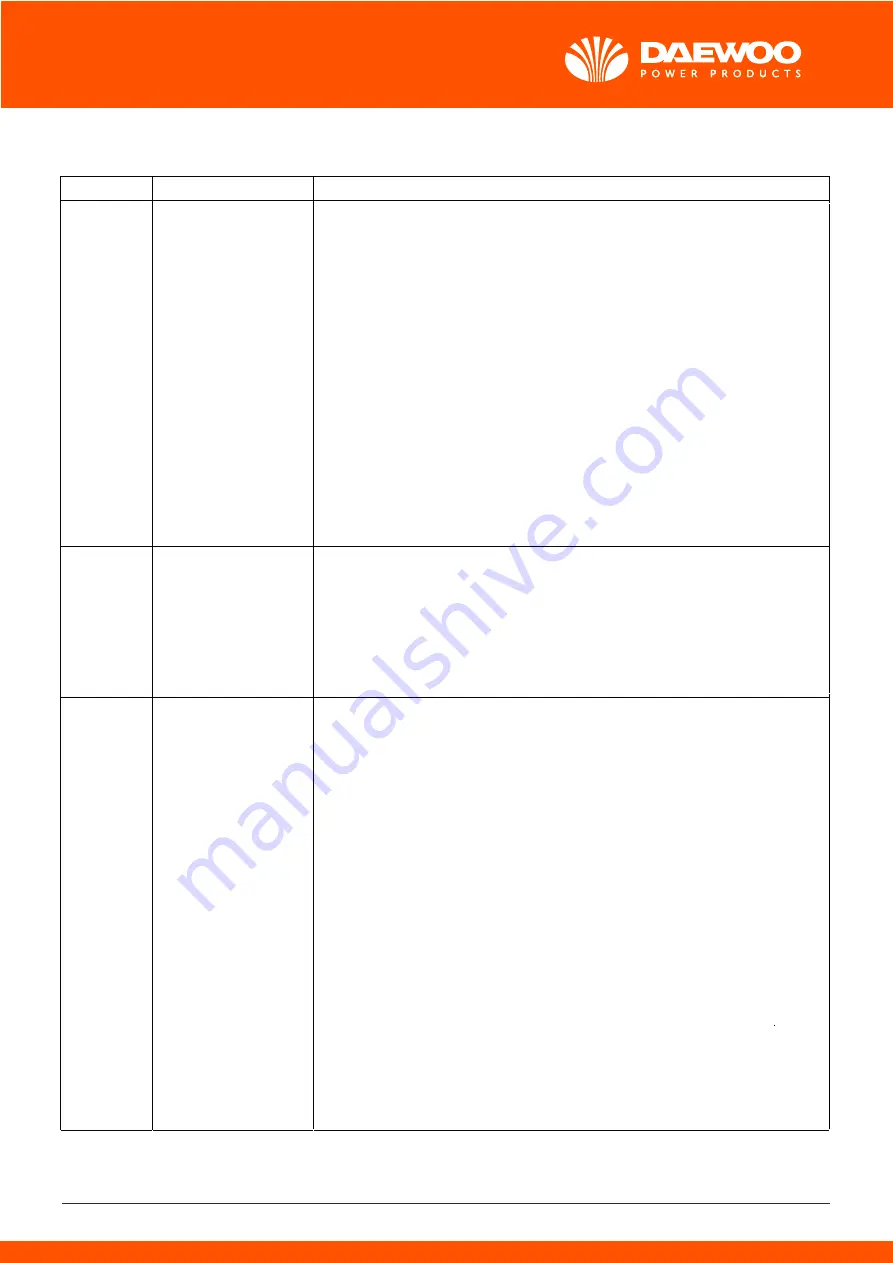
56
Fault judge and eliminate
Fault
Number
1. Low pressure pipe buckled or too long;
(
settle
)
2. Ignition system with not enough ignition power;
3. Ignition wires and FBT is not connected correctly;
4. Ignition wires and spark plugs are not connected properly;
5. Some of the cylinders miss the ignition;
Handling method of 3, 4, 5:
1
)
Pull out the spark plug, observe pole top to see whether it has burned
trace, if there is, then replace the spark plug.
2
)
Use multi-meter
(
XKΩ GEAR
)
test the resistance of the ignition wires, if
damaged, change ignition wires.
6. Und–er pressure of the cylinder; (check and adjust valve or replace the
piston ring )
7. High pressure fuel line blocked or out of shape; (clear or replace line)
8. Clean or replace air filter;
9. Mixer is not sealed well; (replace)
10. The joint part of mixer and throttle leaking; (settle)
11. Check gas pressure flow;
12. Check whether gas is up to standard, use only high grade LPG;
13. Air filter , exhaust system jam,(clean air filter and exhaust pipe);
14. Voltage output instability. ( adjust or change )
1. Safety fuse burned out; (replace)
2. Loss of GND connection; (settle)
3. Pressure reducer water cycle emerges ice block;
(Handling method: Clear the water cycle)
4. Pressure reducer low-pressure chamber leaks or diaphragm broken,
repair or replace; (settle or replace)
5. Air filter is too dirty; (check or clean)
6. Solenoid valve fault closed;
7. Fault of emergency stop switch;
Engine with not
enough power,
power, tumbling,
consumption of fuel
increases
Sudden Stop
1. Ignition timing is early and causes detonation;
Check distributor timing!
2. Ignition timing is late which causes backfiring of exhaust;
Dealing methods for Item 1 and 2: adjust the ignition timing on the distribu-
tor.
3.Tolerance between piston and cylinder is incorrect, it knocks when
starting engine, noise dissipates after warm-up of engine;
4. The gap between piston pin and pin hole is too big, sound is light but
clearer during idling;
5. The gap between main bearing and connecting rod bearing is worn, can
hear especially at lower speed, it sounds heavy and strong;
6. Lose crankshaft bearing, can hear noise when idling;
7. Broken Valve spring, excessive valve clearance, that can be heard
knocking around the cylinder cap;
Dealing methods for Item 3, 4, 5, 6 and 7: replace the parts, insure proper
tolerances and gaps.
8. When the piston hits the cylinder head, you can hear the knocking of
metal around the cylinder head;
Repair method: check the piston and valve to see if damage has occurred.
Abnormal sound when
the engine is opera-
ting
6
4
5
a. Liquid propane (lp vapor)
in engines set up to run on liquid propane, please check the fuel supply pressure, lower or higher
pressure range will result in equipment failure. inlet pressure 1.7kpa to 3.5kpa, and gas line should
be no longer than 16 feet or 5 meters, the inner diameter shall not be less than (0.63”) or 16mm.
It is strictly prohibited to remove high pressure gas lines during maintenance, service and repair.
You must check and test for gas leaks using a gas leak detector before use. The observation time is
not less than 1 minute per connection.
Based on different gas sources that are available, there may be different gas pressures present.
Make sure pressure is known before installation. A pressure reducing valve may be required to
obtain optimal requirements. You will need to use a pressure reducing valve if the pressure is exces-
sively high. Tools such as leak detectors and pressure gauges are not included with this purchase.
B. Natural Gas
If engine set to run on natural gas from factory, please check the fuel pressure and flow. The
purchase of a pressure reducing valve might be required and not included with this unit.
4. Electrical Connections
If the generator set is used for standby power, install properly sized automatic transfer switch (ATS)
provided by manufacture. This will prevent inadvertent interruptions of standby power and normal
sources of supply. Always shut down generator before servicing the equipment. Never contact
electrical leads or appliances when standing in water or on wet ground because these conditions
increase the risk of electrical shock.
5. Battery
Connect positive lead wire first (+) and then negative lead wire (-) to matching positive (+) and negati-
ve (-) terminals on battery. Connect negative
(
-
)
lead last!!!!!
IMPORTANT!
The generator will not start and circuit board damage can occur if battery is connec-
ted in reverse.
(Before initial use the maintenance free battery should be tested for voltage, if >12.6V,it can be
installed and used immediately; After first time use or <12.6V it should be re-charge before use.)
For first time use, you should operate according to the steps bellow:
-
Installing battery - take off red cap on positive battery terminal.
-
Use a multi-meter to check voltage of battery before installing and starting. If reading is below
-
Loosen positive battery clip. Connect positive terminal fully and adjust direction. Tighten terminal
nut on battery clip and place red rubber cover over terminal.
-
Follow the same steps for negative or black battery lead, then place rubber cover over terminal.
The battery represents a risk of high short circuit current. When working on the battery, always
remove watches, rings or other metal objects, and only use tools that have insulated handles!
Installing, Servicing or Exchanging the Battery should be performed or supervised by knowledgea-
ble personal. Battery connection or exchange requires precautions and protective gear. Always
wear face and eye protection with electrical rubber gloves, boots and battery apron. Keep unautho-
rized personnel away from battery.
Installing, Servicing or Exchanging the Battery should be performed or supervised by knowledgea-
ble personal. Battery connection or exchange requires precautions and protective gear. Always
wear face and eye protection with electrical rubber gloves, boots and battery apron. Keep unautho-
rized personnel away from battery.
