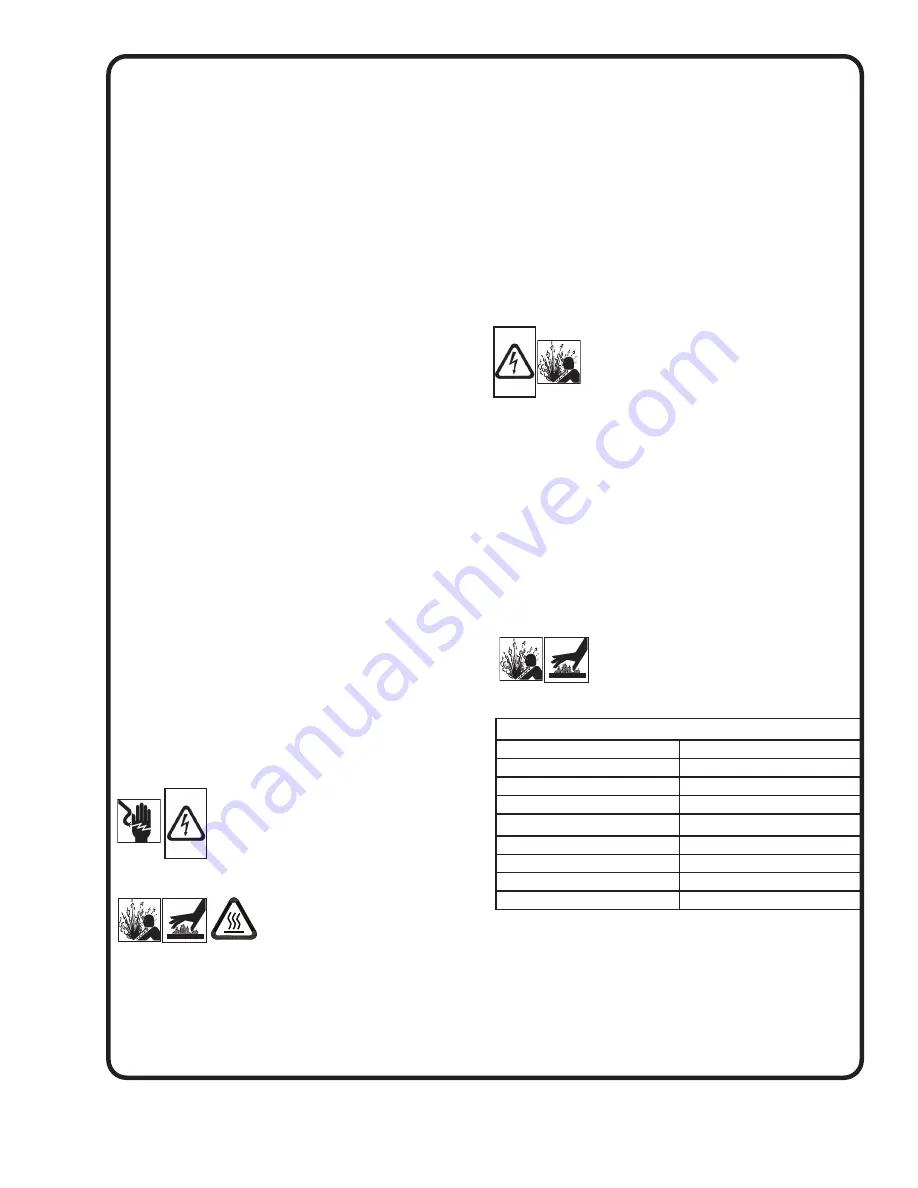
15
C-3.2) Insulation Test:
Before the pump is put into service, an insulation (megger)
test should be performed on the motor. The resistance values
(ohms) as well as the voltage (volts) and current (amps)
should be recorded on the start-up report. Pumps/systems
with an insulation value of less than 5 M-Ohms should
be investigated for moisture or damaged cables before
proceeding.
