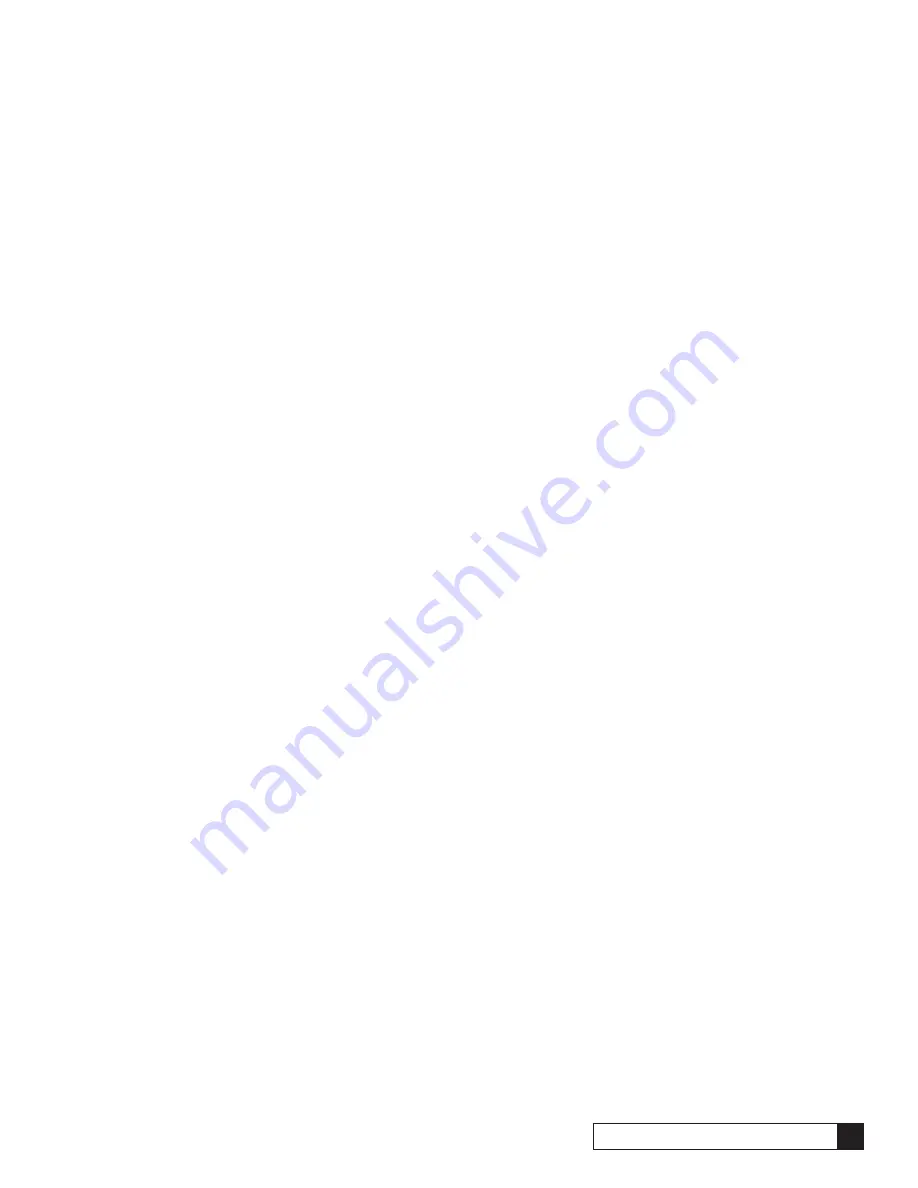
Circuit Board Troubleshooting
33
Listed below are some other circuit board problems and their explanations:
–
Board skips the service position or only stops for a second in service before advancing to the backwash position
Board has been armed for regeneration. Let the board time out of all three cycles or reset and reprogram the board. Resetting
the board can be done by connecting or disconnecting the meter cable.
–
Motor goes round and round
Only one of two things can happen when this is the case; it can find its desired position or it gives you an error code. So, LET
IT RUN until you find out which will occur.
•
If the motor still runs or there is power to motor after the error code is displayed, then the triac is likely bad – change the
board.
•
If the error code is displayed and the motor is stopped (no power to the motor), check switches, cam and wire harness
– the board got a signal it wasn’t supposed to or a connection failed.
A word about triacs –
A triac is an electronic switch and can “latch on” when it becomes overheated from a laboring motor (tight seal pack). It may
operate properly when it cools down. A continuously running motor could be caused by an overheated triac. Checking the seal
pack and voltage draw and allowing the triac to cool down could give you favorable result and prevent the need to change the
board. Otherwise, when it is sent to Returned Goods it could test good and be returned.
You clear an error code and it starts into regeneration
It was either in regeneration or has kept track of time since the error code occurred and it’s trying to finish the regeneration. Reset
and reprogram the board.
The board repeatedly defaults, resets or gains time
Look at the power supply or source. Most of these issues are caused by the power source, so-called “dirty power” having noise
interference or incorrect voltage. This could be erratic fluctuations caused by other heavy power draws, poor wiring, low voltage
wiring running along high voltage, having active electrical storms that causes “corruption” of the EEPROM. Consider the use of a
surge protector or an uninterruptible power supply after you see this repeatedly.
If you suspect the power source is causing problems, take a voltage reading at the outlet, at the power connection on the board,
and on the motor leads while the motor is running. We are looking for a consistent range of 108-132 volts at the receptacle and
22-28 volts on the board. Also, the wall transformer is only used to step down the voltage; it is not used for protection or filtering
the power source.
Test Mode
In this mode the control can be put through a performance test to verify the operation of the board components. Moving dip #1 from
service to test mode enters the test mode; the motor output should turn off (if it was on) upon entering test mode.
When entering test mode all program settings and statistical data should be stored in EEPROM. The test sequence is to follow
the description as found in the table below. Upon exiting test mode, if a device connection is different (flow meter connected or
disconnected) or a DIP switch setting is changed from the condition that was present when entering test mode, the control should
behave as if the change was made while out of test mode. For example, if a flow meter was added and not removed while in test
mode, the control shall load the flow meter defaults when exiting test mode.
Содержание Iron-Cleer
Страница 4: ... Culligan Iron Cleer Water Filters ...