When replacing battery, always use the same size battery and number type: 12V, Lead-acid battery.
CAUTION – Do not dispose of battery or batteries in a fire. Batteries are capable of exploding.
CAUTION – Do not open or mutilate the battery. Released electrolytes have been known to be
harmful to skin, eyes and to be toxic.
6. Grounding
Make sure the generator set is grounded. Check grounding strap to make sure the generator set
ground terminal.
7. Starting Generator
1) Digital display #1.
2) Turn on the power switch #2.
3) Turn on the fuel switch #3.
4) After 10seconds manually press #5 on control panel.
5) Press #6 to initiate system start.
6) Press 7 through 8 to observe frequency, voltage, speed and the 12V working voltage and opera-
tion time.
7) After the unit has started it will automatically sync with ATS and enter into automatic mode.
The emergency stop switch, power switch and fuel switch must be kept in the on position for auto-
matic start-up.
8. Inspection of Generator Set when Operating.
1) Radiator and Coolant Level. After warm-up, check the coolant flow in system by rising
lid to make sure coolant is circulating. If no coolant is visible flowing through hose to coolant reser-
voir, shut down the engine. Allow engine to cool down, and remove the radiator cap.
Check-lists
:
-
Check for fluid and coolant leaks.
-
Inspect inside and out of the radiator to ensure no excessive dirt is present.
-
Check the radiator coils and ensure no dust, dirt or foreign debris exists.
-
Check hoses to ensure it is not blocked.
Add additional coolant to recommended levels.
The emergency stop switch, power switch and fuel switch must be kept in the on position for auto-
matic start-up.
8. Inspection of Generator Set when Operating.
1) Radiator and Coolant Level. After warm-up, check the coolant flow in system by rising
lid to make sure coolant is circulating. If no coolant is visible flowing through hose to coolant reser-
voir, shut down the engine. Allow engine to cool down, and remove the radiator cap.
Check-lists
:
-
Check for fluid and coolant leaks.
-
Inspect inside and out of the radiator to ensure no excessive dirt is present.
-
Check the radiator coils and ensure no dust, dirt or foreign debris exists.
-
Check hoses to ensure it is not blocked.
Add additional coolant to recommended levels.
2) Fault Indicator Lamp
When red lamp indicator is illuminated, operator must shut the generator down and follow trouble
shooting guide and steps.
If the generator still won’t start, press the emergency stop switch. Rotate clockwise to pop up
position. After waiting for 30 seconds, try starting again. If generator still cannot be started, check
the generator carefully for loose wires, battery terminals and voltage output, gas flow to the lines
and generator.
It is important to confirm after starting that the normal electrical output range is not exceeded as
this will damage the generator.
4) Other Problems requiring shutting down of the Generator
You should shut down the engine if the following circumstances happen.
-
The engine speed is hunting ( inconsistently speeding up and down)
-
An abnormal noise is heard coming from the generator or engine.
-
The engine exhaust suddenly turns dark grey or black.
-
The fault indicating light is illuminated.
9. Shutting down the Generator
Should a need occur to shut down the generator, shut down the electrical output first by turning the
circuit breaker to the “OFF” position and depress the reset key. This will automatically shut the
engine and generator down.
The power switch (#2) needs to be in the open or on position if connected to the ATS system in order
for the unit to start automatically.
Chapter Three: Long term Care and Storage of Generator
I. Long Term Storage and Care
1. Remove battery positive lead first and then negative lead. Remove battery and store in dark dry
place. It is recommended to recharge it slowly every three months.
2. Turn Gas line to generator in off position and disconnect. Plug gas line with rubber plug to
prevent dirt from getting into gas line.
3. Remove all dirt from the generator if long time storage is needed.
4. Drain coolant from engine. Place drain pan under pre plumed coolant line and open valve allowing
all coolant to drain (See page 26).
5. Drain oil from engine. Place drain pan under pre plumed oil line and open valve allowing all oil to
drain (See page 26).
6. Ensure engine is in good technical condition, keep all surfaces clean.
7. Remove all spark plugs, pour 1oz or 30grams of engine oil in each spark plug opening, turn
crankshaft 20 turns slowly to allow oil to coat inside of cylinders and pistons, and then re-install
spark plugs.
8. Use dewatering Vaseline (heat range 100°-200°F) wipe on the surface of contacts.
9. Add light amount of penetrant oil to all, hinges, bolts and moving parts.
10. Use clean canvas or cloth to cover the engine and keep it dust-free.
11. Store and cover in a warm clean room with temperatures above (5°C, 41°F) relative humidity
should be kept between 40-70%.
12. Check all loose nuts, bolts and screws.
13. Seal gas line inlet valve with rubber plug to keep gas line free of dust.
14. Push the emergency stop button.
15. Cover the generator with the dust-proof cover, and keep it in the dry and clean place.
16. Keep it in well ventilated, dry rainproof area and away from flammable and explosive materials.
II. Starting after long periods of Storage
1. Wipe and remove protective lubricants from all contacts.
2. Remove spark plugs one at a time to remove 1oz or 30grams of engine oil from cylinders. Use
clean rag and place it in each spark plug opening and turn engine over slowly allowing oil to soak
into clean rag. Repeat this process for each cylinder.
3. Add light penetrant oil to all hinges.
4. Add coolant.
5. Add engine oil.
6. Check all wires and hose connections.
7. Install battery connecting positive lead first and then negative lead.
8. Reconnect gas line and check for leaks using a digital gas detector.
9. Start engine to make sure operation is normal.
10. If belts are making noise, shut down generator, allow to cool down and then tighten belts as
needed.
11. Check all electrical parts and digital display for normal working conditions.
12. If red indicator light on display panel is illuminated, perform trouble shooting procedures. See
trouble shooting guide.
2. MAINTENANCE OF GENERATOR
Regular maintenance is an important part of your investment and provides longevity of the complete
generator system. Keeps it in good working condition according to the specifications outlined and it
will provide many years of dependable service.
The following generator maintenance specifications are based on a good working environment. If
working conditions are less than desirable, (such as excessive dust, dirt and humidity, etc.)the
maintenance interval periods should be shortened.
When maintaining the generator set, you should operate in strict accordance with the following
requirements. Improper use and operation can cause premature failure.
I. Breaking-in Period of New Engine
The life of the engine is greatly determined by the state of the first cycle of use. It is recommended
that the oil be replaced after only 10 hours of use on the first cycle The new engine should be opera-
ted as required. Abnormal engine ware will directly affect the life of generator engine.
II. Maintenance of the Fuel System
The genset is multi-fuel and comes preset from the factory to ether Natural Gas (NG) or Liquid
Propane (LPG), Maintenance will vary according to the fuel used.
Fuel is flammable and an explosive material. Smoking is prohibited while working or servicing
generator.
When using Natural Gas (NG) or Liquid Propane (LPG)
-
Before each operation, you should check all components for loose connections. Check for fluid
leaks around cylinders, pipes and hoses. Tighten as needed.
-
Periodically check the gas pressure reducer and the solenoid valve sealing pad for deformities.
-
Periodically check the low-pressure gas line to see if it has weathered or aged (soapy water can be
used to detect leaks).
-
When maintenance of the gas line is required, gas valve must be closed before any maintenance or
repairs are carried out.
III. Maintenance of the Lubricating System
1. Engine Oil
Oil viscosity: Select the viscosity brand according to the ambient temperature.
Oil quality level (according to standards set by the American Petroleum Institute): API SE SP SG or
higher-level oil.
After 30 hours of running new engine, the oil must be replaced. Only maintain and replace the
amount of oil according to the requirement, this will ensure long dependable engine life. Recom-
mended oil: Shell, Mobil 1, Valvoline or similar oil quality.
Do not mix different grades and detergents of oil.
2. Replacement of old engine oil
Replacing engine oil: This unit comes with pre-drain hoses already installed from the factory for
ease of service. See photo on next page.
Start the engine for several minutes to increase the temperature of the engine oil and then stop the
engine.
Place pan under the oil drain hose. Open oil drain valve to drain out all engine oil.
Close oil drain valve and replace with recommended oil amount.
Start engine and allow new oil to circulate and fill oil filter for three minutes. Make sure there are
no visible oil leaks!
Shut down unit and top off oil as needed. Oil level should be between A and B marks on the dips-
tick, it is preferred that the level be close to B mark but not over!
3. Replacement of used oil filter with new oil filter
Replace old oil filter after the engine has cooled. The replacement cycle should be followed accor-
ding to the maintenance cycle schedule.
Steps for replacement
:
●
Use oil filter wrench to remove old oil filter. Turn to the left to loosen.
●
Before installing new oil filter coat, gasket surface with a thin layer of oil before installation.
-
Twist new filter to the right to tighten into place with a firm hand. Do not over or under tighten filter.
