTION 8B SUPPLEMENTAL INFLATABLE RESTRAINTS SIR ...
Страница 44: ...1D 6 ENGINE COOLING DAEWOO M 150 BL2 RADIATOR FAN D12D4021 1 Radiator Assembly 2 Electric Cooling Fan Assembly ...
Страница 93: ...ENGINE ELECTRICAL 1E 37 DAEWOO M 150 BL2 SCHEMATIC AND ROUTING DIAGRAMS STARTING SYSTEM D12E2011 ...
Страница 94: ...1E 38 ENGINE ELECTRICAL DAEWOO M 150 BL2 CHARGING SYSTEM D12E2021 ...
Страница 95: ...ENGINE ELECTRICAL 1E 39 DAEWOO M 150 BL2 IGNITION SYSTEM CIRCUIT TYPICAL D12E2031 ...
Страница 96: ...1E 40 ENGINE ELECTRICAL DAEWOO M 150 BL2 IGNITION SYSTEM CIRCUIT EURO III MAA1E010 ...
Страница 122: ...1F 24 ENGINE CONTROLS DAEWOO M 150 BL2 MAA1F020 ENGINE CRANKS BUT WILL NUT RUN ...
Страница 142: ...1F 44 ENGINE CONTROLS DAEWOO M 150 BL2 MAA1F080 IGNITION SYSTEM CHECK ...
Страница 149: ...ENGINE CONTROLS 1F 51 DAEWOO M 150 BL2 BLANK ...
Страница 159: ...ENGINE CONTROLS 1F 61 DAEWOO M 150 BL2 BLANK ...
Страница 163: ...ENGINE CONTROLS 1F 65 DAEWOO M 150 BL2 BLANK ...
Страница 169: ...ENGINE CONTROLS 1F 71 DAEWOO M 150 BL2 BLANK ...
Страница 177: ...ENGINE CONTROLS 1F 79 DAEWOO M 150 BL2 BLANK ...
Страница 181: ...ENGINE CONTROLS 1F 83 DAEWOO M 150 BL2 BLANK ...
Страница 185: ...ENGINE CONTROLS 1F 87 DAEWOO M 150 BL2 BLANK ...
Страница 191: ...ENGINE CONTROLS 1F 93 DAEWOO M 150 BL2 BLANK ...
Страница 195: ...ENGINE CONTROLS 1F 97 DAEWOO M 150 BL2 BLANK ...
Страница 201: ...ENGINE CONTROLS 1F 103 DAEWOO M 150 BL2 BLANK ...
Страница 211: ...ENGINE CONTROLS 1F 113 DAEWOO M 150 BL2 BLANK ...
Страница 215: ...ENGINE CONTROLS 1F 117 DAEWOO M 150 BL2 BLANK ...
Страница 219: ...ENGINE CONTROLS 1F 121 DAEWOO M 150 BL2 BLANK ...
Страница 232: ...1F 134 ENGINE CONTROLS DAEWOO M 150 BL2 MAA1F160 ...
Страница 236: ...1F 138 ENGINE CONTROLS DAEWOO M 150 BL2 MAA1F160 ...
Страница 247: ...ENGINE CONTROLS 1F 149 DAEWOO M 150 BL2 BLANK ...
Страница 267: ...ENGINE CONTROLS 1F 169 DAEWOO M 150 BL2 BLANK ...
Страница 271: ...ENGINE CONTROLS 1F 173 DAEWOO M 150 BL2 BLANK ...
Страница 275: ...ENGINE CONTROLS 1F 177 DAEWOO M 150 BL2 BLANK ...
Страница 279: ...ENGINE CONTROLS 1F 181 DAEWOO M 150 BL2 BLANK ...
Страница 283: ...ENGINE CONTROLS 1F 185 DAEWOO M 150 BL2 BLANK ...
Страница 289: ...ENGINE CONTROLS 1F 191 DAEWOO M 150 BL2 BLANK ...
Страница 293: ...ENGINE CONTROLS 1F 195 DAEWOO M 150 BL2 BLANK ...
Страница 297: ...ENGINE CONTROLS 1F 199 DAEWOO M 150 BL2 BLANK ...
