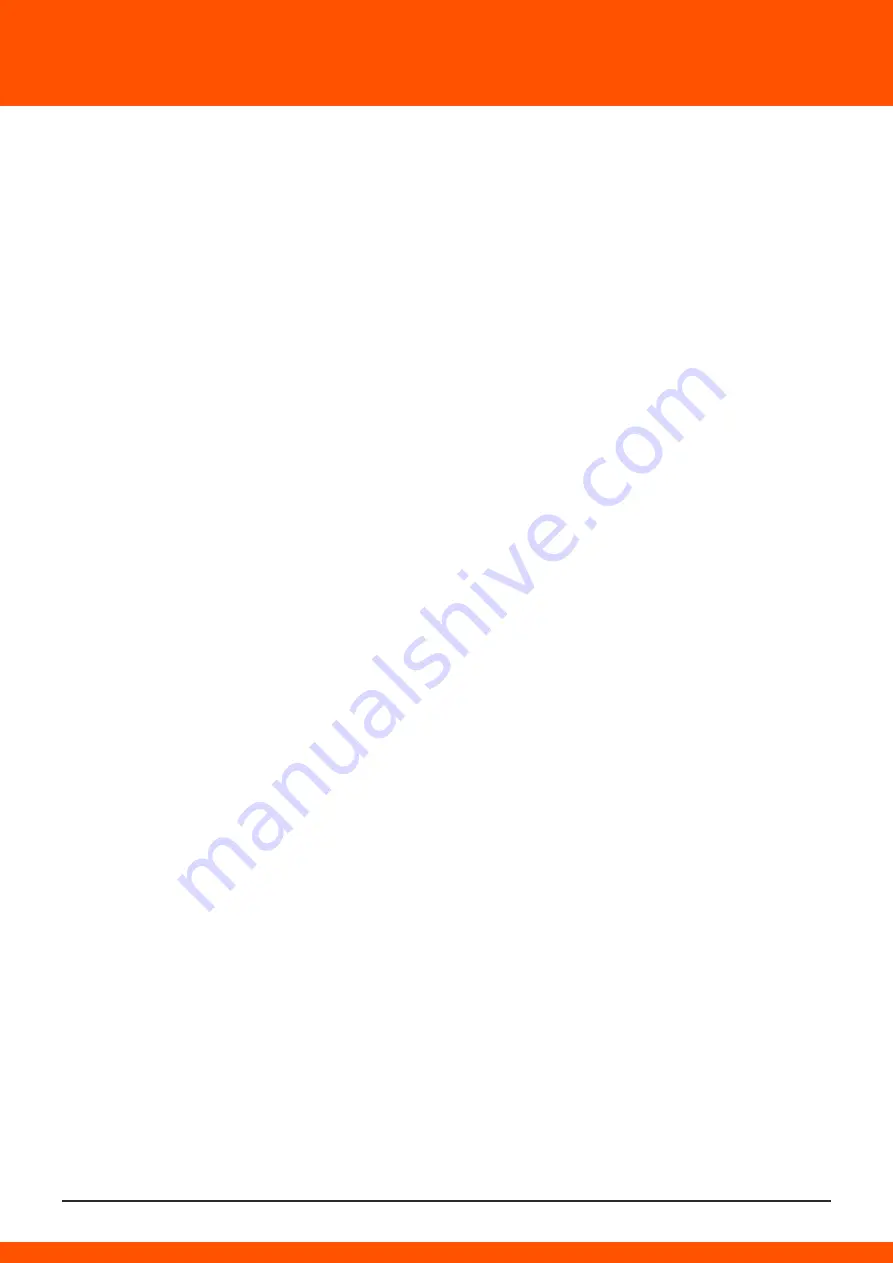
10
1. INTRODUCTION
You’ve received the air compressor you had longed for Probably you’ve already had knowledge of it,
but in order to make it serve you always in a good condition, read the manual carefully please.
Operate according to the manual, you’ll get the best economy and efficiency from your new com-
pressor.
Check the compressor when you received it
(1)Make sure it is the model and specification you ordered.
(2)Check the spare parts according to the list attached.
(3)If damage and loosening occurs during the transport, contact the seller please. He will give you a
satisfied solution.
2. SAFETY INFORMATION
2.1 Specified conditions of use
This machine is intended to generate compressed air tools.
