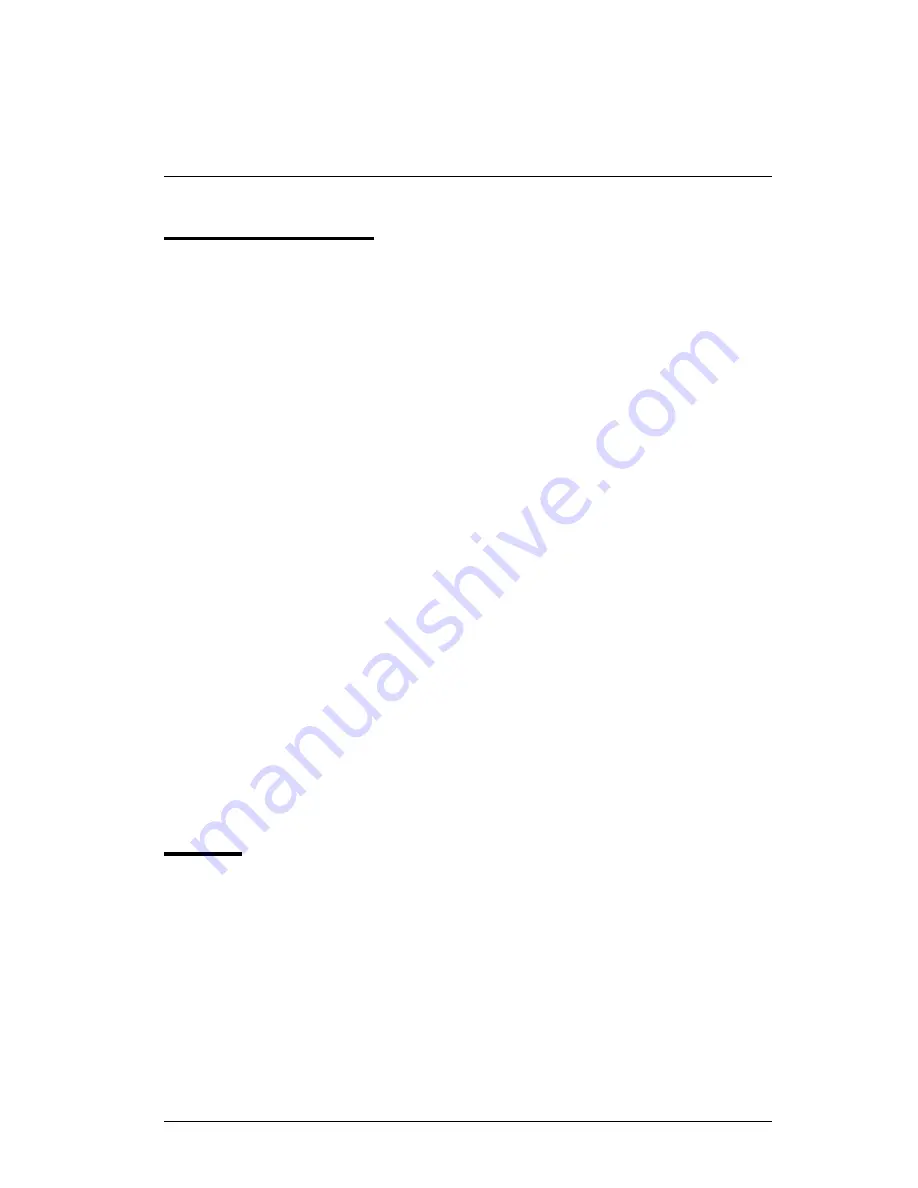
REFRIGERATION INSTALLATIONS LIMITED
Unit D9 Newton Business Park
Cartwright Street
H y d e
Cheshire SK14 4EH
Telephone: +44 (0)161 366 1110 Fax: +44 (0)161 366 1190
D ocument Reference: WI 9 Page 24 of 24
Issue 02
11. Unit Re-assembly
Re-assembly of the unit is essentially the reverse of the
dismantling procedure but the following points are important.
11.1 Thoroughly clean between the cooling fins of the condenser
coil with compressed air, vacuum or a brush. This is particularly
important for older machines where dust and other airborne
contaminants may have lodged in the fins thereby reducing the
cooling efficiency.
11.2 Replace all cable ties, grommets and screws.
11.3 Ensure that any glue used has set, that glued components
are secure before continuing to assemble and that glue has not
unintentionally contaminated or glued other components.
11.4 When replacing the top panel ensure that no wires or cables
are trapped and could be damaged.
11.5 Ensure that the clear sealing ring that sits on the top edge of
the Refrigeration Barrel is correctly orientated. See Section 8.8.
12. Test
It is recommended that the repaired unit is subjected to a
functional check as described in Sections 8.3 through 8.5 as
appropriate.