-
Start generator and run for several minutes. Check for leaks. Shut down unit and check oil level
using dipstick. Oil level should read between point A and point B on dipstick. If needed add additio-
nal oil. Do not over fill.
Use oil filter wrench if needed but don’t over tighten, the recommended torque is between
15N.M-20N.M. Disposes of used oil and filter properly and do not pour down drain or on ground
IV. Maintenance of the Cooling System
When the engine is operating, there must be enough antifreeze and distilled water in the radiator
system to insure proper engine cooling. It is suggested to check it regularly before use, if there is
not enough antifreeze or distilled water add as needed. Do not use mineral, hard water or poor
quality antifreeze. We suggest Prestone, Shell, Texaco or similar brand.
1. Replace antifreeze and distilled water as outlined in the service guide or if discolored to a brown
watery mix. Combine antifreeze and distilled water only to manufactures suggested guidelines.
Do not replace cooling liquid when the engine is hot.
After prolong use or time, the coolant can go bad and discolor. Follow the recommended steps as
outlined below:
-
Place pan under pre plumed coolant or water line pipe. See photo below.
-
Open coolant or water line pipe valve and allow it to drain completely.
-
Remove or wipe any old excess water.
-
Close coolant or water drain pipe line valve.
-
Refill radiator cooling system and reservoir until full.
-
Start the generator without load for a few minutes. Allow for air pockets in the system to settle.
Shut down generator and add additional coolant as needed until the level remains steady.
-
Shut down generator again and add coolant to the “FULL” level mark.
-
Make sure the expansion tank is filled half way between low and full mark.
-
Install radiator cap and expansion tank cover. Inspect system carefully to make sure there are no
leaks.
Hard water, mineral water and saline water is harmful to the engine and cooling system. Do Not
Use!
2. Routine Radiator Maintenance tips:
-
Regularly check radiator hoses. Inspect clamps and make sure they are secure.
-
If hoses become deformed, develop bulges, hardening or cracking is visible they need to be chan-
ged immediately!
-
Inspect and clean the cooling fins on the radiator regularly, use compressed air to blow out excess
dust and dirt. Important! Blow compressed air from the inside out. Debris can build over time and
affect the cooling system.
3. Routine Belt inspection tips:
Adjust and replace the water pump belt as needed. Inspect it regularly for cracking or missing
pieces of rubber.
Pump belt is extremely important. It drives the water pump that cools the engine and entire system.
Note:
Listen for sounds coming from the belts. If you hear the belts squealing when the generator
starts up, this is a sign that the belts are loose or worn and the system will run hot! If belts show
signs of cracks or pieces of belt are missing, contact service provider.
Important! To check to see if the belt is too tight make sure the main power switch is in the off
position. Perform the following inspections and adjust or replace belt as needed.
Deflection check of the belt
:
7
〜
10mm
(
0.28-0.35in
)
⁄100N
{
10.01kgf
(
22.1 lbs.
)
}
Adjust the deflected belt
:
-
Stop the engine.
-
Use thumb to press on the belt between pulley wheels.
-
If the tightness is not correct, adjust it by relaxing the tension wheel to the acceptable degree.
Replace the water pump belt when it is cracked, missing pieces of rubber or singes of considerable
wear.
CONTROLLER FEATURES
-
LCD display, easy to operate
-
System voltage/frequency selection and engine configuration
-
Maintain steady-state speed(stepping alternator)
-
High engine temperature
-
Low oil pressure
-
Over speed/Under speed
-
Crank cycle status
-
Over voltage/Under voltage
-
Charging system frailer
LIMITATIONS:
This limited warranty does not cover product failures resulting from:
-
Inappropriate use relative to designated power rating.
-
Inappropriate use relative to application guidelines.
-
Non-conformance to applicable industry standards for installation.
-
Normal wear and tear.
-
Improper and/or unauthorized installation.
-
Owner’s or operator’s negligence, accidents or misuse.
-
Lack of maintenance or unauthorized repair.
-
Noncompliance with any published guideline or policy for the product.
-
Improper storage before and after commissioning.
-
Owner’s delay in making product available after notification of potential product problem.
-
Use of steel enclosures within 60 miles of the coast of salt water when aluminum or an alternate
non-corrosive material enclosure option is available.
-
Replacement parts and accessories not authorized by Chongqing Panda Machinery Co., Ltd.
-
Owner or operator abuse or neglect such as: late servicing and maintenance and improper stora-
ge.
-
Damage to parts, fixtures, housings, attachments and accessory items that are not part of the
transfer switch or paralleling system.
This limited extended warranty does not cover costs resulting from:
-
Difficulty in gaining access to the product.
-
Repair of cosmetic damage to enclosures.
COMPONENTS COVERED:
The emission-related warranty covers all components whose failure would increase an engine's
emissions of any regulated pollutant, including components listed in 40 CFR part 1068, Appendix I,
and components from any other system you develop to control emissions. The emission-related
warranty covers these components even if another company produces the component. Your emis-
sion-related warranty does not cover components whose failure would not increase an engine's
emissions of any regulated pollutant.
3. SAFETY RULES
Save These Instructions – The manufacturer suggests that these rules for safe operation be copied
and posted near the unit’s installation site. Safety should be stressed to all operators and potential
operators of this equipment.
Study these SAFETY RULES carefully before installing, operating or servicing this equipment.
Become familiar with this Owner’s Manual and with the unit. The generator can operate safely,
efficiently and reliably only if it is properly installed, operated and maintained. Many accidents are
caused by failing to follow simple and fundamental rules or precautions.
The manufacturer cannot anticipate every possible circumstance that might involve a hazard. The
warnings in this manual, and on tags and decals affixed to the unit are, therefore, not all-inclusive. If
using a procedure, work method or operating technique the manufacturer does not specifically
recommend, ensure that it is safe for others. Also make sure the procedure, work method or opera-
ting technique utilized does not render the generator unsafe.
-
Despite the safety design features of this generator, operating this system improperly, and neglec-
ting routine maintenance can cause possible injury or death. Allow only certified and licensed
personal to install, operate and maintain this system.
-
Potentially lethal voltages are generated by these generators. Make sure all steps are taken to
render the machine safe before attempting to work or service the generator system.
Parts of the generator are rotating at high speeds and are hot during operation. Exercise care near
operating generators.
-
Installation must always comply with applicable local and state codes, standards, laws and regula-
tions.
Common Hazards!
-
A running generator gives off carbon monoxide, and odorless, colorless poison gas. Breathing in
carbon monoxide can cause headaches, fatigue, dizziness, nausea, vomiting, confusion, fainting,
seizures or death.
-
The engine exhaust fumes contain carbon monoxide, which can be DEADLY. This dangerous gas, if
inhaled in sufficient concentrations, can cause unconsciousness or even death. Do NOT alter or add
to the exhaust system or do anything that might render the system unsafe or in noncompliance with
applicable codes and standards.
-
Install a battery operated carbon monoxide alarm indoors, according to manufacturer’s instruc-
tions and recommendations.
-
Adequate, unobstructed flow of cooling and ventilating air is critical to correct generator operation.
Do not alter the installation or permit even partial blockage of ventilation, as this can seriously affect
safe operation of the generator. The generator MUST be installed and operated outdoors only.
-
Keep hands, feet, clothing, etc., away from drive belts, fans, and other moving or hot parts. Never
remove any drive belt or fan guard while the unit is operating.
-
When working on this equipment, remain alert at all times. Never work on the equipment when
physically or mentally fatigued.
-
Inspect the generator regularly, and contact the nearest Dealer for parts needing repair or replace-
ment.
-
Before performing any maintenance on the generator, disconnect battery cables to prevent acci-
dental start up. Disconnect the cable from the battery post indicated by a NEGATIVE, NEG or (–)
first, then remove the POSITIVE, POS or (+) cable. When reconnecting the cables, connect the
POSITIVE cable first, the NEGATIVE cable last.
-
Never use the generator or any of its parts as a step. Stepping on the unit can stress and break
parts, and may result in dangerous operating conditions from leaking exhaust gases, fuel leakage,
oil leakage, etc. NEVER STAND ON UNIT!
Electrical Hazards
-
Generators covered by this manual produce dangerous electrical voltages and can cause fatal
electrical shock. Utility power delivers extremely high and dangerous voltages to the transfer switch
as does the standby generator when it is in operation. Avoid contact with bare wires, terminals,
connections, etc., while the unit is running. Ensure all appropriate covers, guards and barriers are in
place, secured and/ or locked before operating the generator. If work must be done around an
operating unit, stand on an insulated, dry surface to reduce shock hazard. We recommend a
wooden pallet with rubber mat.
-
Do not handle any kind of electrical device while standing in water, while barefoot, or while hands
or feet are wet. DANGEROUS ELECTRICAL SHOCK MAY RESULT.
-
The National Electrical Code (NEC) requires the frame and external electrically conductive parts of
the generator to be connected to an approved earth ground. Local electrical codes also may require
proper grounding of the generator electrical system.
