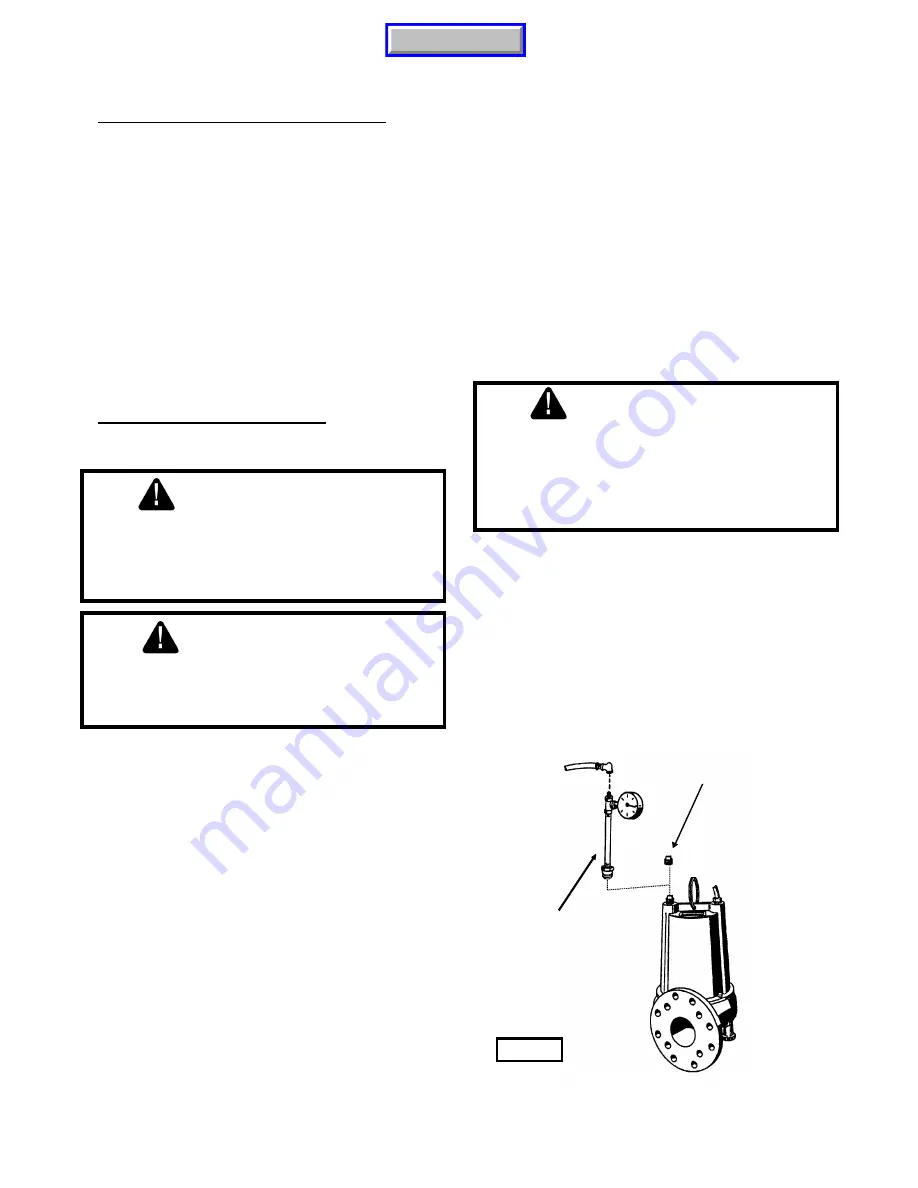
SECTION E: PREVENTATIVE MAINTENANCE
As the motor is oil filled, no lubrication or other maintenance is
required, and generally Barnes Pumps will give very reliable
service and can be expected to operate for years on normal
sewage pumping without failing. However as with any
mechanical piece of equipment a preventive maintenance
program is recommended and suggested to include the
following checks:
1) Inspect motor chamber for oil level and contamination
and repair as required per section F-1.
