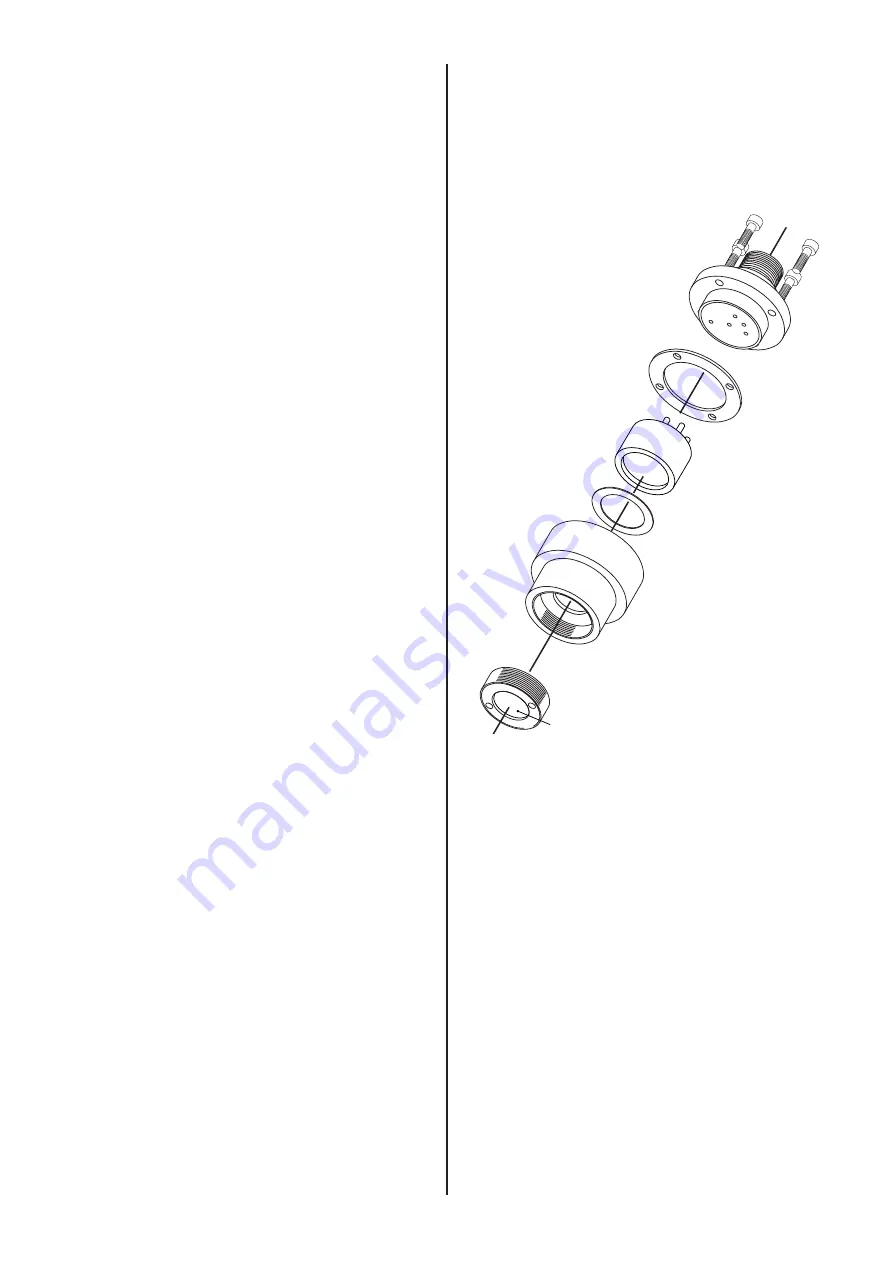
4
(contact Crowcon for the supply of calibration gas.)
j.
Allow the gas reading to stabilise.
k.
Place the end of the ‘CRO-Mag’ over the ’UP’ or ‘DOWN’ arrow pads to
make the display read the correct concentration.
l.
If the control equipment display requires adjustment consult the operating
manual for the equipment.
Returning to normal operation (NORMAL mode):
n.
Place the end of ‘CRO-Mag’ over the ‘MENU’ pad. All decimal points will
disappear and the backlight will turn off. The green status LED will be on
steadily (assuming no gas is present at the detector).
o.
