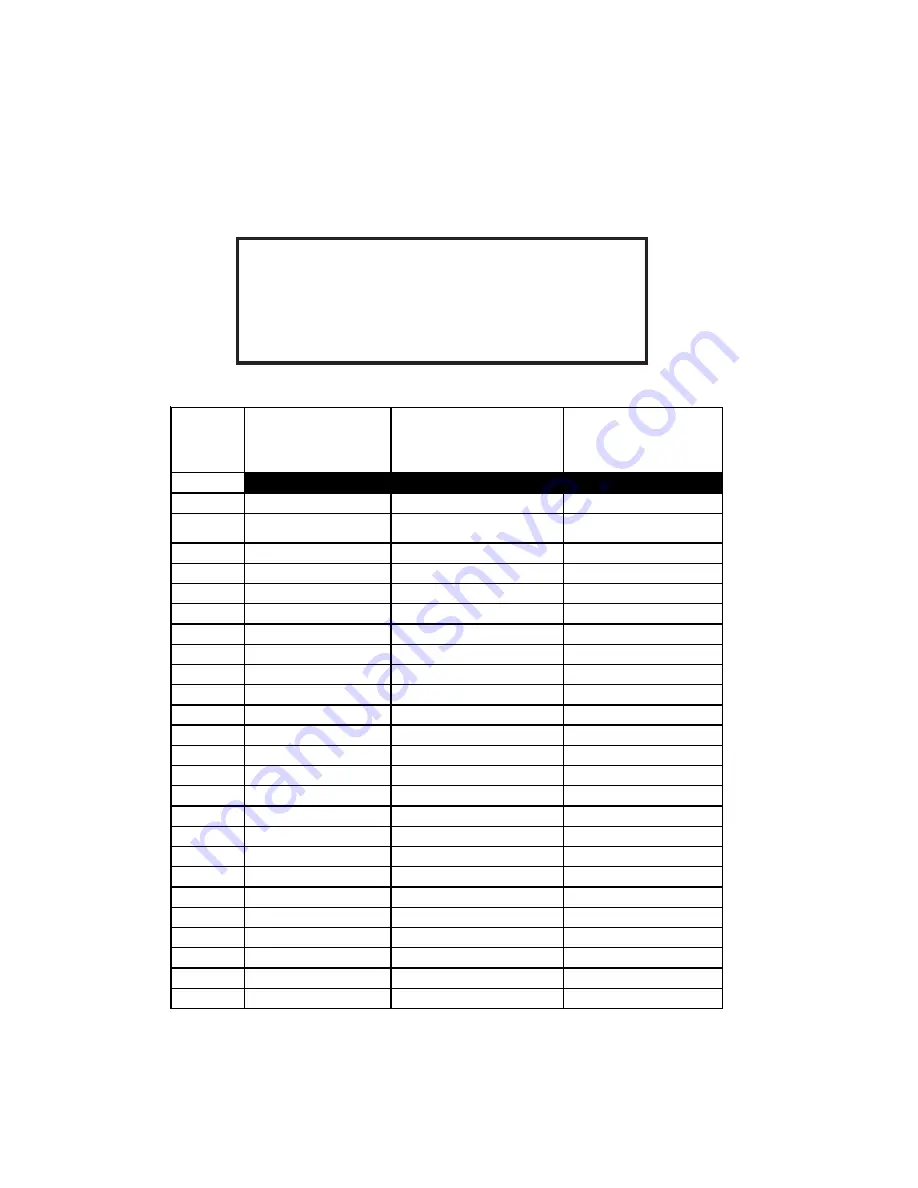
26
6)
Lateral venting should slope upwards towards the chimney not less than one inch in four feet. No portion of vent pipe
should run downward or have sags. Vent pipe must be securely supported.
7)
The connector rise coming off the boiler should be as tall as possible, while still maintaining the proper
clearance from the horizontal vent connector to combustibles and the proper pitch called for in (6) above.
8)
Lateral vent pipe should be installed above the bottom of the chimney to prevent blockage.
9)
Lateral vent pipe must be inserted flush with inside face of the chimney liner and the space between vent pipe and
chimney sealed tight.
24
Table 4: Sizing For Vent Systems Outside The Scope Of The National Fuel Gas Code Venting Tables
IMPORTANT: READ THE ENTIRE VENT SECTION
AND REFER TO FIGURE 20 BEFORE
ATTEMPTING TO USE THIS CHART
32-475*
32-570
20
9 1/2
12
32-665
20
9 1/2
12
32-760
20
10
12
32-855
20
10 1/2
12
32-950
20
11
14
32-1045
20
11 1/2
14
32-1140
20
12
14
32-1235
20
12 1/2
14
32-1330
20
13
16
32-1425
20
13 1/2
16
32-1520
20
14
16
32-1615
20
14 1/2
16
32-1710
20
14 1/2
18
32-1805
20
15
18
32-1900
20
15 1/2
18
32-1995
20
16
18
32-2090
20
16 1/2
18
32-2185
20
17
20
32-2280
20
17 1/2
20
32-2375
20
18
20
32-2470
20
18 1/2
20
32-2565
20
19
20
32-2660
20
19 1/2
22
32-2755
20
19 1/2
22
32-2850
20
20
22
* USE NATIONAL FUEL GAS CODE TO SIZE 32-475 VENTING
MODEL
MIN. COMMON VENT
INSIDE DIA. (D), in
MIN. CHIMNEY
HEIGHT (H), ft
MAX. LATERAL
COMMON VENT (Lm), ft
Содержание 32 Series and
Страница 2: ...2 ...
Страница 4: ...4 Figure 1 Base Model General Configuration 2 II Specifications ...
Страница 13: ...13 11 Figure 4 Multiple Base Assembly ...
Страница 15: ...15 13 Figure 6 Assembly Of Sections Figure 5 Use Of Nipple Gauge ...
Страница 20: ...20 18 Figure 14 Exploded View Of Jacket Assembly ...
Страница 24: ...24 22 Figure 19 All Air From Outdoors Using Horizontal Ducts Into The Boiler Room ...
Страница 34: ...34 Figure 26 Typical Near Boiler Piping When Using A Boiler Feed Pump 32 ...
Страница 35: ...35 Figure 27a Recommended Steam Boiler Piping 1 or 2 Supply Connections Gravity Return 33 ...
Страница 36: ...36 Figure 27b Recommended Steam Boiler Piping 3 Supply Connections Gravity Return 34 ...
Страница 37: ...37 35 Figure 27c Recommended Steam Boiler Piping 4 5 or 6 Supply Connections Gravity Return ...
Страница 42: ...42 40 Figure 30 Typical Water Boiler System Piping ...
Страница 49: ...49 47 Figure 35 Series 32 Standard Boiler Wiring ...
Страница 50: ...50 48 Figure 36 Series 32 CSD 1 Boiler Wiring ...
Страница 65: ...65 63 Figure 42 Exploded View Base Parts ...
Страница 67: ...67 65 Figure 43 Exploded View Gas Manifold Burners Pilot Assembly ...