-
After installing this home standby electrical system, the generator may crank and start at any time
without warning. When this occurs, load circuits are transferred to the STANDBY (generator) power
source. To prevent possible injury if such a start and transfer occur, always set the generator’s
AUTO/OFF/MANUAL switch to its OFF position before working on equipment and remove the fuse
from the generator control panel.
-
In case of accident caused by electric shock, immediately shut down the source of electrical power
by pushing the emergency stop switch located on the outside of unit. Use a non-conducting imple-
ment to push the emergency stop switch if possible. If it is not possible, attempt to free the victim
from the live conductor. AVOID DIRECT CONTACT WITH THE VICTIM. Use a non-conducting item,
such as a dry rope or wooden board, to free the victim from the live conductor. If the victim is
unconscious, apply first aid and get immediate medical attention.
-
Never wear jewelry when working on this equipment. Jewelry can conduct electricity resulting in
electric shock, or may get caught in moving components causing injury.
Possible Fire Hazards!
-
For fire safety, the generator must be installed and maintained properly. Installation must always
comply with applicable codes, standards, laws and regulations. Adhere strictly to local, state and
national electrical and building codes. Comply with all regulations the Occupational Safety and
Health Administration (OSHA) has established. Also, ensure that the generator is installed in accor-
dance with the manufacturer’s instructions and recommendations. Following proper installation, do
nothing that might alter a safe installation and render the unit in noncompliance with the aforemen-
tioned codes, standards, laws and regulations.
Keep a fire extinguisher near the generator at all times. Extinguishers rated “ABC” by the National
Fire Protection Association are appropriate for use on the standby electrical system. Keep the
extinguisher properly charged and be familiar with its use. Consult the local fire department with
any questions pertaining to fire extinguishers.
Possible Explosion Hazards!
-
Do not smoke around the generator. Wipe up any fuel or oil spills immediately. Ensure that no
combustible materials are left in the generator compartment, or on or near the generator, as FIRE or
EXPLOSION may result. Keep areas surrounding the generator clean and free from debris.
-
Gaseous fluids such as natural gas (NG) and liquid propane gas (LPG) are extremely EXPLOSIVE.
Install the fuel supply system according to applicable fuel-gas codes. Before placing the standby
electric system into service, fuel system lines must be properly purged and leak tested according to
applicable code. After installation, inspect the fuel system periodically for leaks. Make sure there are
no gas leaks, use digital gas detector.
Only qualified electricians or contractors should attempt such installations, which must comply
strictly with applicable local and state codes, standards and regulations.
Uncrating and Initial Inspection
After uncrating, carefully inspect the contents for any visible damage. Do not tilt the machine more
than 30 degrees. Try to avoid transporting on uneven ground. Violent shaking and vibration during
transportation may affect the unit.
-
This standby generator set is ready for installation with a weather protective enclosure that is
intended for outdoor installation use only!
-
This ETL listed standby generator set may be packaged with an automatic transfer switch (ATS).
-
This ETL listed, 2-pole switch is rated at 200 AC amperes at 250 volts maximum. The 200 Amp
transfer switch is rated for indoor or outdoor use.
If this generator is used to power electrical load circuits normally powered by a utility power
source, it is required by code to install a transfer switch. The transfer switch must effectively isolate
the electrical system from the utility distribution system when the generator is operating (NEC 700,
701 & 702). Failure to isolate an electrical system by such means will result in damage to the genera-
tor and also may result in injury or death to utility power workers due to back-feed of electrical
energy.
If any loss or damage is noted at time of delivery, have the person(s) making the delivery, note all
damage on the freight bill or affix their signature under the consignor’s memo of loss or damage.
If a loss or damage is noted after delivery, separate the damaged materials and contact the carrier
for claim procedures.
“Concealed damage” is understood to mean damage to the contents of a package that is not in
evidence at the time of delivery, but is discovered later.
To properly open the cover, press down on the center top lip and release the latch. If pressure is not
applied from the top, the roof may appear stuck. Always verify that the lock is released before
attempting to lift the roof.
NEC Requirements
Local code enforcement may require that AFCI’s be incorporated into the transfer switch distribu-
tion panel. The Transfer Switch provided will accept AFCI’s.
Siemens P/N. Q115AF - 15A or Q120AF - 20A can be obtained from a local electrical wholesaler and
will simply replace any of the single pole circuit breakers supplied in the Transfer Switch distribution
panel.
First Step!
Contact your local building inspector or City Hall to be aware of all federal, state and local codes
that could impact the installation. Secure all required permits before starting the project!
Carefully read and follow all procedures and safety precautions detailed in the installation guide. If
any portion of the installation manual, technical manual or other factory-supplied documents is not
completely understood, contact your local authorized dealer for assistance.
It is extremely important to comply with all relevant NEC, NFPA and OSHA standards as well as all
federal, state and local building and electrical codes.
As with any generator, this unit must be installed in accordance with current NFPA 37 and NFPA 70
standards as well as any other federal, state, and local codes for minimum distances from other
structures.
1. Place the mounting area as close as possible to the transfer switch and fuel supply.
IMPORTANT! Pre wired control harness located inside ATS is 9’ feet long. Longer wiring harnesses
are available.
Leave adequate room around the area for service access. You must CHECK LOCAL CODE for
proper distance between generator and structure! We suggest the clearance between genset and
combustible materials is not less than 12ft away.
(check local code), and place high enough to keep rising water from reaching the generator. Select
an open space that will provide adequate and unobstructed airflow.
Electrical interference with such items as, cell phones, computers, TV’s and other electrical devices
and equipment can occur when standing close or next to running standby system.
2. Place the unit so air vents won’t become clogged with leaves, grass, snow or debris. Make sure
exhaust fumes will not enter the building through eaves, windows, ventilation fans or other air
intakes.
Build a rectangular form out of 2”X6 wooden studs. Dig an area approximately 4 inches deep and
about 4 to 6 inches, longer and wider than the footprint of the generator. Place wooden frame in
whole leaving approximately 2” above ground. Place polyurethane film in the bottom and fill with
pea gravel or crushed stone. Level and pack gravel or stone evenly. The concrete pad is now ready
to be poured.
When pouring concrete, set grade 5 anchor bolts in wet concrete based on the foot print of genera-
tor lining up with holes on the base of the unit. Once complete level and finish concrete pad and
allow to set.
3. Inspect packaging and generator for exterior shipping damage. Remove all packaging material.
4. Make sure the lifting equipment to be used has sufficient capacity to safely handle the weight of
the generator (20KW created gross weight 850lbs). Use nylon lifting straps and connect them to the
lifting eyebolts on each corner of the base frame to avoid damage to the enclosure (lifting eyebolts
included) Set generator into place and anchor tightly to concrete pad using grade 5 hardware.
5. When using forklift, you have to ensure that forks are wide enough to lift the unit from the bottom.
Fully insert the fork legs completely through the bottom of the machine. Pay attention to the machi-
ne components avoiding damage, lift and set flat on concrete pad.
6. Center the generator onto pad so that there is equal distance between the generator on all four
sides, making sure the generator is level within ¼” inch.
Grounding Generator
7. IMPORTANT! Connect an approved ground strap to the grounding lug on the base of frame and to
an approved earth ground or grounding rod as specified by local code and regulations.
DOTHIS STEP FIRST BEFORE ANY OTHER INSTALATION PROCEADURE IS PERFORMED!
Engine Pre-start and Preparation
All necessary installation and maintenance must be conducted and performed by authorized licen-
sed personnel.
Before starting engine for the first time, engine oil and radiator coolant must be added. An initial
fluid inspection and pre-check is recommended before starting genset for the first time or when unit
has been in operation for over 20 hours. It can also be used as a quick review of all fluids. Check all
of the following items before running system for the first time. (Please operate according to Opera-
tion and User’s Manual)
4. LUBRICATION SYSTEM
IMPORTANT NOTE! Unit is not shipped with engine oil or coolant from Factory!!
After installment of generator, fill engine with recommended oil weight based on ambient temperatu-
re shown below and add radiator coolant. Prior to initial start-up, replace all service panels and
close lid. Start engine and allow 10 minutes for system to warm-up. After this has been performed
remove service panels rise lid and check for any leaks or drips. If found, tighten lose hoses, clamps
or plugs. Recheck all fluid levels and top off as necessary.
Engine Oil. The unit is not shipped with oil from factory!!! Use high-quality detergent oil “Classified
for Service in CC, SD, SE, or SF use” Only use oil having the following SAE viscosity ratings. Fill with
the recommended amount of oil as specified. Overfilling or under filling can cause damage to the
engine. Use the following recommended or similar type engine oil.
Temperature Recommended Oil grade
Below 32° F (0° C)
SAE 10W or 15W-40
32° to 80° F (-1° to 27° C)
SAE 20W or 15W-40
Above 80° F (27° C) SAE 30W or 15W-40
-
Place funnel in engine oil inlet.