The detector is now operational.
Note: Always return the detector to NORMAL mode to avoid leaving
the detector in a permanently inhibited state.
4.2 Routine Maintenance
The operational life of the sensors depends on the application, frequency and
amount of gas being seen. Under normal conditions (6 monthly calibration
with periodic exposure to CAL gas) the life expectancy of the detectors are:
• Hydrogen sulphide
18 to 24 months
• Carbon monoxide
18 to 24 months
• Ammonia
24 months
• Oxygen
18 to 24 months
• Sulphur dioxide
18 to 24 months
Site practices will dictate the frequency with which detectors are
tested. Crowcon recommend detectors are gas tested at least every 6 months
and re-calibrated as necessary following the steps given in 4.1.
4.3 Sensor Replacement / Servicing of Detectors
WARNING
This work should be carried out by Crowcon or an approved service
centre unless suitable training has been received.
TXgard-Plus uses the 96HD sensor housing which allows the user to replace
the sensors, gaskets and sinter if necessary. An exploded view of the 96HD
sensor housing is given in Diagram 4. The following procedure may be
followed when servicing a TXgard-Plus detector.
a.
Switch off and isolate power to the detector requiring attention.
b.
Open the junction box of the detector by loosening the tamper proof grub
screw and removing the lid by rotating it anti-clockwise.
c.
Remove the amplifier.
d.
Disconnect the 3 sensor wires from the terminal board (terminals 4, 5 & 6).
e.
Unscrew the complete 96HD sensor housing from the junction box.
Note: If a spare 96HD sensor housing complete with new sensor is
available ignore steps f to k and return the old 96HD to Crowcon or an
approved service centre for repair.
f.
Open the 96HD sensor housing by removing the four Allen head screws
from the Top Cap with a 3mm Allen key.
g.
Remove the sensor from the Top Cap PCB.
h.
Fit the replacement sensor checking the part number is correct. This part
number is labelled on the main body of the detector.
i.
Inspect the gaskets and replace if necessary.
j.
The sinter assembly will only need to be replaced if it has become blocked
by dust or oil. Such blockage causes the response time of the detector to
be slow and may affect sensitivity. To remove the sinter a removal tool (Part
# M01614) is required. Loctite No 243 must be used on the sinter
assembly threads to maintain certification.
k.
Re-assemble the 96HD housing taking time to ensure that the 3 mm Allen
head screws are securely fixed into position.
l.
Fit the 96HD sensor housing to the junction box ensuring that the colour
coded wires are terminated correctly.
m.
Replace amplifier ensuring the captive screws are fastened securely.
n.
Switch on power.
0.
Close the junction box remembering to fasten the tamper proof grub
screw into position.
p.
Follow the Commissioning Procedure given in 4.1.
4.4 Changing Alarm Levels (Relay Version Only)
WARNING
This work should be carried out by Crowcon or an approved service
centre unless suitable training has been received. Before attempting
to change alarm levels ensure the detector is in fresh air and no
flammable gas is present.
Alarm levels are factory set as detailed in Table 3. To change either level:
a.
Switch off and isolate power to the detector requiring attention.
b.
Open the junction box of the detector by loosening the tamper proof
grub screw and removing the lid by rotating it anti-clockwise.
c.
Remove the amplifier from the terminal board.
d.
Ensure that the ‘INHIBIT’ link is set to ‘N’.
e.
Re-fit the amplifier to the terminal board ensuring that all screws have
been secured correctly.
f.
Apply power to the detector and allow the detector to stabilise.
g.
Place the end of ‘CRO-Mag’ over the ‘MENU’ pad. The decimal point
above the word ‘ZERO’ will illuminate, the Status LED will flash green and
the display backlight will illuminate.
h.
With clean air present at the detector, place the end of the ‘CRO-Mag’
key over the ‘UP’ or ‘DOWN’ arrow pads to make the display read the
desired alarm level.
4 OFF M4 X 12 mm
ALLEN HEAD SCREWS
TOP CAP AND SENSOR PCB
NEOPRENE GASKET 1
(Part No. M04452)
SENSOR
GASKET 2
(Part No. M04128)
MAIN BODY
SINTER ASSEMBLY
(Part No. S01781)
SINTER
Diagram 4
: 96HD assembly