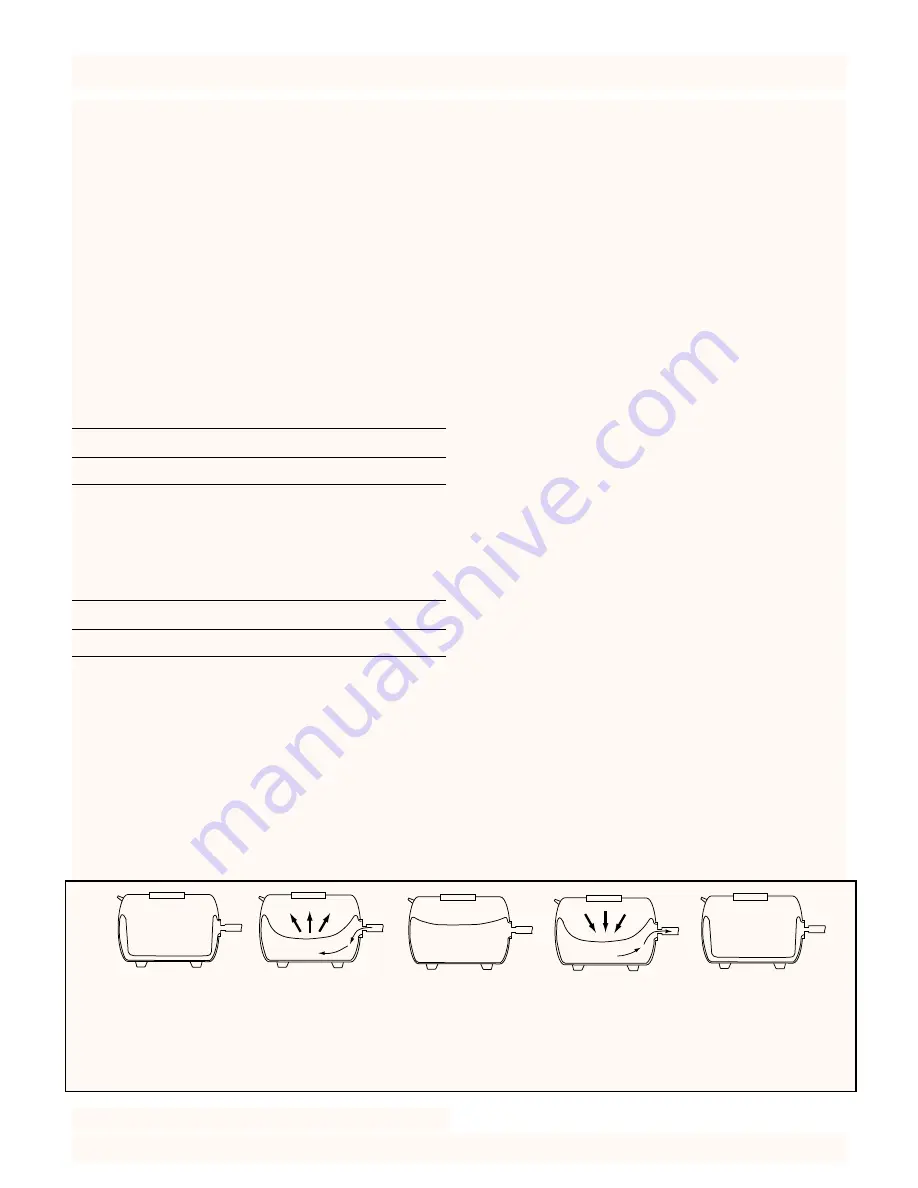
INSTALLATION
5
1. Wrap male pipe threads being attached to pump
with one or two layers of Teflon tape. Cover entire
threaded portion of pipe.
2. Do not overtighten threaded fittings in the plastic
pump. Be sure you do not try to tighten joint past
thread stop in pump port!
3. If leaks occur, remove fittings, clean off old tape,
rewrap with two to three layers of tape and remake
the connection. If joint still leaks, replace the fit-
tings (fittings may be undersized).
4. Be sure to support all piping connected to the
System.
Horizontal Piping from Well to Pump
When the pump is offset more than 25 feet from the
well, horizontal suction pipe size should be increased
to reduce friction losses. Never install a suction pipe
that is smaller than the suction tapping of the pump.
1-1/4”
1-1/2”
2”
Up to 25 Ft.
25 to 50 Ft.
50 to 200 Ft.
Discharge Pipe Sizes
When the pump is some distance from the house or
point of water use, the discharge pipe size should be
increased to reduce pressure losses caused by friction.
1”
1-1/4”
1-1/2”
Up to 25 Ft.
25 to 100 Ft.
100 to 600 Ft.
Tank
Tanks are pre-charged with 30 PSI air pressure at the
factory. Your tank requires an air charge of 30 pounds
per square inch (PSI) for proper operation; check tank
pressure with tire gauge to determine if air charge
needs adjustment. Tank pre-charge should be checked
annually; see instructions at right.
In areas where the temperature is high for long peri-
ods of time, the tank pre-charge pressure may increase.
This may reduce the tank drawdown (amount of water
available per cycle). If this occurs, reduce the pre-
charge pressure to two PSI below the pump cut-in set-
ting of the pressure switch (normally to 28 PSI).
It is necessary to flush all air out of the piping system
and water reservoir portion of the pre-charged tank.
This is required on new installations, pumps requiring
repriming and pumps that have been disassembled for
service. Do this as follows:
1. Open faucets furthest from tank and allow pump to
operate.
2. Air in the system will cause a sputtering flow; allow
faucets to run until you have a steady, air free
stream.
3. Open and close faucets repeatedly until you are
sure all air has been removed.
4. If stream does not become steady, air may be leak-
ing into the system; check for leaks in the piping on
the suction side of the pump.
NOTICE:
To prevent waterlogging, check tank air
charge annually.
To Check Tank Air Charge
If drawdown (amount of water available per cycle) de-
creases significantly, check as follows:
1. To check air charge in tank, shut off electric power
to pump, open faucet near tank, and drain com-
pletely.
2. At the air valve in top of tank, check air pressure
with standard tire gauge. Air pressure should be
same as pump pressure switch cut-in setting (30
PSI).
3. If the air pressure is below the cut-in setting, add air
to the tank. Use an air compressor or a portable air
storage tank.
4. Use soap or liquid detergent to check for air leaks
around air valve. Continuous bubbling indicates a
leak. If necessary, install new core in air valve. This
is the same as those used for automobile tubeless
tires.
H
2
0
H
2
0
H
2
0
612 1293
1
2
3
4
5
1. Tank nearly empty – air expands filling area above
vinyl separator.
2. Water begins to enter tank – air is compressed
above separator as it fills with water.
3. Pump-up cycle completed – air now compressed
to cut off setting of pressure switch.
4. Water being drawn from tank – compressed tank
air forces water out of separator.
5. Separator completely empty – new cycle ready to
begin.
Figure 3
Water
Water
Water
Содержание 390.252156
Страница 15: ...15 ...