-
First time operation will require 4 liters or (4.25qts) of oil
-
Check oil gauge dipstick regularly, oil level should be kept between top and bottom lines, at all
times. It is preferred to be at the top mark but not over.
Cooling System
Use only automotive grade antifreeze and distilled water in cooling system.
Do not use water that contains salt or alkalis (Tap Water)! Using non-distilled water creates scale in
the radiator causing corrosion and premature wear.
Fuel Selection and Conversion from NG to LPG
1. Most generators are configured for natural gas operation at the factory. Switching over to LP
Vapor is a simple procedure
Fuel Conversion
These fuels are flammable and explosive materials. Do not operate around open flames.
1. When using LPG as fuel
:
●
Prior to each operation, you should check various components and handle any loose fasteners.
Check if there’s any leakage of the fuel tank, pipes and connections by utilizing a digital gas leak
detector (soapy water can be used). Service any leakage immediately!
●
When replacing fuel tank, close valve and turn off main power breaker on standby.
●
After fuel tank replacement, use gas leak detector for any leakage.
●
periodically check the pressure reducing valve, if the solenoid valve sealing pad is deformed. You
must first close the manual stop valve on the fuel tank. Then start the engine. Use up the gas in the
pipeline before you remove the solenoid valve and other parts, If not, this will have a greater risk of
high-pressure and is not safe.
●
The Pressure reducer is an important component of the gas supply system. You should pay
particular attention to its operation. If leakage occurs, the unit should be replaced. Periodically
remove the pollution discharge plug on the pressure reducer. Drain off the oil and condensation. If
the obstruction is not drained off, it can seriously affect its performance.
2. When using NG as fuel
:
●
Before each operation, you should check the integrity of the various components and handle any
loose fasteners immediately! Check if there’s any leakage from the fuel tank, pipes and connections
(soapy water can be used). Take care of leakage ASAP!
●
periodically check the pressure reducer, if the solenoid valve sealing pad is deformed, replace.
●
periodically check the low-pressure pipe. If any visible signs of wear, aging or leak detection are
observed, repair or replace. Soapy water can be used to detect leaks around connections.
●
during maintenance of the gas line, the valve must be closed prior to repair.
●
when the engine is operating, especially at high load, it should work 1-3 min in no load state, to
allow the engine to cool. Do not touch hot engine parts. The engine and exhaust system compo-
nents become extremely hot during operation. Make sure unit is disconnected from main power and
main gas lines before converting
Two fuel connections on the fuel block allow field conversion between natural gas (NG) and Liquid
Propane (LPG). The fuel metering valves are factory-set and sealed to provide the best possible hot
and cold starting.
Use the following procedure to convert fuel from one type to another.
Natural Gas (NG) and Liquid Propane (LPG) Conversion
●
Use a pressure reducing valve to reduce LPG pressure supply.
●
pushing the button as attached pictures show below to the natural gas or LP vapor per the fuel
which you want to use. Push in for LPG and out for NG
In engines set up to run on Liquid propane, please check the fuel supply pressure, lower or higher
pressure range will result in equipment failure. Inlet pressure 1.7kPa to 3.5kPa, and gas line should
be no longer than 16 feet or 5 meters, the inner diameter shall not be less than (0.63”) or 16mm.
5. INSTALLING AND CONNECTING GAS LINES
1. Natural gas and LP Vapors are highly explosive substances; you must follow all safety, codes,
standards and regulations.
Use a certified plumber familiar with local codes to make all gas line connections. Always use
AGA-approved gas pipe and a quality pipe sealant or joint compound.
Verify the capacity of the natural gas meter or the LP tank in regards to providing sufficient fuel for
both the generator and other operating appliances.
2. Most all applications will require an external manual shutoff valve on the fuel line.
3. Only use UL Listed or AGA-approved flexible fuel line in accordance with local regulations, when
connecting the gas line to the generator. The section of flexible fuel line is to ensure that vibration
from the generator does not create a gas leak at a connection point. Because of this, it’s important
the fuel line be installed with as few connection points and bends as possible.
4. Do not bend flexible fuel line to avoid using an elbow. Bending the flexible fuel line decreases its
ability to absorb vibrations and defeats the purpose. It also prevents smooth fuel flow.
5. After checking for leaks, check the gas pressure at the REGULATOR to make sure there’s enough
gas pressure for generator operation. See Owner’s Manual for fuel pressure specifications. If not
within these limits, contact your local gas supplier.
6. After checking and testing gas pressure regulator, close the main shutoff valve.
Single Phase External Power Connections and Wiring Diagram
Three Phase External Power Connections and Wiring Diagram
1. Locate area where electrical conduit will enter structure and drill 1.75” hole. Feed conduit through
hole, sealing both exterior and interior with caulk.
2. Seal the hole with silicone caulk. Don’t forget to caulk the hole inside the house as well.
3. Remove knockout in the back of connection box, feed wires through the back of the box and
secure the conduit with lock nut.
4. Mount connection box over whole in structure. Seal around all sides with weather proof caulk.
5. Connect all wires to the lugs inside connection box. Connect, black to black, red to red, white to
white. Connect ground wire to the ground lug and then connect breaker connections.
6. Close cover and lock connection box.
Initial Battery Connection and Controller Activation
1. When battery power is applied to the generator during the installation process, the controller will
light up. However, the generator still needs to be activated before it will automatically run in the
event of a power outage.
2. Battery Connection - connect positive red lead wire first (+) and then negative lead black wire (-)
to matching positive (+) and negative (-) terminals on battery. Connect negative
(
-
)
lead last!
3. Programming the generator is a one-time process that is guided by the controller screen
prompts. Once the product is activated, the controller screen will not prompt you again, even if you
disconnect generator battery. See SmartGen Owner’s Manual for programming
4.The Activation code is 1234 for basic programming and 8421 to enter into full feature program-
ming. Please complete the following steps at the generator’s control panel.
5. IMPORTANT! The generator will not start and circuit board damage can occur if battery is con-
nected in reverse.
(Before initial use the maintenance free battery should be tested for voltage, if >12.6V, it can be
installed and used immediately; after first time use or <12.6V it should be re-charge before use.)
For first time use, you should operate according to the steps bellow:
●
Installing battery - take off red cap on positive battery terminal.
●
Use a multi-meter to check voltage of battery before installing and starting. If reading is below
12.6V, recharge battery.
●
Loosen positive battery clip. Connect positive terminal fully and adjust direction. Tighten terminal
nut on battery clip and place red rubber cover over terminal.
●
Follow the same steps for negative or black battery lead, then place rubber cover over
terminal.
The battery represents a risk of high short circuit current. When working on the battery, always
remove watches, rings or other metal objects, and only use tools that have insulated handles!
Installing, Servicing or Exchanging the Battery should be performed or supervised by knowledgea-
ble personal. Battery connection or exchange requires precautions and protective gear. Always
wear face and eye protection with electrical rubber gloves, boots and battery apron. Keep unautho-
rized personnel away from battery.
When replacing battery, always use the same size battery and number type: 12V, Lead-acid battery.
CAUTION – Do not dispose of battery or batteries in a fire. Batteries are capable of exploding.
CAUTION – Do not open or mutilate the battery. Released electrolytes have been known to be
harmful to skin, eyes and to be toxic.
CAUTION – A battery presents a risk of electrical shock and high short circuit current. The following
precautions are to be observed when working on batteries:
1) Remove watches, rings, or other metal objects,
2) Use tools with insulated handles,
3) Wear rubber gloves, apron, eye protection and boots,
4) Do not lay tools or metal parts on top of batteries,
Make sure the generator set is grounded. Check grounding strap to make sure the generator set
ground terminal.
6. GENERATOR ELECTRICAL CONNECTION
If the Switch was purchased separately from the generator, a seal-tite electrical whip will need to be
connected to the generator. To complete the wiring, run ¾” conduit for the power leads and control
wires from the external connection box to the generator.
1. Feed the wires through the back of the generator and secure the conduit with lock nut.
2. Run power leads through the strain relief hole provided.
3. The circuit breaker and control panel are located under the top lid. Unlock and lift open to gain
access.
4. Remove the screws on the control panel cover to gain access to the connection area.
5. Feed the wires through the back of the generator and secure the conduit with locking nut.
6. Run power leads through the strain relief provided.
7. The circuit breaker is mounted inside next to the generator digital controller.
8. Secure circuit connections.
9. Users must connect the GND wire to the grounding lug and tighten.
10. The GND wire should be the same size but not smaller than the load wire.
11. Connecting according to the following connector bar from left side to right side.
12. Connecting according to the following type due to different Models.
Use insulated and certified wire/cable hose to connect the output hole. And the AC output wires/ca-
ble, and ATS control wires shall be separated by an insulation bushing (min 1.0mm)
Tighten all wires before operating generator set, or it will cause short circuit failure, do not connect
generator sets together, damage may occur if wires are connected in reverse.
The AC output wires shall be at least 3AWG, and temperature rating shall not less than 75 , and
copper wire.