2) Inspect impeller and body for excessive build-up or
clogging and repair as required per section F-2.
3) Inspect motor, bearings and shaft seal for wear or
leakage, replace as required per section F-3.
SECTION F: SERVICE AND REPAIR
NOTE:
All item numbers in ( ) refer to Figures 8 & 9.
WARNING !
ELECTRICAL POWER TO THE PUMP MOTORS MUST
BE DISCONNECTED AND LOCKED OUT TO PREVENT
ANY DANGEROUS ELECTRICAL HAZARDS OR
PERSONNEL DANGER BEFORE ANY SERVICE WORK
IS DONE TO THE PUMP.
CAUTION !
OPERATING PUMP BUILDS UP HEAT AND
PRESSURE; ALLOW TIME FOR PUMP TO COOL TO
ROOM TEMPERATURE BEFORE HANDLING OR
SERVICING.
F-1) Lubrication:
Anytime the pump is removed from operation the cooling oil in
the motor housing (3), must be checked visually for oil level
and contamination.
F-1.1) Checking Oil:
Motor Housing-
To check oil, set unit upright. Remove Pipe
Plug (2) or (36) from motor housing (3) With a flashlight,
visually inspect the oil in the motor housing (3) to make sure it
is clean, clear and that oil level is above all internal
componentry.
F-1.2) Testing Oil:
1.
Place pump on it’s side, remove Pipe Plug (2) or (36) from
motor housing (3) and drain oil into a clean, dry container.
2.
Check oil for contamination using an oil tester with a range
to 30 Kilovolts breakdown.
3.
If oil is found to be clean and uncontaminated (measure
above 15 KV. breakdown), refill the motor housing as
per section F-1.3.
4.
If oil is found to be dirty or contaminated (or measures
below 15 KV. breakdown), the the pump must be carefully
inspected for leaks at the shaft seal (9), Gland nut (28b)
and (39b if equipped), O-ring (24), Gasket (13), pipe plugs
(2) or (36) before refilling with oil. To locate the leak,
perform a pressure test as per section F-1.4. After leak is
repaired, refill with new oil as per section F-1.3.
F-1.3) Replacing Oil:
Motor Housing-
Drain all oil from motor housing and dispose
of properly. Refill with (see parts list for amount) new cooling
oil as per Table 1. An air space must remain in the top of the
motor housing to compensate for oil expansion (see Fig. 8).
Set unit upright and fill only until the motor, as viewed through
the pipe plug opening, is just covered and no more. Apply pipe
sealant to pipe plug (2) or (36) and install in motor housing (3).
WARNING !
DO NOT OVERFILL OIL
OVERFILLING OF MOTOR HOUSING WITH OIL CAN
CREATE EXCESSIVE AND DANGEROUS HYDRAULIC
PRESSURE WHICH CAN DESTROY THE PUMP AND
CREATE A HAZARD. OVERFILLING OIL VOIDS
WARRANTY.
F-1.4) Pressure Test:
Motor Housing-
Before checking the pump for leaks around
the shaft seal, square rings, and cord inlet, the oil level should
be full as described in section F-1.3. Remove pipe plug (2) or
(36) from motor housing (3). Apply pipe sealant to pressure
gauge assembly and tighten into pipe plug hole (see Fig. 2).
Pressurize motor housing to 10 P.S.I. Use a soap solution
around the sealed areas and inspect joints for "air bubbles". If,
after five minutes, the pressure is still holding constant, and no
"bubbles" are observed, slowly bleed the pressure and remove
the gauge assembly. Replace the pipe plug using a sealant. If
the pressure does not hold, then the leak must be located.
10 PSI AIR
⇒
Remove Pipe Plug
PRESSURE GAUGE
ASSEMBLY
(See Parts List)
Fig. 2
8
Manual Index
Содержание BARNES 4SE Series
Страница 15: ...Fig 8 15 Manual Index ...
Страница 16: ...Fig 9 16 Manual Index ...