Страница 301: ...ENGINE CONTROLS 1F 203 DAEWOO M 150 BL2 BLANK ...
Страница 305: ...ENGINE CONTROLS 1F 207 DAEWOO M 150 BL2 BLANK ...
Страница 311: ...ENGINE CONTROLS 1F 213 DAEWOO M 150 BL2 BLANK ...
Страница 315: ...ENGINE CONTROLS 1F 217 DAEWOO M 150 BL2 BLANK ...
Страница 319: ...ENGINE CONTROLS 1F 221 DAEWOO M 150 BL2 BLANK ...
Страница 323: ...ENGINE CONTROLS 1F 225 DAEWOO M 150 BL2 BLANK ...
Страница 327: ...ENGINE CONTROLS 1F 229 DAEWOO M 150 BL2 BLANK ...
Страница 331: ...ENGINE CONTROLS 1F 233 DAEWOO M 150 BL2 BLANK ...
Страница 335: ...ENGINE CONTROLS 1F 237 DAEWOO M 150 BL2 BLANK ...
Страница 339: ...ENGINE CONTROLS 1F 241 DAEWOO M 150 BL2 BLANK ...
Страница 343: ...ENGINE CONTROLS 1F 245 DAEWOO M 150 BL2 BLANK ...
Страница 347: ...ENGINE CONTROLS 1F 249 DAEWOO M 150 BL2 BLANK ...
Страница 363: ...ENGINE CONTROLS 1F 265 DAEWOO M 150 BL2 BLANK ...
Страница 418: ...1F 320 ENGINE CONTROLS DAEWOO M 150 BL2 ECM WIRING DIAGRAM SIRIUS D3 1 OF 5 MAA1F610 ...
Страница 419: ...ENGINE CONTROLS 1F 321 DAEWOO M 150 BL2 ECM WIRING DIAGRAM SIRIUS D3 2 OF 5 MAA1F620 ...
Страница 420: ...1F 322 ENGINE CONTROLS DAEWOO M 150 BL2 ECM WIRING DIAGRAM SIRIUS D3 3 OF 5 MAAF630 ...
Страница 421: ...ENGINE CONTROLS 1F 323 DAEWOO M 150 BL2 ECM WIRING DIAGRAM SIRIUS D3 4 OF 5 MAA1F640 ...
Страница 422: ...1F 324 ENGINE CONTROLS DAEWOO M 150 BL2 ECM WIRING DIAGRAM SIRIUS D3 5 OF 5 MAA1F650 ...
Страница 446: ...FRONT SUSPENSION 2C 3 DAEWOO M 150 BL2 COMPONENT LOCATOR FRONT SUSPENSION D16B401A ...
Страница 573: ...4F 14 ANTILOCK BRAKE SYSTEM DAEWOO M 150 BL2 ABS Cont d D17E402A ...
Страница 574: ...ANTILOCK BRAKE SYSTEM 4F 15 DAEWOO M 150 BL2 BLANK ...
Страница 578: ...ANTILOCK BRAKE SYSTEM 4F 19 DAEWOO M 150 BL2 BLANK ...
Страница 586: ...ANTILOCK BRAKE SYSTEM 4F 27 DAEWOO M 150 BL2 BLANK ...
Страница 600: ...ANTILOCK BRAKE SYSTEM 4F 41 DAEWOO M 150 BL2 BLANK ...
Страница 610: ...ANTILOCK BRAKE SYSTEM 4F 51 DAEWOO M 150 BL2 BLANK ...
Страница 625: ...PARKING BRAKE 4G 9 DAEWOO M 150 BL2 SCHEMATIC AND ROUTING DIAGRAMS PARKING BRAKE SYSTEM D17A201B ...
Страница 629: ...5B 4 FIVE SPEED MANUAL TRANSAXLE DAEWOO M 150 BL2 INPUT SHAFT AND COUNTER SHAFT GEAR D13B4031 ...
Страница 781: ...HEATING AND VENTILATION SYSTEM 7A 31 DAEWOO M 150 BL2 SCHEMATIC AND ROUTING DIAGRAMS NON A C DIAGRAMS D18A201B ...
