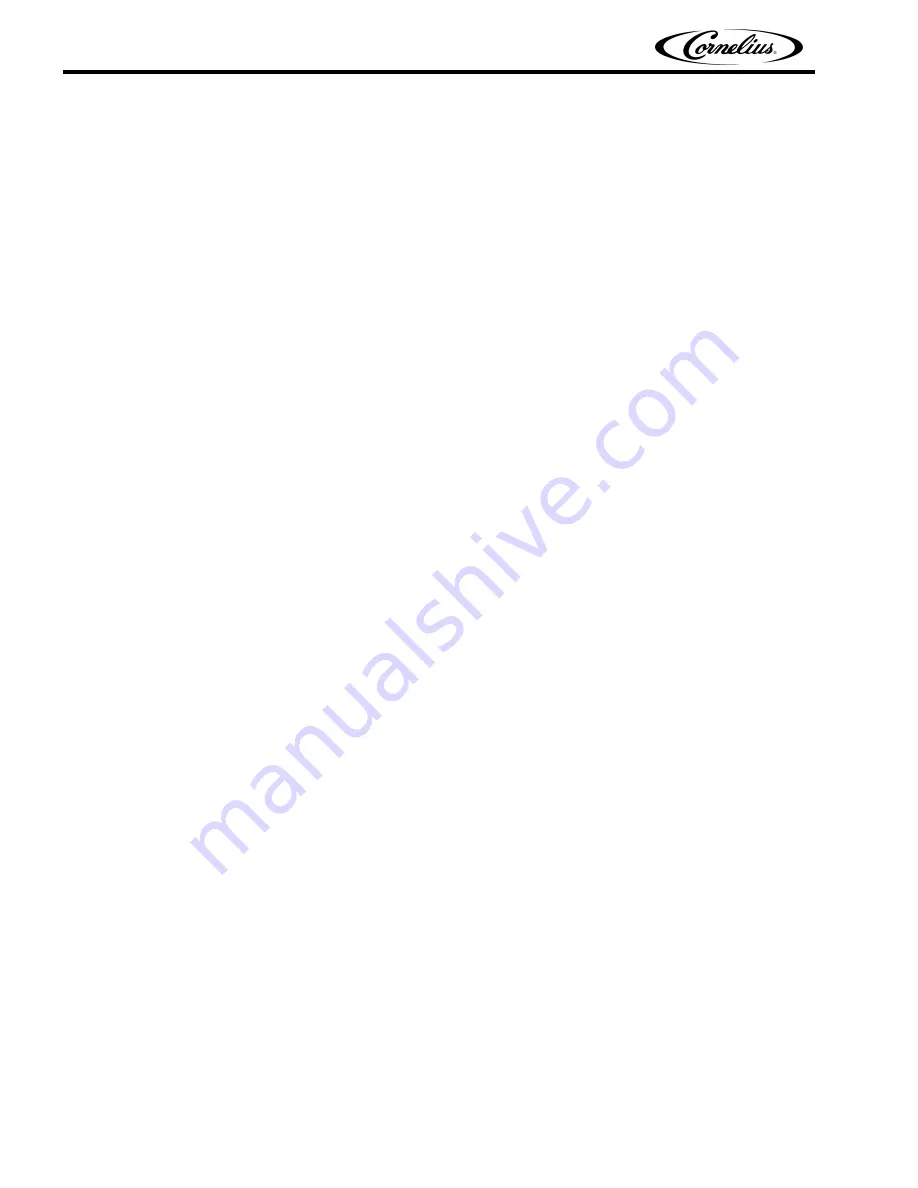
Installation and Service Manual
Publication Number: 710160089
- 10 -
© 2004, IMI Cornelius Inc.
LIQUID LEVEL CONTROL WITH TIMER
P
URPOSE
OF
L.L.C.
WITH
T
IMER
The liquid level control with timer is designed to protect the pump of a carbonation system against
running dry and consequent pump damage.
O
PERATION
Designed to operate as a normal liquid level control under normal conditions. The timer circuit monitors
the running time of the pump motor. If the pump motor runs continuously for the specified time period,
the timer circuit will discontinue the operation of the pump motor until the reset switch is manually reset.
NOTE: The built-in carbonator normal refill time for the UCC-40 is 3 to 5 seconds (15 fl oz. [444
ml] normal refill volume).
Usually, when the water flow to the pump is interrupted for any extended period, the residual water
present in the pump warms up and will eventually evaporate, but as it warms up it continues to lubricate
the wear points of the pump. Experience has shown that a seven minute interruption in water flow is not
significantly detrimental to the future operation of the pump.
WARNING: The L.L.C. with timer will give no protection against the initial startup of a new
carbonator pump with no water being present at the pump. A new pump which has never
pumped water is considered dry and will suffer damage in a matter of 2 to 3 minutes.
F
EATURES
220v/50z and 115v/60z models are available.
3-minute and 7-minute models are available.
Designed to control and protect a 1/2hp maximum pump motor.
Reset
A. Challenger and Enterprise carbonator.
• Separate manual reset switch (#35-0181) ensures that the cause of the problem has been
corrected before continued use of the pump motor. This feature has been provided in these
carbonators since January 1, 1995.
• Carbonators built before January 1, 1995 can be fitted with the time style liquid level control and
can be manually reset be disconnecting the power supply cord from the electrical supply and then
reconnecting same.
B. Overcounter Dispensers with built-in Carbonators (models CTC-20, CTC-40)
• These models have a rocker switch which controls the power supply to the liquid level control
(carbonation system). This switch is accessible through the top surface of the top cover of the
CTC-40, and located on the top left corner of the front valve mounting plate of the model CTC-20.
The timer can be reset by turning this rocker switch “off” and then “on” again.