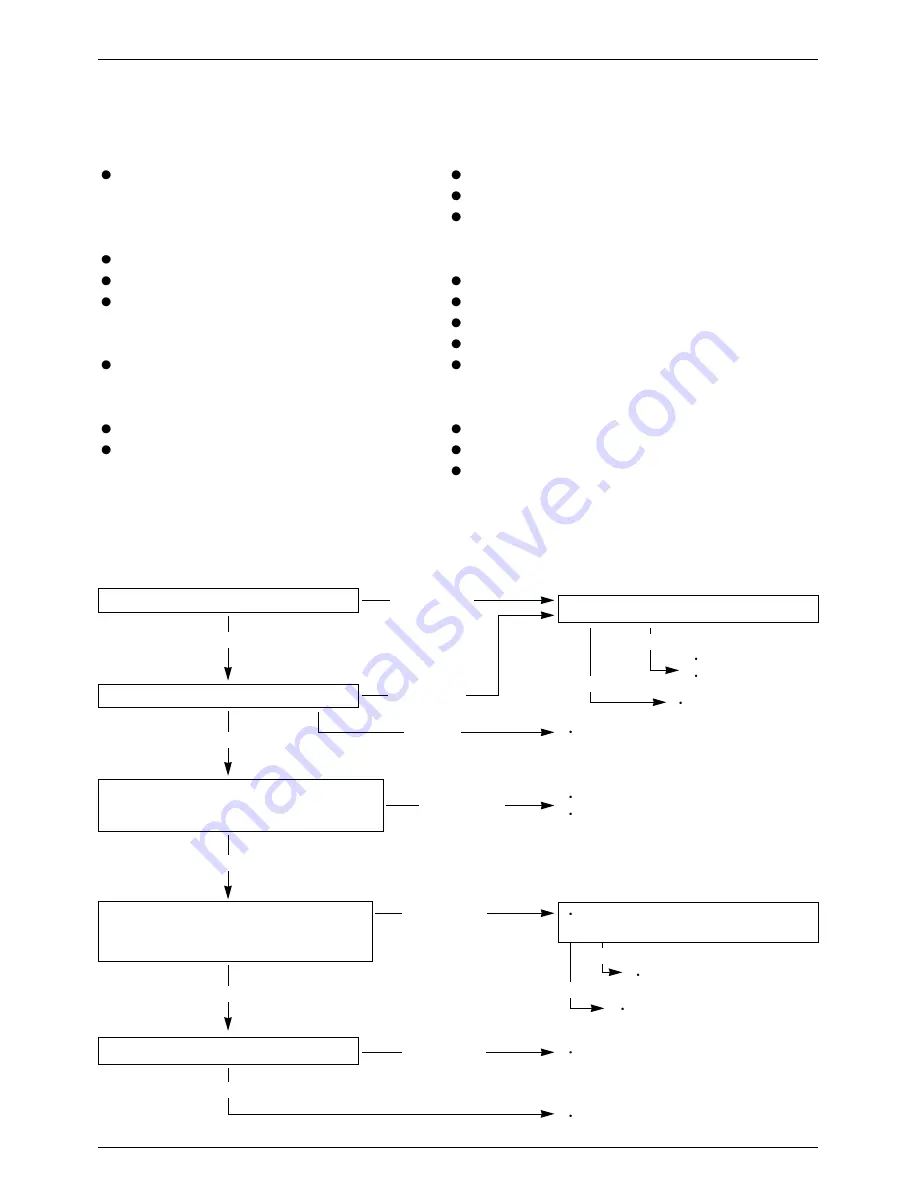
15-3
BATTERY/CHARGING SYSTEM
TROUBLE SHOOTING
No power (Key turned on)
Low power (Engine running)
Dead battery.
Battery undercharged.
-Low fluid level.
Battery is failing.
-Low specific gravity.
Charging system failure.
-Charging system failure.
Disconnected battery cable.
Intermittent power
Main fuse burned out.
Loose battery connection.
Faulty ignition switch.
Loose charging system connection.
Loose starting system connection.
Low power (Key turned on)
Loose connection or short circuit in ignition system.
Battery undercharged.
Loose connection or short circuit in lighting system.
-Low fluid level.
-Low specific gravity.
Charging system failure
Charging system failure.
Loose, broken or shorted wire or connection.
Loose battery connection.
Faulty regulator rectifier.
Faulty A.C generator.
CHARGING SYSTEM
Measure battery current leakage.
Check the regulator rectifier.
Battery is failing
Open circuit in wire harness.
Poorly connected coupler.
Shorted harness wire.
Faulty ignition switch.
Faulty regulator rectifier.
Check the charging coil of theA.C
generator.
Faulty regulator rectifier.
Faulty battery.
Inspect the charging voltage.
Check the voltage between the battery line and
ground wire of regulator rectifier.
Check the resistance of the charging coil at
the charging coil line of regulator rectifier
coupler.
Check the regulator rectifier.
CORRECT
INCORRECT
INCORRECT
CORRECT
Poorly connected A.C generator coupler.
Faulty charging coil.
ABNORMAL
NORMAL
ABNORMAL
INCORRECT
ABNORMAL
OVER 15V
14~15V
UNDER 14V
NORMAL
NORMAL
CORRECT
Содержание BESBI SC125 -
Страница 1: ......
Страница 11: ...1 9 SERVICE INFORMATION SERIAL NUMBER LOCATION ENGINE SERIAL NUMBER LOCATION FRAME SERIAL NUMBER LOCATION...
Страница 36: ...MEMO...
Страница 56: ...MEMO...
Страница 60: ...7 0 LH CRANKCASECOVER KICKSTARTER CONTINUOUSLYVARIABLE TRANSMISSION...
Страница 65: ...Install the LH crankcase cover 7 5 LH CRANKCASECOVER KICKSTARTER CONTINUOUSLYVARIABLE TRANSMISSION...
Страница 77: ...MEMO...
Страница 78: ...8 0 A C GENERATOR STARTER CLUTCH...
Страница 87: ...MEMO...
Страница 88: ...9 0 CYLINDER HEAD VALVES...
Страница 104: ...10 0 CYLINDER PISTON...
Страница 111: ...MEMO...
Страница 112: ...11 0 TRANSMISSION CRANKSHAFT CRANK CASE...
Страница 123: ...MEMO...
Страница 124: ...MEMO...
Страница 136: ...MEMO...
Страница 144: ...MEMO...
Страница 154: ...CHARGING DEVICE LOCATION 15 2 BATTERY CHARGING SYSTEM A CGENERATOR C D I UNIT REGULATOR RECTIFIER KEY SET IGNITION UNIT...
Страница 160: ...16 2 IGNITION SYSTEM IGNITION DEVICES LOCATION A CGENERATOR C D I UNIT BATTRY REGULATOR RECTIFIER KEY SET IGNITION UNIT...
Страница 164: ...MEMO...
Страница 166: ...17 2 STARTER SYSTEM STARTER DEVICES LOCATION A CGENERATOR C D I UNIT BATTRY REGULATOR RECTIFIER KEY SET IGNITION UNIT...
Страница 178: ...MEMO...
Страница 184: ...MEMO...
Страница 185: ...20 WIRING DIAGRAM G Gr B G O Lb Lb I GNI TI ON SWI TCH G O COMBI MERER ASS Y...
Страница 186: ...I GNI TI ON SWI T CH FUEL UNI T ENGI NE STOP SWI T CH PASS...
Страница 187: ...SERVICEMANUAL 2007 09 PRINTED 2007 09 PUBLICATION...
Страница 188: ......