Страница 827: ...8A 12 SEAT BELTS DAEWOO M 150 BL2 SCHEMATIC AND ROUTING DIAGRAMS DRIVER SEAT BELT WARNING D1AA201A ...
Страница 836: ...SUPPLEMENTAL INFLATABLE RESTRAINTS SIR 8B 9 DAEWOO M 150 BL2 BLANK ...
Страница 840: ...SUPPLEMENTAL INFLATABLE RESTRAINTS SIR 8B 13 DAEWOO M 150 BL2 BLANK ...
Страница 908: ...9A 2 BODY WIRING SYSTEM DAEWOO M 150 BL2 DESCRIPTION AND OPERATION HOW TO READ ELECTRICAL WIRING DIAGRAM D111001A ...
Страница 913: ...BODY WIRING SYSTEM 9A 7 DAEWOO M 150 BL2 POWER DISRIBUTION SCHEMATIC D111005B ...
Страница 917: ...BODY WIRING SYSTEM 9A 11 DAEWOO M 150 BL2 FRONT HARNESS ROUTING Left Hand Drive Shown Right Hand Drive Similar D111401D ...
Страница 920: ...9A 14 BODY WIRING SYSTEM DAEWOO M 150 BL2 INSTRUMENT HARNESS ROUTING Left Hand Drive D111403E ...
Страница 921: ...BODY WIRING SYSTEM 9A 15 DAEWOO M 150 BL2 INSTRUMENT HARNESS ROUTING Right Hand Drive D111403F ...
Страница 923: ...BODY WIRING SYSTEM 9A 17 DAEWOO M 150 BL2 BODY HARNESS ROUTING D111405D ...
Страница 924: ...9A 18 BODY WIRING SYSTEM DAEWOO M 150 BL2 BODY HARNESS ROUTING Cont d D111406D ...
Страница 925: ...BODY WIRING SYSTEM 9A 19 DAEWOO M 150 BL2 FRONT DOOR HARNESS ROUTING D111407D ...
Страница 926: ...9A 20 BODY WIRING SYSTEM DAEWOO M 150 BL2 REAR DOOR HARNESS ROUTING D111408D ...
Страница 927: ...BODY WIRING SYSTEM 9A 21 DAEWOO M 150 BL2 TAILGATE HARNESS ROUTING D111409D ...
Страница 944: ...LIGHTING SYSTEMS 9B 17 DAEWOO M 150 BL2 SCHEMATIC AND ROUTING DIAGRAMS BACKUP LAMP S CIRCUIT D19D201B ...
Страница 945: ...9B 18 LIGHTING SYSTEMS DAEWOO M 150 BL2 HEADLAMPS CIRCUIT D19D202B ...
Страница 946: ...LIGHTING SYSTEMS 9B 19 DAEWOO M 150 BL2 HEADLAMP LEVELING CIRCUIT D19B723B ...
Страница 947: ...9B 20 LIGHTING SYSTEMS DAEWOO M 150 BL2 TAIL AND LICENSE PLATE LAMPS CIRCUIT D19D203B ...
Страница 948: ...LIGHTING SYSTEMS 9B 21 DAEWOO M 150 BL2 STOPLAMPS CIRCUIT D19D204B ...
Страница 949: ...9B 22 LIGHTING SYSTEMS DAEWOO M 150 BL2 TURN AND HAZARD LAMPS CIRCUIT D19D205B ...
Страница 950: ...LIGHTING SYSTEMS 9B 23 DAEWOO M 150 BL2 INTERIOR COURTESY LAMP CIRCUIT D19D206B ...
Страница 951: ...9B 24 LIGHTING SYSTEMS DAEWOO M 150 BL2 FRONT FOG LAMP CIRCUIT D19B724A1 ...
Страница 952: ...LIGHTING SYSTEMS 9B 25 DAEWOO M 150 BL2 REAR FOG LAMP CIRCUIT D19B724B ...
Страница 953: ...9B 26 LIGHTING SYSTEMS DAEWOO M 150 BL2 DIMMER CONTROL CIRCUIT EXCEPT W EUROPE D29B009A ...
