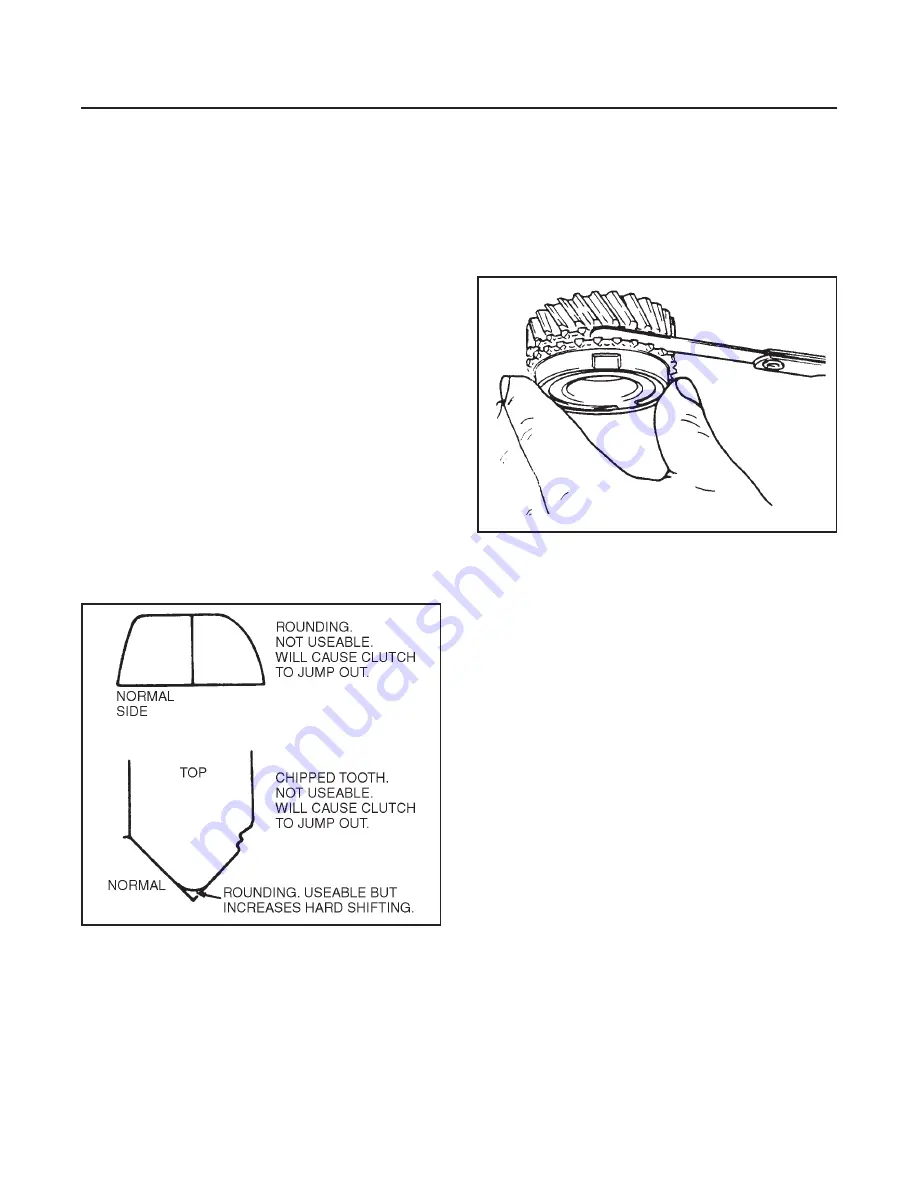
SPLINE TEETH
Check for broken or chipped spline teeth. Small chips
may be blend-repaired in same manner as gear teeth.
If any spline tooth is broken, the part must be rejected.
Spline teeth will not show contact patterns as gear
teeth do.
However, they may show evidence of step wear
which is cause for rejection.
GEAR REPAIR
Parts which are rejected by inspection are to be
replaced, unless repair procedures specified in the
following paragraphs, or other obvious minor repair,
will restore the part to complete serviceability.
Repair is limited to blend-repair of chips. See Figure
4H-17.
Blend repair chips using a suitable hand-held, high
speed grinding tool.
Blend chip into surrounding base metal, but do not
remove any more metal than necessary.
Blend all sharp edges into smooth contour. Sharp
edges may chip again or develop cracks.
Use a suitable abrasive stone to remove burrs. Be
careful to remove only raised material, not base metal.
SYNCHRONIZER RINGS
Fit the rings to the cone of the gear (input gear, or
“third,” “second” or “low” gear), and measure the
clearance between the two at the peripheral teeth, as
shown in Figure 4H-18. Standard clearance is 0.039
to 0.055 inch (1.0 to 1.4 mm). If the clearance is less
than 0.02 inch (0.5 mm) the ring and gear should be
replaced.
Inspect the external cone (of the gear) and internal
cone (of the ring) for abnormal wear. Be sure that the
contact patterns on these surfaces indicate uniform
full-face contact, and that the surfaces are free from
any wavy wear. A badly worn ring or gear must be
replaced.
Proper synchronizing action on gear shifting can be
expected only when the ring-to-gear clearance and
the condition of cone surfaces, are satisfactory.
RING (EXTERNAL) AND
GEAR SLEEVE (INTERNAL) TEETH
Synchronizer rings and hubs have three slots each, in
which the keys are carried as backed by expanding
springs, so that the hub and its two rings, one on each
end, are capable of running together. Since the
sleeve is engaged by its internal teeth with the hub,
as if the two were splined together, the sleeve also
runs with the hub and rings.