Controller Key Functions Operation
Manual Start / Stop
1. MANUAL START: Manual mode is selected by pressing the button; a LED besides the button will
illuminate to confirm the operation; then press button to start the genset; it will detect crank
disconnect condition and generator accelerates to high-speed running automatically. With high
temperature, low oil pressure, over speed and abnormal voltage during generator operation, contro-
ller will protect genset and stop quickly. (Please refer to No.3~8 of Automatic Start Sequence in
controller manual for detail procedures.) The controller will send Close Gen signal after the genset is
running normally.
2. MANUAL STOP: Press will stop the running generator. (Please refer to No.2~6 of Automatic Stop
Sequence for detail procedures).
Digital Controller Indicator Lights
BASIC PARAMETER SETTINGS
Start the controller, then press to enter into the parameters setting menu, see fig 1 below:
Fig1
1. Set Parameters
2. Information
3. Language
4. Time and Date
Parameters Settings
When entering password interface, input correct password (default: 1234) can set all of the parame-
ter items in Form 1. If there is need to set more parameters (e.g. Voltage Calibration), please contact
the factory.
CAUTION: Please change the controller parameters when generator is in standby mode only (e.
g. Crank disconnect conditions selection, auxiliary input, auxiliary output, various delay), otherwise,
shutdown and other abnormal conditions may happen.
CAUTION: Over voltage set value must be higher than under voltage set value, otherwise over
voltage and under voltage condition may occur simultaneously.
CAUTION: Over speed set value must be higher than under speed set value, otherwise over
speed and under speed condition may occur simultaneously.
Refer to the SmartGen Controller Manual for more detailed parameters and settings
CAUTION: Please set the generator frequency value as low as possible when cranking, in order
to make the starter be separated quickly as soon as possible.
CAUTION: Auxiliary input 1~5 could not be set as same items; otherwise, there are abnormal
functions. However, the auxiliary output 1~4 can be set as same items.
CAUTION: If need to shut down after cooling, set any digital input as “WTH STOP by cool”, then
connect this input port, to ground soundly.
Note: In this interface, press will display the auxiliary inputs and outputs status.
-
Language
Chinese, English, Russian and Spanish interface can be selected.
-
Time and Date
The time and date information can be set in this interface.
Note: Pressing key at any time will stop the programming and return to the previous setting menu.
Auto Start / Stop Operation
Auto mode is selected by pressing the button; a LED besides the button will illuminate to confirm
the operation.
Automatic Start Sequence:
1. When “Remote Start” is active, “Start Delay” timer is initiated;
2. “Start Delay” countdown will be displayed on LCD;
3. When start delay is over, preheat relay energizes (if configured), “preheat delay XX s” information
will be displayed on LCD;
4. After the above delay, the Fuel Relay is energized, and then one second later, the throttle of the
driving stepper motor will rotate as the pre-set angle and then the Start Relay is engaged. The
engine is cranked for a pre-set time. If the engine fails to fire during this cranking attempt then the
fuel relay and start relay are disengaged for the pre-set rest period; “crank rest time” begins and
wait for the next crank attempt.
5. Should this start sequence continue beyond the set number of attempts, the start sequence will
be terminated, the fourth line of LCD display will be highlighted in black and a Fail to Start fault will
be displayed.
6. With a successful crank attempt, the “Safety On” timer is activated and the throttle on the driving
stepper motor will govern the speed, allowing Low Oil Pressure, High Temperature, Under speed,
Charge Alternator Failure and auxiliary inputs (to be configured) to stabilize without triggering the
fault. As soon as this delay is over, “start idle” delay is initiated (if configured).
7. During “start idle” delay, under speed, under frequency, under voltage alarms are activated. When
this delay is over, “warm up” delays are activated (if configured).
8. After the “warm up” delay, if generator status is normal, its indicator will be illuminated. If genera-
tor voltage and frequency have reached on-load requirements, then the generator close relay will be
energized; genset will take load; generator power indicator will illuminate and generator will enter
into Normal Running status. If voltage or frequency is abnormal, the controller
will initiate shutdown alarm (alarm information is displayed on LCD).
Automatic Stop Sequence:
1. When the “Remote Start” signal is removed, the Stop Delay is activated.
2. Once this “stop delay” has expired, the Generator Breaker will open and the “Cooling Delay” is
initiated. Moreover, the generator indicator is extinguished.
3. During “Stop Idle” Delay (if configured), idle relay is energized.
4. “ETS Solenoid Hold” delay begins, ETS relay is energized while fuel relay is de-energized.
5. "Fail to Stop Delay" begins, complete stop is detected automatically.
6. When generator is stopped completely, generator is placed into its standby mode. Otherwise, fail
to stop alarm is initiated and the corresponding alarm information is displayed on LCD.
7. Now connect the red and black power leads to the circuit breaker. Since this is a single-phase
application, it does not matter which wire is connected to which lug.
8. Connect the green equipment ground wire to the ground bus bar and torque to 35 inch lbs. The
torque values are:
-
10-14 AWG = 35 in/lbs.
-
8 AWG = 40 in/lbs.
-
4-6 AWG = 45 in/lbs.
9. Connect the white neutral wire to the neutral bus bar and torque to 35 inch lbs. The torque values
are:
-
10-14 AWG = 35 in/lbs.
-
8 AWG = 40 in/lbs.
-
4-6 AWG = 45 in/lbs.
10. Connect the control wires to the correct terminals.
NOTE:
In order to maintain separation of circuits, the DC control wires must be separated from the AC
control wires. Wrap insulation over the AC wires OR the DC wires, but not both, from the wire
landing area to the outside of the generator. Use cable lock to hold the insulation in place.
An improperly connected control wire can damage the generator control board.
Generator Circuit Diagram
CAUTION! Expand relay with high capacity start and fuel output is recommend.
CAUTION! Expand relay must be used in generator closed outputs.
Single Phase ATS Wiring Diagram
Three Phase ATS Wiring Diagram
Controller Wiring Diagram
Description of terminal connection: For more complete info reference Controller Owner’s Manual
The Connection between Controller and Genset
SmartGen Controller Specifications
Automatic Transfer Switch(ATS) Installation
-
Before beginning any installation, make sure power is shut OFF to the main distribution panel and
carefully read the ATS Owner’s Manual that came with the system.
-
All wiring must be the correct size and type, and must conform to all codes, standards and regula-
tions. Refer to the transfer switch Owner’s Manual and the National Electrical Code for additional
information.
-
The distribution load center switch in the ATS must be mounted close enough to the main distribu-
tion panel to accommodate electrical conduit and the 9’ft. EZ connection wiring harness from ATS
to standby unit. Make sure no water or corrosive substances can drip onto the transfer switch
enclosure.
-
Always inspect the switch for shipping damage. Never install a transfer switch that shows any
damage. Protect against impact and mount the switch vertically to a rigid support structure. Make
sure the switch is level and plumb.
-
The automatic transfer switch is an open transition switch. Open transition switches prevent elec-
trical feedback between the generator and the utility by only allowing load circuits to be connected
to one power supply at a time.
-
When three-conductor wiring is used, two 120 volt circuits will often share the same neutral wire.
To avoid overloading the neutral, either move BOTH of the circuits that share the neutral or don’t
move either of them.
-
When moving two circuits with a shared neutral, they should be connected to adjacent positions
(one above the other) in the transfer switch. That will assure that the two hot wires are on separate
phases and will maintain their relationship to neutral.
-
Choose a circuit to be backed up and remove the power lead from the breaker.
-
Using UL Listed wire nuts, reconnect the power lead to a matching breaker in the transfer switch.
-
Make sure each circuit moved is protected by the same size breaker in the transfer switch. 15 Amp
circuits must be connected to 15 Amp breakers and 20 Amp circuits to 20 Amp breakers.
-
Connect large neutral to the neutral bar in the distribution panel.
-
Install a 2-pole breaker in the distribution panel to protect the transfer switch. The required amp
rating of the breaker depends on which transfer switch is used. The ATS included with this unit is
200 Amps. This breaker must be compatible with the existing electrical distribution panel.
-
Install the breaker in two adjacent empty slots (one above the other) in the main panel.
-
EZ connect wiring harness, from ATS to generator control panel. Locate control panel wiring
harness pre-wired inside ATS. The 9’ft long controller harness passes through the electrical access
ports on the corner of generator above gas line connection.
-
EZ pre-wired Controller harness w/male plug located inside ATS.
-
Generator Electrical Access Port.
-
EZ Controller receptacle on Generator.
Wires/Cables Hose
-
The connection receptacle is located on the back side of control panel inside the standby genera-
tor. Remove rear panel to view the connection, from ATS. The wire will go out through the wire outlet
on the enclosure, passing harness through wire access in standby.
-
When all priority circuits have been moved to the transfer switch, close the main breaker to restore
utility power and make sure utility voltage at the transfer switch is correct. Refer to NFPA 70-E for
safety equipment required when working inside a live transfer switch.