Страница 954: ...LIGHTING SYSTEMS 9B 27 DAEWOO M 150 BL2 DAYTIME RUNNING LAMPS CIRCUIT W EUROPE ONLY D29B010A ...
Страница 958: ...9C 4 HORN DAEWOO M 150 BL2 SCHEMATIC AND ROUTING DIAGRAMS HORN WIRING SYSTEM D19D207B ...
Страница 998: ...9E 24 INSTRUMENT DRIVER INFORMATION DAEWOO M 150 BL2 INSTRUMENT CLUSTER FENIX 5MR D19B201S ...
Страница 999: ...INSTRUMENT DRIVER INFORMATION 9E 25 DAEWOO M 150 BL2 INSTRUMENT PANEL ILLUMINATION D19B202B ...
Страница 1000: ...9E 26 INSTRUMENT DRIVER INFORMATION DAEWOO M 150 BL2 DIGITAL CLOCK D19B203B ...
Страница 1030: ...9G 18 INTERIOR TRIM DAEWOO M 150 BL2 SPECIAL TOOLS AND EQUIPMENT SPECIAL TOOLS TABLE D109E101 KM 475 B Trim Remover ...
Страница 1072: ...GLASS AND MIRRORS 9L 17 DAEWOO M 150 BL2 SPECIAL TOOLS AND EQUIPMENT SPECIAL TOOLS TABLE D109E102 J 24402 Glass Sealant Remover ...
Страница 1073: ...9L 18 GLASS AND MIRRORS DAEWOO M 150 BL2 SCHEMATIC AND ROUTING DIAGRAMS REAR WINDOW DEFOGGER D19E201B ...
Страница 1082: ...9N 4 FRAME AND UNDERBODY DAEWOO M 150 BL2 SPECIFICATIONS UNDERBODY DIMENSIONS Unit mm in DBDM118A ...
Страница 1083: ...FRAME AND UNDERBODY 9N 5 DAEWOO M 150 BL2 Unit mm in DBDM119A Unit mm in DBDM120 ...
Страница 1084: ...9N 6 FRAME AND UNDERBODY DAEWOO M 150 BL2 Unit mm in DBDM117A ...
Страница 1095: ...DOORS 9P 3 DAEWOO M 150 BL2 COMPONENT LOCATOR FRONT DOOR D19C403A ...
Страница 1097: ...DOORS 9P 5 DAEWOO M 150 BL2 REAR DOOR D19C404A ...
Страница 1121: ...DOORS 9P 29 DAEWOO M 150 BL2 D19C635A Installation Procedure 1 Install the tailgate strut with the ball studs ...
Страница 1122: ...9P 30 DOORS DAEWOO M 150 BL2 SCHEMATIC AND ROUTING DIAGRAMS POWER DOOR LOCKS LEFT HAND DRIVE D19C201B ...
Страница 1123: ...DOORS 9P 31 DAEWOO M 150 BL2 POWER DOOR LOCKS RIGHT HAND DRIVE D19C201S ...
Страница 1124: ...9P 32 DOORS DAEWOO M 150 BL2 POWER DOOR LOCKS W ANTI THEFT CONTROL LHD D19C201S ...
Страница 1125: ...DOORS 9P 33 DAEWOO M 150 BL2 POWER DOOR LOCKS W ANTI THEFT CONTROL RHD D19C202S ...
Страница 1126: ...9P 34 DOORS DAEWOO M 150 BL2 POWER WINDOWS FRONT ONLY D19C202B ...
Страница 1152: ...9T ii REMOTE KEYLESS ENTRY AND ANTI THEFT SYSTEM DAEWOO M 150 BL2 BLANK ...
Страница 1160: ...9T 8 REMOTE KEYLESS ENTRY AND ANTI THEFT SYSTEM DAEWOO M 150 BL2 BLANK ...
Страница 1183: ...IMMOBILIZER ANTI THEFT SYSTEM 9T 31 DAEWOO M 150 BL2 SCHEMATIC AND ROUTING DIAGRAMS D19T001B IMMOBILIZER ANTI THEFT SYSTEM ...