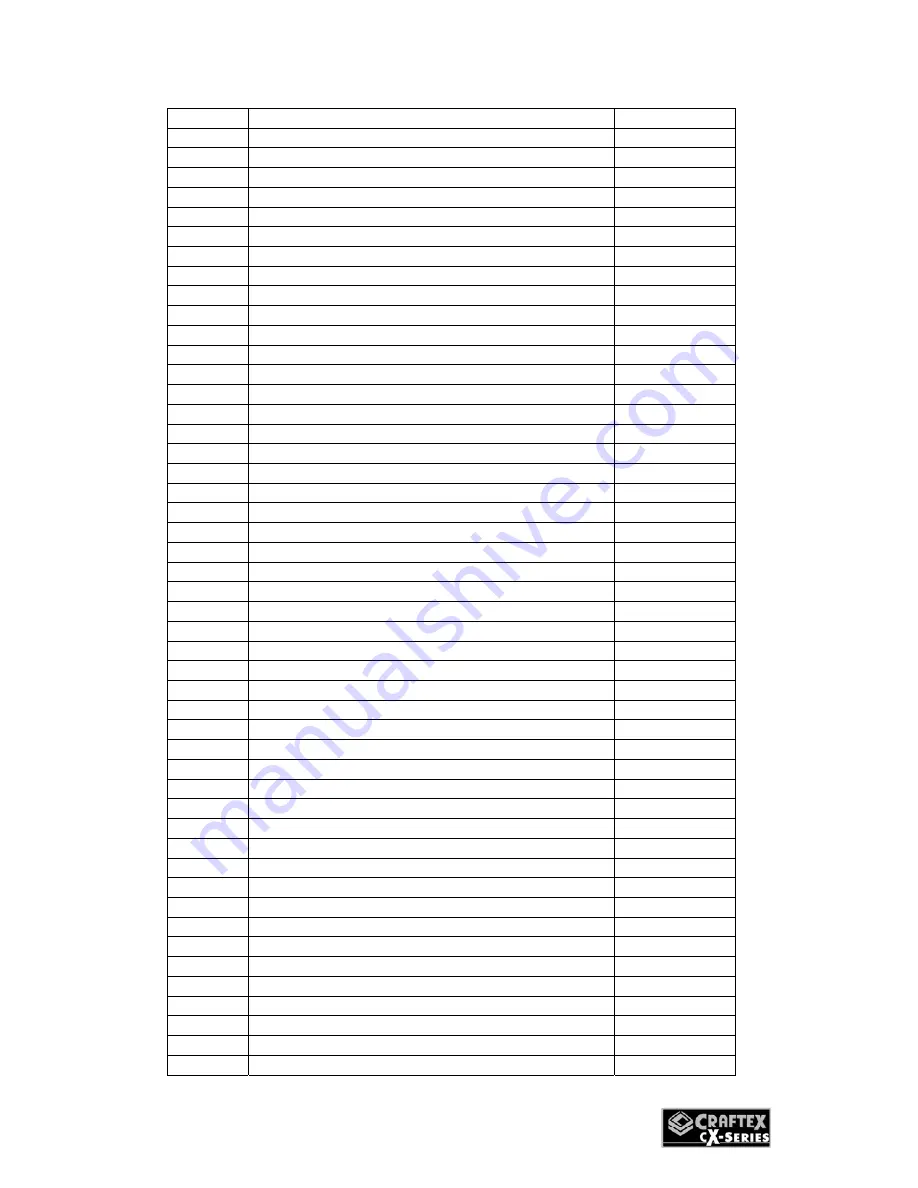
18
46
BELT TENSION LOCK KNOB
P0624046
47
PIN - ROLL 3 X 12
PRP61M
48 SHAFT
P0624048
49 SPACER
M18
P0624049
50 COMPRESSION
SPRING
P0624050
51
LOWER PULLEY ACCESS PLATE
P0624051
52
NUT - HEX 3/8-16
PN08
53 RUBBER
FOOT
P0624053
54
SCREW - PAN HD PHILLIPS M5-0.8 X 10
PS09M
55
WASHER - FLAT M5
PW02M
56
STRAIN RELIEF
P0624056
57
SWITCH - ASSEMBLY
P0624057
57-1
SCREW - PAN HD PHILLIPS 10-24 X 1 1/2
PS10
57-2
WASHER - TOOTHED EXT M5
PTLW02M
57-3 SWITCH
PLATE
P0624057-3
57-4 SWITCH
BOX
P0624057-4
57-5
NUT - HEX 10-24
PN07
57-6
SWITCH W/ SAFETY KEY
P0624057-6
58
SCREW - SET M4-0.7 X 6
PSS79M
59 MOTOR
PULLEY
P0624059
60
NUT - LOCK M8-1.25
PLN04M
61
SCREW - PAN HD PHILLIPS M6-1.0 X 16
PS11M
62 MOTOR
PLATE
P0624062
63
WASHER - FLAT M5
PW02M
63-1
WASHER - LOCK M5
PLW01M
64
SCREW - CAP SOC HD M5-0.8 X 15
PSB10M
65 TENSION
BRACKET
P0624065
66
BOLT - SQUARE HD
P0624066
67 RUBBER
SLEEVE
P0624067
OT MOTOR
P0624068
68-1 CAPACITOR
COVER
P0624068-1
68-2
CAPACITOR 25MFD 250VAC
P0624068-2
68-3 FAN
P0624068-3
68-4 FAN
COVER
P0624068-4
69 DUST
GUARD
P0624069
70
LOCTITE SCREW 10-24 X 6
P0624070
71
C-RING EXT M10
PR01M
72
TOOL POST BASE
P0624072
73
TOOL REST LOCK HANDLE M6-1.0
P0624073
74 ADJUST
SHAFT
P0624074
75 SLIDE
COLLAR
P0624075
76
NUT - LOCK M10-1.5
PLN05M
77 TOOL
REST
P0624077
78
PIN - ROLL M4 X 20
PRP39M
79
C-RING EXT M14
PR02M
80 ECCENTRIC
SHAFT
P0624080
81 LEVER
KNOB
P0624081
82
TOOL REST RELEASE LEVER
P0624082
83
WRENCH - HEX M2.5
PAW02.5M
Содержание CX801
Страница 1: ...CX801 HEAVY DUTY BENCH TOP LATHE User Manual ...
Страница 6: ...6 PHYSICAL FEATURES ...
Страница 16: ...16 CX801 PARTS BREAKDOWN ...