Testing
1. Switch the generator’s main circuit breaker OFF and put the switch in the OFF
position.
2. Make sure utility power is OFF and place all of the priority circuit breakers in the transfer switch in
the OFF position as well.
3. Locate the transfer of power switch inside the ATS; use included handle to move the main con-
tacts to the standby power, or generator position.
4. NEVER OPERATE THE TRANSFER SWITCH MANUALLY WHEN LOADS ARE CONNECTED.
5. Allow the engine to warm up, and then switch the generator’s main breaker to the ON position.
The generator is now supplying electricity to the transfer switch but is not carrying any load.
6. Be sure that voltage and frequency from the generator is correct. If line-to-line voltage is not
approximately 240 volts, refer to the Owner’s Manual for the proper adjustments needed.
7. On all models, if line-to-neutral voltage is not 120 volts, check the neutral connection between the
generator and transfer switch.
8. When finished checking the voltage, switch the generator’s main circuit breaker OFF and put the
mode switch in the OFF position to shut down the generator.
9. Make sure the 2-pole circuit breaker installed in the main distribution panel is in the OFF position.
10. Use the transfer handle to move the main contacts in the transfer switch to on (utility position).
Switch the 2-pole breaker ON in the distribution panel.
11. Now switch the generator’s main breaker ON, and put the mode switch on AUTO.
12. Shut OFF utility power and make sure the generator starts automatically.
13. If everything worked correctly, switch the main breaker to ON position and make sure that power
is automatically transferred back to the utility and standby power shuts down automatically.
14. After the engine has completed its cool down cycle and shut down, shut OFF utility power again.
15. When the generator is supplying power to the transfer switch, move the breakers in the switch to
the ON position, one at a time, until the generator has accepted the entire selected load.
16. With the generator carrying the entire priority load, recheck gas pressure to verify that it is at the
same level it was before the generator was started.
IMPORTANT!
17. Even if the generator is running smoothly at this point, a drop in gas pressure indicates that the
supply is barely adequate to supply the generator’s needs. Changes in the generator load, or addi-
tional gas demand by other appliances may affect the generator’s overall performance. Verify gas
pressure and pipe size.
18. Switch the main breaker ON to restore utility power.
19. The generator will continue to run to allow the engine to cool down before shutting down.
20. Close the main breaker to restore utility power and allow the engine to cool its self down and
shut off automatically.
21. Operational tests are now complete. Refer to – Setting the Automatic Exercise Function to com-
plete the installation.
22. Testing is now complete.
23. Refer to Smart Gen Controller Owner’s Manual – Setting Automatic Exercise Function to comple-
te the installation.
Circuit Coverage for Whole House and Small Commercial
1. If the generator will be backing up all electrical loads within the panel, the amperage rating of the
transfer switch must be equal to or greater than the amperage rating of the normal utility service.
Unless a service rated transfer switch is used, a main service disconnect must be located before
the transfer switch. The transfer switch must be installed between the utility service entrance and
the building distribution panel.
2. A service rated transfer switch is installed between the service and the main distribution panel.
The service rated switch becomes the main service so no service disconnect is needed. The exis-
ting main distribution panel becomes a sub- panel.
3. The grounding that is normally in the main panel must be accomplished in the service rated
switch and must be disconnected in the existing distribution panel. Refer to the National Electrical
Code (NEC) for complete information on grounding and bonding.
Specified Electrical Circuit Coverage
IMPORTANT!
If the generator only powers designated breakers and circuits that are already grouped together and
wired into a separate specified distribution panel, the ATS must be installed between the main
electrical panel and specified distribution panel.
The amperage rating of the transfer switch must be equal to or greater than the highest amperage
rating of the utility and generator breakers feeding the switch.
Electrical Connections
Secure circuit connections:
-
Users must connect the GND wire to the grounding lug and tighten.
-
The GND wire should be the same with, or not smaller than the load wire.
-
Connecting according to the following connector bar from left side to right side.
-
Connecting according to the following type due to different Models.
Use the insulated and certified wire/cable hose to connect the output hole. And the AC output
wires/cable, and ATS control wires shall be separated by an insulation bushing (min 1.0mm). Tighten
all wires before operating generator set, or it will cause short circuit failure, do not connect genera-
tor sets together, damage may occur if wires are connected in reverse.
The AC output wires shall be at least 3AWG, and temperature rating shall not less than 75 , and
copper wires.
A).Connect the power leads from both the generator and the utility to the appropriate lugs in the
transfer switch. The lugs are clearly marked in the switch.
B). Neutral wires from both the utility and the generator are connected to the same neutral bar in the
switch.
C). Connect the control wires from the generator to the designated locations.
D). Complete the transfer switch wiring by connecting the equipment ground wires from both the
utility and the generator to the grounding bar lug.
E). Being careful to support the lugs, torque lugs to 20 N.m inside the transfer switch.
Functional Testing of Unit
1. Switch the main utility breaker OFF. Refer to NFPA 70-E for the safety equipment required when
working inside a live transfer switch.
2. Engage the utility power and check line-to-line and line-to-neutral voltage at terminals on the
transfer contactor. If line-to-line voltage is not approximately 240 volts, disengage utility power and
check terminal between the utility and Neutral 1 and Neutral 2. If line to neutral is not reading
approx. 120 volts, shut down utility power and re-inspect neutral terminal connections.
3. Repeat the same voltage checks on terminals to make sure current is flowing properly through
the contactor.
4. Switch the generator’s main circuit breaker OFF and put the mode switch in the OFF position.
5. Make sure utility power is in the OFF position and place all individual circuits in the main power
panel in
off position
as well.
6. Locate the transfer handle; insert the metal end into the slot in the main contactor assembly. Pull
the handle DOWN to move the main contacts to the standby power (generator) position. NEVER
OPERATE THE TRANSFER SWITCH MANUALLY WHEN LOADS ARE CONNECTED.
7. ATS Transfer Handle Transfer Lug
8. Locate the transfer handle; insert the metal end into the slot in the main contactor assembly. Pull
the handle DOWN to move the main contacts to the standby power (generator) position. NEVER
OPERATE THE TRANSFER SWITCH MANUALLY WHEN LOADS ARE CONNECTED.
9. Place generator in MANUAL mode before initiating start. After warm-up, transfer the generators
main breaker in the ON position. At this point, the system is now supplying electrical power to the
ATS but is not applying any electrical load
10. Check to be sure that voltage and frequency from the generator is correct. If voltage to the line is
not at least 240 volts, reference BNL20SE Owner’s Manual for proper corrective procedures. If
line-to-neutral voltage is not approximately 120 volts, check the neutral connection between the ATS
and generator.
11. Transfer the generator’s main circuit breaker to OFF position and put the mode switch in the OFF
position to shut down the generator.
12. With utility power still OFF, use the switch handle to move the main contacts to the Utility power
ON position.
13. Transfer the main breaker to turn utility power ON.
14. Transfer generator’s main breaker to ON position and set the ATS switch in AUTO mode.
15. To test, SHUT OFF utility power. Generator should start automatically after the time set delay has
expired.
16. Switch the utility breaker to ON and make sure that power is automatically transferred back to
the utility, shutting down generator automatically after cool down period.
17. Turn OFF utility power once again to automatically start the generator. When power has transfe-
rred to the generator, in the distribution panel, turn each of the breakers to ON position one at a time
until generator is accepting the full load.
18. With generator on full load, check and recheck gas pressure to verify that it’s maintaining the
same pressure level, prior to pre-starting generator.
19. CAUTION! Even though generator sounds and runs smoothly, a drop in gas pressure will barely
be adequate to supply the system’s needs. Changes in the electrical loads or additional gas demand
by other appliances will affect the generator’s performance. Verify gas pressure and pipe sizing.
Turn off the gas, unhook the manometer and re-install port plug.
20. Transfer utility breaker to ON position to restore electrical utility power.
21. The generator will continue to run to allow the engine to cool down, then it will shut down auto-
matically.
22. Shut OFF utility power again. The generator should start and the entire electrical load will trans-
fer to the generator.
23. Close the main breaker to restore utility power and allow the engine to cool down and shut itself
off.
24. Operational tests are now complete. Refer to SmartGen Owner’s Manual for setting the Automa-
tic Exercise Functions. This will complete the installation.
5. MAINTENANCE OF GENERATOR SYSTEM
Regular maintenance is an interracial part of the genset. To maintain good reliable condition, please
maintain according to specifications.
The following genset maintenance specifications are based on a good working environment and
normal operating conditions. Please strictly adhere to the following requirements. If working condi-
tions are less than favorable, (such as excessive dust, humidity, excess ambient temperature or the
temperature is too low, etc.) the maintenance period should be shortened accordingly.
Break-in of New Engine
The life of the engine is greatly dependent on the first 30 hours of use. It is vital to change the
engine oil after this initial period of time. It also an excellent time to inspect for, leaks, loose belts,
fluid levels gas lines, and connections. Tighten if necessary.
