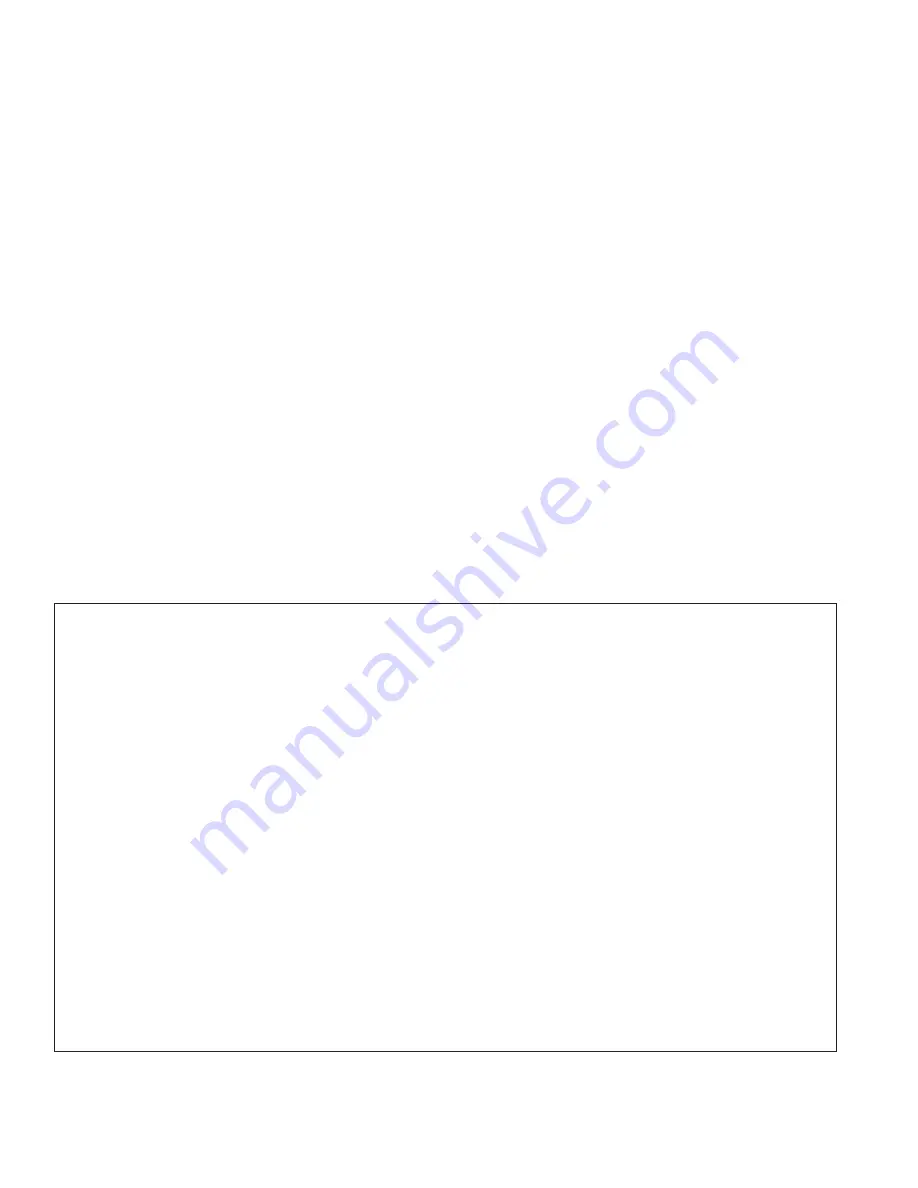
34
14) Place the boiler back in operation using the procedure outlined in “Start-up”. Check the pilot line and any other gas piping
disturbed during the inspection process for leaks.
Heat Exchanger Cleaning Procedure
1)
Turn off electrical power and gas supply to the boiler
2)
Disconnect the damper and vent connector from the boiler.
3) Remove the upper front and top jacket panels. If possible, remove the rear and left side jacket panels
4)
Remove the burners.
5)
Remove the blocked vent (“spill”) switch
6)
Remove the ¼-20 nuts and washers holding the flue collector onto the heat exchanger.
7)
Carefully remove the flue collector gasket strips and set them aside.
8)
Remove the flue collector from the heat exchanger.
9)
Clean the flue passageways using a stiff bristle brush. Be certain that all foreign material is removed from the gaps
between the pins
10) Clean the bottom surfaces of the heat exchanger
11) Put a light in the combustion chamber and look through the flue passages from the top to verify that they have been
thoroughly cleaned.
12) Replace the flue collector gasket strips. If desired, RTV silicone sealant with a 500F intermittent duty temperature may be
substituted for this rope gasket. The flue collector must be thoroughly sealed to the heat exchanger.
13) Replace the ¼-20 nuts and washers that hold down the flue collector
14) Reattach all the jacket components.
15) Reinstall burners, being careful to put the pilot main burner in its original location.
16) Replace the blocked vent switch.
17) Reconnect the damper and vent system.
WARNING
SOOT DEPOSITS IN THE FLUE PASSAGES ARE A SIGN THAT THE BOILER MAY BE OPERATING AT HIGH
CARBON MONOXIDE (CO) LEVELS. AFTER CLEANING THE BOILER OF SOOT DEPOSITS, CHECK THE CO
LEVEL IN THE FLUE GAS TO INSURE THAT THE BOILER IS OPERATING PROPERLY.
If it is necessary to check CO, use a combustion analyzer, or other instrument which is designed to measure CO in flue gas.
A CO “sniffer” designed for testing CO levels in ambient air cannot be used to check boiler combustion. Take a flue gas
sample by inserting a sample probe through the draft diverter opening and into the flue collector so that the sample is taken
in the area directly over the heat exchanger. Do not take a sample until the boiler has been firing for at least five minutes.
A normal CO reading for a BSI series boiler is less than 50ppm (0.005%). A reading of more than 100ppm (0.01%) is indica-
tive of a combustion problem.
Some causes of excessive CO include:
•
Incorrectly sized main burner orifice for the altitude at which boiler is installed
•
Crooked or out-of-round orifice holes (never attempt to drill orifice for this boiler in the field)
•
Partially plugged flue passages
•
Improper manifold pressure
•
Foreign material in burner venturis or burner ports
•
Leak in seal between flue collector and heat exchanger
•
Inadequate supply of combustion air
33
Содержание BERMUDA BSI069
Страница 43: ...43 42...
Страница 45: ...45 44...
Страница 47: ...47 46...
Страница 49: ...49 48 FIGUREA1 BASE HEATEXCHANGER FLUE COLLECTORASSEMBLY...
Страница 51: ...51 50 FIGUREA2 JACKETINSTALLATION...
Страница 53: ...53 52 FIGUREA3 TAPPING LOCATIONS SEE TEXT FOR TAPPING USES...