Any use for medical purposes, food processing as well as filling of oxygen cylinders for breathing
equipment is not permitted.
Explosive, combustible gases or gases detrimental to health may not be compressed. Operation in
hazardous locations is not permitted.
Any other use is not as specified. Use not as specified, alteration of the machine or use of parts that
are not approved by the equipment manufacturer, can cause unforeseeable damage!
Children, juveniles and persons not having been instructed in its usage are not permitted to operate
this machine and any air tools connected to it.
2.2 General safety information
1 )Keep bystanders, particularly children, out of the work area. Do not permit other persons to touch
the tool or power cable while the machine is running.
(2) Don’t perch on the machine,or use it to hold you
(3) Before each use,inspect compressed air system and electrical components for signs of damage,-
deterioration,weakness or leakage,repair or replace damaged parts before using the equipment
(4) Observe the status accident insurance institution regulations and regulations for the prevention
of accidents pertaining to the operation of air compressors and air tools, where applicable.
(5) To prevent the motor damage by overloading, the compressed air in tank should be released
before operation.
(6) The cylinder head and pipes must be very hot during working, this is normal phenomenon.
(7) To ensure safety, be sure to switch off the power after work or power failure during work.
(8) Be sure to install air switch before connect the power
General hazard!
(1) Keep your work area tidy,a messy work area easy to lead accidents
(2) Consider environmental conditions.
(3) Keep work area well bright.
(4) Do not operate the machine near inflammable liquids or gases.
Danger! Risk of electric shock!
(1) Do not expose the machine to rain.
(2) Do not operate the machine in damp or wet environment.
(3) Prevent body contact with earthed objects such as radiators,pipes,cooking stoves or refrigera-
tors when operating this electric tool
(4) Do not use the power cable for any purpose it is not intended for.
Risk of personal injury by escaping compressed air and parts hurled about by escaping air!
(1) Never direct compressed air against persons or animals!
(2) Ensure all air tools and accessories used are designed for the working pressure or are supplied
via a pressure regulator.
(3) Please note that, when disconnecting the quick coupler, the compressed air contained in the
pressure hose will escape all of a sudden. You should therefore firmly hold the air hose when
disconnecting it
(4) Ensure all screwed connections are fully tightened at all times.
(5) Do not attempt to repair the machine yourself! Only trained specialists are permitted service or
repair compressors
Hazard generated by oil saturated compressed air!
(1) Use oil saturated compressed air only for air tools requiring such supply.
(2) Do not use an air hose used to supply compressed air containing oil to supply air tools not desig-
ned for operation on compressed air containing oil.
(3) Do not fill tires with compressed air containing oil.
Risk of burns from the surfaces of parts carrying compressed air!
Let machine cool off before servicing.
Risk of personal injury and crushing by moving parts!
Please note that the compressor will start automatically when the pressure falls off to minimum!-dis-
connect from power supply prior to any servicing
Hazard generated by insufficient personal protection gear!
(1)Wear hearing protection.
(2)Wear safety glasses.
(3)Wear mask respirator when work generates dust or mist detrimental to health.
(4)Wear suitable work clothes. When working outdoors wearing of nonslip shoes is recommended.
2.3 Safety devices
Safety valve
The safety valve is incorporated into the pressure switch unit,the safety valve opens if the max,per-
missible pressure is exceeded,Will be not accepted adjustment
3. OPERATION
(1) Working place:
*install the compressor in a well ventilated, probably dust and moisture free environment.
*a bright place where oil can be easily added.
*a level place for assemble and check the compressor easily. The belt side should near the wall, but
a distance at least 30cm for the fan’s normal work.
(2)Install wheel
The wheel install includes the following:
-4pcs Wheel(15)
-4pcs key(14)
-4pcs spring washer(16)
Install wheel as illustrated
(3)Install air intake filter
Install air filter on air intake as illustrated
(4)Motor
*Install your own motor that match the compressor.
*Install the V-belt as showed in the figure.
*Adjust belt tension.
The belt must a give of about 10-15mm with a space at it’s center, as showed in the figure:
**Such things may happen if the belt is too tight:
increase the loading, motor get hot, waste energy and
break the belt.
**Such things may happen if the belt is too loose:
sliding produce high temperature, damage the belt,
irregular revolution.