In meshing action, the sleeve is pushed (by the shifter
fork) to one side, so that it slides axially on the hub,
pushing the ring toward the cone surface of the gear.
This push is transmitted by the three keys, which are
lightly gripped by the sleeve.
By the friction between the gear cone and the ring
cone (internal), the ring begins to rotate but is
opposed by the hub because of the keys. In other
words, the ring is (at this time) twisted, while the
sleeve is advancing further to push the ring fully
against the gear cone. Since the ring is unable to
slide along any further, the sleeve lets go of the keys
and rides over to the ring. At this moment, the initial
contact between the chamfered ends of teeth of the
ring and those of internal teeth of the sleeve occurs.
This contact is such that the internal teeth of the
sleeve align themselves to those of the ring. When
DRIVE TRAIN
SECTION 4H. TRANSMISSION
(4-CYLINDER 970 GASOLINE OR DIESEL ENGINES)
4H-10
Figure 4H-17. Clutch Tooth Inspection
Figure 4H-18. Synchronizer Ring-to-Gear Clearance
Содержание TURF-TRUCKSTER
Страница 31: ...ENGINE SECTION 3D DIESEL ENGINE 3D 3 3D Figure 3D 2 Radiator and Cooling System Repair...
Страница 41: ...ENGINE SECTION 3E GASOLINE ENGINES 3E 6 Figure 3E 5 Radiator and Cooling System 4 Cylinder Engine Suzuki 970...
Страница 54: ...DRIVE TRAIN SECTION 4C DRIVE SHAFT 4C 3 4C Figure 4C 3 Drive Shaft Disassembly and Reassembly...
Страница 102: ...DRIVE TRAIN SECTION 4I REAR AXLE 4I 4 Figure 4I 4 Axles and Axle Housings...
Страница 107: ...DRIVE TRAIN SECTION 4I REAR AXLE 4I 9 4I Figure 4I 11 Auxiliary Transmission Disassembly...
Страница 110: ...DRIVE TRAIN SECTION 4I REAR AXLE 4I 12 Figure 4I 13 Auxiliary Transmission Reassembly...
Страница 112: ...DRIVE TRAIN SECTION 4I REAR AXLE 4I 14 Figure 4I 14 Differential and Axle Assembly Installation...
Страница 124: ...BRAKE SYSTEM SECTION 5E MASTER CYLINDER 5E 2 Figure 5E 2 Master Cylinder Connections...
Страница 131: ...STEERING SECTION 6C STEERING SYSTEM 6C 4 Figure 6C 4 Steering Column...
Страница 137: ...STEERING SECTION 6D STEERING GEAR 6D 4 Figure 6D 5 Rack Piston...
Страница 143: ...STEERING SECTION 6E STEERING PUMP 6E 2 Figure 6E 2 Steering Pump Repair...
Страница 163: ...HYDRAULICS SECTION 8G BOX CYLINDER 8G 2 Figure 8G 2 Seal Kit Installation...
Страница 168: ...HYDRAULICS SECTION 8J INSTRUMENT TEST 8J 3 8J Figure 8J 2 Standard Hydraulic System Pump Flow Test...
Страница 170: ...HYDRAULICS SECTION 8J INSTRUMENT TEST 8J 5 8J Figure 8J 3 Selector Valve Test Steps 13 to 20...
Страница 171: ...HYDRAULICS SECTION 8J INSTRUMENT TEST 8J 6 Figure 8J 4 Selector Valve Test Steps 21 to 29...
Страница 173: ...HYDRAULICS SECTION 8J INSTRUMENT TEST 8J 8 Figure 8J 5 Lift Valve Test Steps 30 to 36...
Страница 174: ...HYDRAULICS SECTION 8J INSTRUMENT TEST 8J 9 8J Figure 8J 6 Lift Valve Test Steps 37 to 41...
Страница 176: ...HYDRAULICS SECTION 8J INSTRUMENT TEST 8J 11 8J Figure 8J 7 Cylinder Test...
Страница 178: ...HYDRAULICS SECTION 8J INSTRUMENT TEST 8J 13 8J Figure 8J 8 Pump Section 1 Flow Test...
Страница 179: ...HYDRAULICS SECTION 8J INSTRUMENT TEST Figure 8J 9 Bottom Selector Valve Test 8J 14...
Страница 181: ...HYDRAULICS SECTION 8J INSTRUMENT TEST 8J 16 Figure 8J 10 Lift Valve Test...
Страница 183: ...HYDRAULICS SECTION 8J INSTRUMENT TEST 8J 18 Figure 8J 11 Cylinder Test...
Страница 185: ...HYDRAULICS SECTION 8J INSTRUMENT TEST 8J 20 Figure 8J 12 Pump Section 2 Flow Test...
Страница 186: ...HYDRAULICS SECTION 8J INSTRUMENT TEST 8J 21 8J Figure 8J 13 Bottom Selector Test...
Страница 251: ...ATTACHMENTS SECTION 12C MECHANICAL PTO 12C 2 Figure 12C 3 Mechanical PTO Exploded View...
Страница 259: ...MISCELLANEOUS SECTION 14A PRECAUTION DECAL LOCATIONS 14A 1 14A PRECAUTION DECAL LOCATIONS...
Страница 261: ...MISCELLANEOUS SECTION 14B CONVERSION CHARTS 14B 1 14B MILLIMETERS TO DECIMALS...
Страница 262: ...MISCELLANEOUS SECTION 14B CONVERSION CHARTS 14B 2 DECIMALS TO MILLIMETERS FRACTIONS TO DECIMALS TO MILLIMETERS...