C-3.3) Pump-Down Test:
After the pump has been properly wired and lowered into the
basin, sump or lift station, it is advisable to check the system
by filling with liquid and allowing the pump to operate through
it’s pumping cycle. The time needed to empty the system, or
pump-down time along with the volume of water, should be
recorded on the start-up report.
SECTION D: PREVENTATIVE MAINTENANCE
As the motor and seal chamber are oil-filled, no lubrication or
other maintenance is required, and generally Barnes Pumps
will give very reliable service and can be expected to operate
for years of normal sewage pumping without failing. However,
as with any mechanical piece of equipment a preventive
maintenance program is recommended and suggested to
include the following checks:
1) Test moisture detector control “Test Switch” for
continuity of circuit. Water in the seal chamber will
energize a seal leak warning light at the control
panel. This is a warning light only and does not
stop the motor. It indicates the seal has leaked
and must be repaired. This should be done within 2
or 3 weeks to prevent further damage. See section
C-2.2.
2) Inspect impeller and body for excessive buildup or
clogging and repair as required per section E-2.
3) Inspect outer shaft seal and replace as required per
section E-3.
4) Check motor for ground leakage and proper amp
draw.
SECTION E: SERVICE AND REPAIR
NOTE: All item numbers in ( ) refer to Figures 9 & 10.
WARNING ! - Electrical power to the pump
motors must be disconnected and locked
out to prevent any dangerous electrical
hazards or personnel danger before any
service work is done to the pump.
CAUTION ! - Operating pump
builds up heat and pressure;
allow time for pump to cool
to room temperature before
handling or servicing.
E-1) Lubrication
E-1.1) Checking Oil
1. Place pump on it’s side, and drain oil into a clean, dry
container.
2. Check oil for contamination using an oil tester with a range
to 30 Kilovolts breakdown.
3. If oil is found to be clean and uncontaminated (measure
above 15 KV. breakdown), refill the seal chamber as per
section E-1.2.
4. If oil is found to be dirty or contaminated (or measures
below 15 KV. breakdown), the pump must be carefully
inspected for leaks at the shaft seal (4), before refilling
with oil. To locate the leak, perform a pressure test as per
section E-1.3. After leak is repaired, refill with new oil as
per section E-1.2.
E-1.2) Replacing Oil:
Seal Chamber - Drain all oil from seal chamber and dispose
of properly. Refill with (see parts list for amount) new cooling
oil as per Table 1. An air space must remain to compensate
for oil expansion (See Fig. 9). Set unit on side and fill.
IMPORTANT! - Do not overfill oil. Overfilling
of seal chamber with oil can create
excessive and dangerous hydraulic
pressure which can destroy the pump
and create a hazard. Overfilling oil voids
warranty.
E-1.3) Pressure Test:
Seal Chamber - Before checking the pump for leaks around
the shaft seal, the oil level should be full. Remove pipe plug.
Apply pipe sealant to pressure gauge assembly and tighten
into pipe plug hole. Pressurize motor housing to 10 P.S.I.
Use a soap solution around the sealed area and inspect
joints for “air bubbles”. If, after five minutes, the pressure
is still holding constant, and no “bubbles” are observed,
slowly bleed the pressure and remove the gauge assembly.
Replace the pipe plug using a sealant. If the pressure does
not hold, then the leak must be located.
CAUTION! - Pressure builds up extremely
fast, increase pressure by “tapping” air
nozzle. Too much pressure will damage
seal. Do Not exceed 10 P.S.I. in seal
chamber.
TABLE 1 - COOLING OIL - Dielectric
SUPPLIER
GRADE
BP
Enerpar SE100
Conoco
Pale Paraffin 22
Mobil
D.T.E. Oil Light
G & G Oil
Circulating 22
Imperial Oil
Voltesso-35
Shell Canada
Transformer-10
Texaco
Diala-Oil-AX
Woco
Premium 100
Содержание BARNES BLADE XGV
Страница 19: ...19 FIGURE 9 Cross Sections FIGURE 10 Vertical Discharge Horizontal Discharge ...
Страница 24: ...Notes ...