(5)Filling with oil
Remove the oil plug (10)
Fill with oil up to the centre of the level indicator(11)
Install back the oil plug(10)
*The lubricant oil should be of oilness and contain inhibitor, not easy to be oxidized, get densified or
foamed, low residual carbon, hight flash point.
*Oil level should maintain in the red scope of the level glass. Too much oil is a waste, also adsorb
carbon to the valve. Too less oil may cause damage or tear and wear.
*Change oil when it get dark or when greasy dirt is found(about 300 hours operation)
*Loosen the outlet bolt under the bottom of crank case to let the oil out, use paperboard or some-
thing else to facilitate its out, incline forward the compressor also do some help. When all old oil is
out. Tighten the bolt and add new oil to the middle level of the red scope in level glass(to prevent
leakage, apply anti-oxygen glue to the bolt).
*Do not add new oil during running.
*Do not use high viscosity lubricant oil or other waste oil.
(6) Check drain valve
Check to see that the condensate drain’s screw is closed
The working pressure of safety values should be 0.5 - 1kg/ cm² higher than other system.
(7) Mains connection
Danger!High voltage
Operate machine in dry envi-ronment only
Operate machine only on a power source complying with the following requirements
-outlets properly installed, earthed and tested;
-fuse protection in accordance with the Technical Specifications.
Position power cable so it does not interfere with the work and is not damaged.
Always check to see that the machine is switched OFF before plugging in.
Protect power cable from heat, aggressive liquids and sharp edges.
Use only extension cables with sufficient lead cross section(see” Technical Specifications”).
Do not stop the compressor by unplugging, but switch OFF using the switch.
Unplug after use.
(8)Generating compressed air
1.Start compressor(1)and wait until the max. Tank pressure is reached(compressor shuts off).
The tank pressure is indicated by the tank pressure gauge(2).
2. Set pressure regulator(4)to required working pressure. The current working pressure is indicated
by the regulated pressure gauge(17).
Caution!
The regulated pressure may not be set higher than the max.working pressure of the connected air
tools
Connect air hose to compressed air outlet(66)
Connect air tool you are now ready to work with the air tool
Switch the compressor OFF(1) if you do not continue working immediately afterwards,Unplug after
switching OFF
4. GENERAL VIEW AND MAIN COMPONENTS
1. Pressure switch
2. Pressure gauge
3. Quick connector
4. Regulator valve
5. Drain valve
6. Crankcase
7. Air filter
8. Motor
9. Tank
No Parts name
1 Bolt
2 Spring washer
3 Connecting three holes
4 Cylinder head
5 Cylinder head gasket
6 Valve plate
7 Valve sheet
8 Valve plate aluminum gasket
9 Valve sheet
10 Valve plate
11 Valve plate gasket
12 Cylinder
13 Cylinder gasket
14 Bolt
15 Spring washer
16 Piston ring
17 Snap spring
18 Piston pin
19 Piston
20 Connecting rod
21 Oil needle
22 Bolt
23 Connecting pipe
24 Elbow
25 Air filter
26 Bolt
27 Spring washer
28 Plain washer
29 Pulley
30 Bolt
31 Spring washer
32 Front cover
33 Front cover gasket
34 Oil seal
35 Bearing
36 Crank
37 Bearing
38 Crank case
39 Bolt
40 Oil leveler
41 Oil plug
42 Nut
43 Spring washer
44 Bolt
45 Motor
46 Motor pulley
47 Motor pin
48 Nut
49 Plain washer
50 Spring washer
51 Bolt
52 Terminal
53 Lead wire
54 Insulating sheath
55 Check valve
56 Elbow
57 Unloading tube
58 Exhaust pipe
59 Air tank
60 Drain valve
61 Wheel
62 Plain washer
63 Pin
64 Pressure switch
65 Safety valve
66 Pressure gauge
67 Air cock assembly
68 Ball valve
69 Safety net
70 Nut
71 Spring washer
72 Plain washer
73 Bolt
74 Belt
75 Plug cord
Содержание DAAX500L
Страница 14: ...13 8 TROUBLES AND REMEDIES LIST OF GOODS The air compressor can be turned...
Страница 15: ...14...
Страница 16: ...15...
Страница 17: ...16...
Страница 20: ...www daewoopowerproducts com Manufactured under license of Daewoo International Corporation Korea...