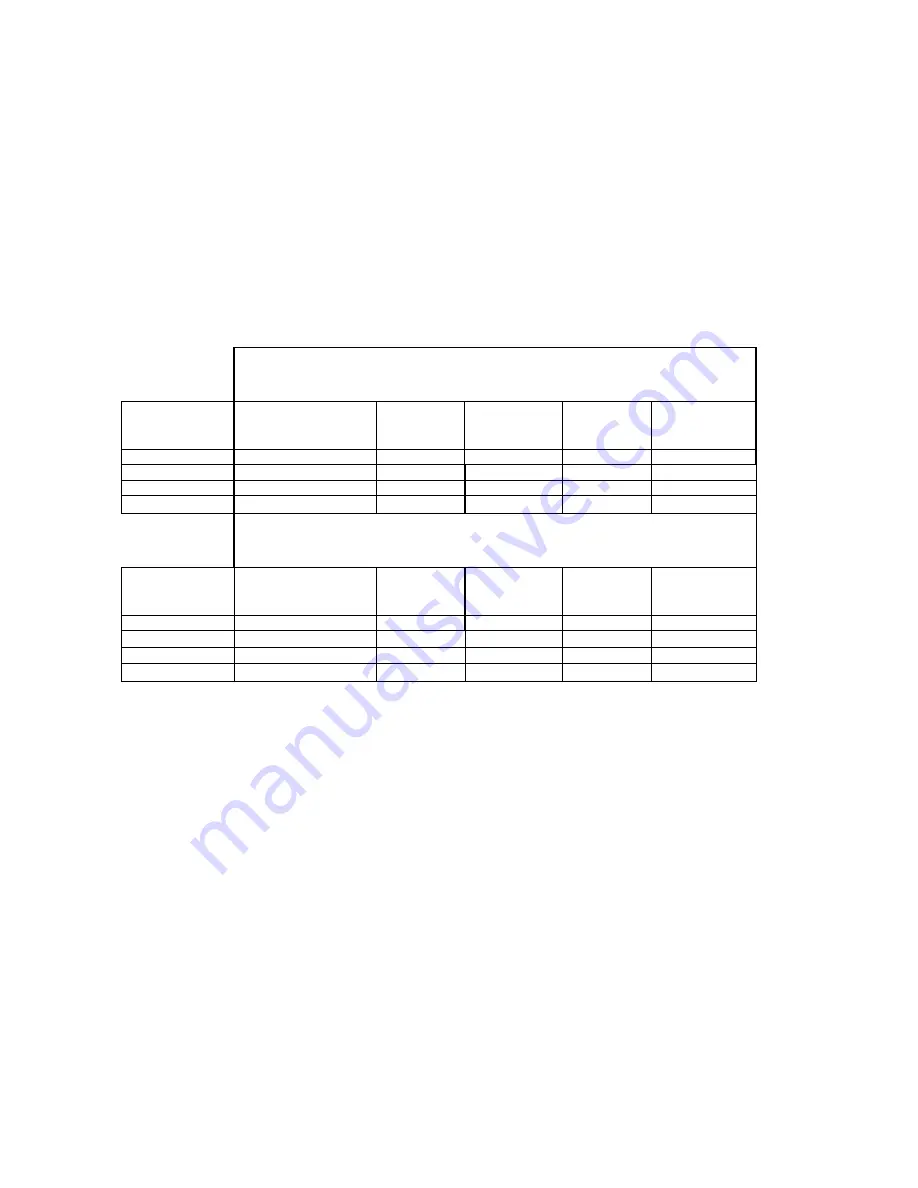
CAUTION
Follow all warnings and cautions on your formulation label. Do not attempt to apply
any formulation at a rate greater than what is specified on the formulation label. This
includes driving your vehicle at a rate slower than what is specified.
TYPICAL FLOW RATES FOR INSECTICIDES
TABLE 1
FLOW RATE
VEHICLE
SPEED
MPH
DURSBAN
(CHLORPYRIFOS)
OZ/MIN
DOW MFC
OZ/MIN
PYRETHRIN
OZ/MIN
D1BROM
OZ/MIN
TECHNICAL
MALATHION
OZ/MIN
5
1.4-2.7
.33 - .66
2.0-2.5
3.0-6.0
1.0-2.1
10
2.7-5.3
.66-1.33
4.0 - 5.0
6.0-12.0
2.0-4.3
15
—
1.0-2.0
6.0-7.5
9.0-18.0
3.0-6.5
20
—
—
8.0-10.0
—
4.0-8.6
FLOW RATE
VEHICLE SPEED
KM/HR
DURSBAN
(CHLORPYRIFOS)
ML/MIN
DOW MFC
ML/MIN
PYRETHRIN
ML/MIN
DIBROM
ML/MIN
TECHNICAL
MALATHION
ML/MIN
8
42-81
10-20
60-75
90-180
30-63
16
81 -159
20-40
120-150
180-360
60-129
24
—
30-60
180-225
270 - 540
90-195
32
—
—
240 - 300
—
120-258
CAUTION
The above rates are examples of typical application rates found on their respective
formulation labels. Refer to the label of your formulation to determine the actual
application rate before calibrating your machine to any of the above flow rates.
Once the flowability of the formulation to be sprayed has been determined, and the
formulation pump has been calibrated, select one of the three tables (next page)
that is closest to the flowability of the formulation to be sprayed (34, 40 or 88
seconds). Then match the closest flow rate in the left hand column with the flow rate
specified on the formulation label. A boom pressure can then be selected that will
produce a particle size in accordance with the formulation label. Remember, with a
constant flow rate supplied to the nozzle system, increasing nozzle boom pressure
will decrease particle size.
21
Содержание 2742
Страница 53: ...ENGINE WIRING DIAGRAM 53 ...
Страница 54: ...REMOTE CONTROL BOX SCHEMATIC 54 ...
Страница 55: ...55 PUMP AND CONTROL SCHEMATICS ...
Страница 56: ...56 POWER REGULATOR SCHEMATICS ...
Страница 57: ...57 MOTOR CONTROL SCHEMATICS ...
Страница 58: ...58 TACHOMETER DECODE SCHEMATICS ...
Страница 59: ...59 SPEED DECODE SCHEMATICS ...
Страница 60: ...4 MPH SWITCH SCHEMATICS 60 ...
Страница 62: ...62 ...
Страница 63: ...63 ...
Страница 64: ...64 ...
Страница 65: ...CURTIS DYNA FOG Ltd WESTFIELD INDIANA U S A MAXI PRO TM 4 MODEL 2742 SERIES 5 65 ...
Страница 71: ...71 ...
Страница 73: ...73 ...
Страница 77: ...SAMPLE CONNECTIONS USING STEEL PLASTIC GRIPPER NUT 48 77 ...
Страница 78: ...78 ...
Страница 79: ...79 ...