Replacing Engine Oil
Start the engine for several minutes to increase the temperature of the engine oil and then stop
engine.
-
Lower pre-plumed oil line out to the side.
-
Put a pan under the oil drain plug. Loosen oil drain bolt to drain off old engine oil.
-
Inspect oil drain screw and gasket for damaged. Replace if necessary.
-
Tighten oil drain screw and gasket. Inspect for oil leakage!
-
Fill with new engine oil and run engine for 2min. Shut down and recheck oil level. Add if needed. Oil
level should between level A (low) and B (full).
Oil Filter Replacement
The oil filter must be replaced when the engine is cooled. The replacement cycle should be accor-
ding to the maintenance cycle. Steps for replacement
-
Use the oil filter spanner to take of the oil filter
-
Coat the gasket surface with a thin layer of oil to adapt the new oil filter.
-
Fix the new oil filter
-
Run the genset for a few minutes. Check if there’s any oil leakage. Then check the oil level of the oil
pan and fill oil to the specified oil level.
-
Use oil filter spanner to fix the oil filter, the torque is between 15N.M-20N.M. When you remove the
filter cartridge, the oil level will drop. Be sure to check the oil spills.
Pre-plumed Oil Drain Line Direction A
:
Tighten Direction B
:
Loosen
Cooling System Maintenance
When the engine is in operation, there must be enough coolant in the radiator system to allow for
proper circulation. It is important to check this level regularly! Only use clean distilled water and
high quality antifreeze. See Owner’s Manual for more info and approved coolants.
Do not replace cooling liquid when the engine is hot!!!!!!
Check coolant effectiveness by using coolant tester during annual inspection of system. If needed,
change coolant.
Changing Coolant
-
Remove front cover panel.
-
Locate pre-plumed coolant line with drain cock. Open drain cock and allow coolant to drain.
Coolant Line
-
Close drain cock securely.
-
Refill with approved coolant and distilled water.
-
Start genset without load for 1 minute. Allow air pockets to dissipate. Stop generator.
-
Add cooling liquid to the radiator full level.
-
Fill the expansion tank with coolant to the “FULL” level.
-
Install the radiator cap and expansion tank cover. Inspect thoroughly for leaks!
Hard water, saline water or mineral water is harmful to the engine. Only use distilled water. If not
available, boil water and allow cooling before adding to radiator.
Water Pump Belt Adjustment and Replacement
The Water pump belt is used to cool the engine. If the tension is too loose or too tight, it will cause
engine overheating. If you hear the belt slipping or squealing, you should check the following. Adjust
or Replace.
Adjust deflected belt
:
-
Stop the engine.
-
Use the thumb to press on the belt of the pulley wheel.
-
If the tightness is not correct, adjust it by relaxing the regulating wheel, until to the acceptable
degree.
-
Replace the water pump belt when it’s broken.
Air Filter Maintenance
Take out the air filter cartridge and clean it based on the maintenance table (on page 39). The steps
are as follows:
-
Remove air filter cover, take out air filter element.
-
Blow off dust on the air filter element with compressed. IMPORTANT. Blow air from the inside out
of the element.
-
Clean the filter element using gasoline, dry with compressed air. IMPORTANT! Do not clean with
water.
-
Replace cracked or damaged air filter elements as soon as possible.
-
Re-install air filter cartridge and air filter cover. Secure clamps.
Radiator Maintenance
-
Check radiator hose often. Inspect hose clamps for tightness and leakage. If hose clamps are
loose, tighten as necessary.
-
If radiator hose is bulging or cracking, replace hose immediately!
-
Periodically clean the cooling fins of the radiator, using compressed air.
IMPORTANT! Lift lid and blow air from the inside out! Do not force air through radiator from the
outside in!
Winter Maintenance
When temperatures are under 0 /32°F, please maintain the engine specially
1. Use winter weight engine oil
2. Check coolant level
3. Use antifreeze tester to check effectiveness of coolant. Add coolant if necessary.
4. For severe cold weather climates we recommend a cold weather kit (sold separately).
Ignition System maintenance
This engine is equipped with electronic ignition; the order is 1-3-4-2. Suggested spark plug: F7RTC
(Autolite 4252) or similar type, Using the wrong type of spark plug will damage the engine.
Replacing spark plugs
-
Remove ignition wires from spark plug.
-
Using spark plug socket, remove from cylinder head.
-
Annually inspect spark plugs, replace if visible cracking is seen on insulators.
-
Measure the gap of each new spark plug!
Correct park plug gap is 0.9-1.1mm
-
Insert new spark plugs by hand first, then tighten with spark plug socket
-
Re-install ignition wires to correct cylinders.
Engine Maintenance
Utilize the following table to maintain the engine system. This will ensure many years of dependable
service. This symbol “
” indicates when a maintenance item needs to be performed.
Additional system maintenance
-
Keep the generator clean.
-
Add lubrication oil and anti-rust at the frictional position
-
Check all the screws loosen or not, and tighten them
Common Faults and Repair Methods of Engine
Trouble Shooting
Содержание DAPD15REG-EB
Страница 1: ...DAPD REG EB www daewoopowerproducts com Gas generator USER S MANUAL...
Страница 39: ...39 EN Three Phase ATS Wiring Diagram...
Страница 40: ...40 Controller Wiring Diagram...
Страница 61: ...61 8 SPARE PARTS LIST...
Страница 62: ...62 EN...
Страница 63: ...63...
Страница 64: ...64 EN...
Страница 65: ...65...
Страница 66: ...66 EN...
Страница 68: ...PR...
Страница 69: ...NG LPG ISO...
Страница 70: ...PR NG LPG ATS BNL SE BNL SE I...
Страница 71: ...35...
Страница 72: ...AC...
Страница 73: ...35 ON OFF OFF CC SD SE SF SAE F C SAE W or W F to C SAE W or W F C SAE W or W...
Страница 74: ...qts NG LPG LP LP...
Страница 75: ...35 A LP ATS...
Страница 76: ...ATS...
Страница 77: ...35...
Страница 78: ...OFF x...
Страница 79: ...PR x NG LPG x API SE SP SG...
Страница 80: ...x x x x x A B B A B...
Страница 81: ...PR x...
Страница 82: ...FULL...
Страница 83: ...PR kgf lbs LCD...
Страница 84: ...CFR I...
Страница 85: ...PR AUTO OFF MANUAL ABC...
Страница 86: ...NG LPG ETL ATS ETL AC NEC NEC AFCI...
Страница 87: ...PR...
Страница 88: ......
Страница 89: ...PR F C SAE W W F C SAE W W F C SAE W W qts...
Страница 90: ...LPG NG NG LPG LPG LP LPG NG LPG NG...
Страница 91: ...35 LP AGA LP UL Listed AGA...
Страница 92: ......
Страница 93: ...35...
Страница 94: ......
Страница 95: ...35 GND GND AC ATS AC AWG...
Страница 96: ...Controller O AUTO LED Close Gen...
Страница 97: ...35 WTH STOP by cool LCD XX s LCD LCD Safety On LCD...
Страница 98: ...Fail to stop LCD AWG AWG AWG AWG AWG AWG...
Страница 99: ...35 DC AC AC DC...
Страница 100: ...ATS...
Страница 101: ...35 Three Phase ATS Wiring Diagram...
Страница 102: ......
Страница 105: ...35 ATS UL EZ...
Страница 106: ...ATS EZ AC ATS...
Страница 107: ...35 ATS OFF AUTO ON ON...
Страница 108: ...x x x x ATS GND GND AC ATS AC AWG...
Страница 109: ...35 NFPA E...
Страница 110: ...MANUAL ATS BNL SE OFF OFF ON ATS AUTO ON...
Страница 111: ...35 A B N M N M...
Страница 112: ...B B...
Страница 113: ...35 FULL...
Страница 114: ......
Страница 116: ...LPG NG LPG Z Z v t d d v Z t d Y u e Z Z Z Z Za Z d Y Z Z Z Y e e Zm Z e Z Z e Y fyY Y Y uY t Z...
Страница 117: ...EN Z Z f Z d Y Z m f Y c Z Z Y fu d d Y y Z Z y Y f Y Y fuY Z Zn Z d Y y d Y Y d Y Z Zf Y Z Z Z y Z Y Y Y f GND 35...
Страница 118: ......
Страница 119: ...EN AC AVR 35...
Страница 120: ...DAPD REG EB NG LPG LPG kVA NG kVA V LPG NG rpm QR cc ECM IGNITION QDY V kW L mm mm L V W CCA A AVR POLE F 35...
Страница 121: ...EN HSC IP ft M dB A PET NG m hr LPG kg hr NG kPa LPG kPa mm mm kg kg...
Страница 122: ......
Страница 123: ......
Страница 124: ...35...
Страница 125: ......
Страница 126: ...35...
Страница 127: ......
Страница 128: ...ration Korea...
Страница 129: ...www daewoopowerproducts com Manufactured under license of Daewoo International Corporation Korea...