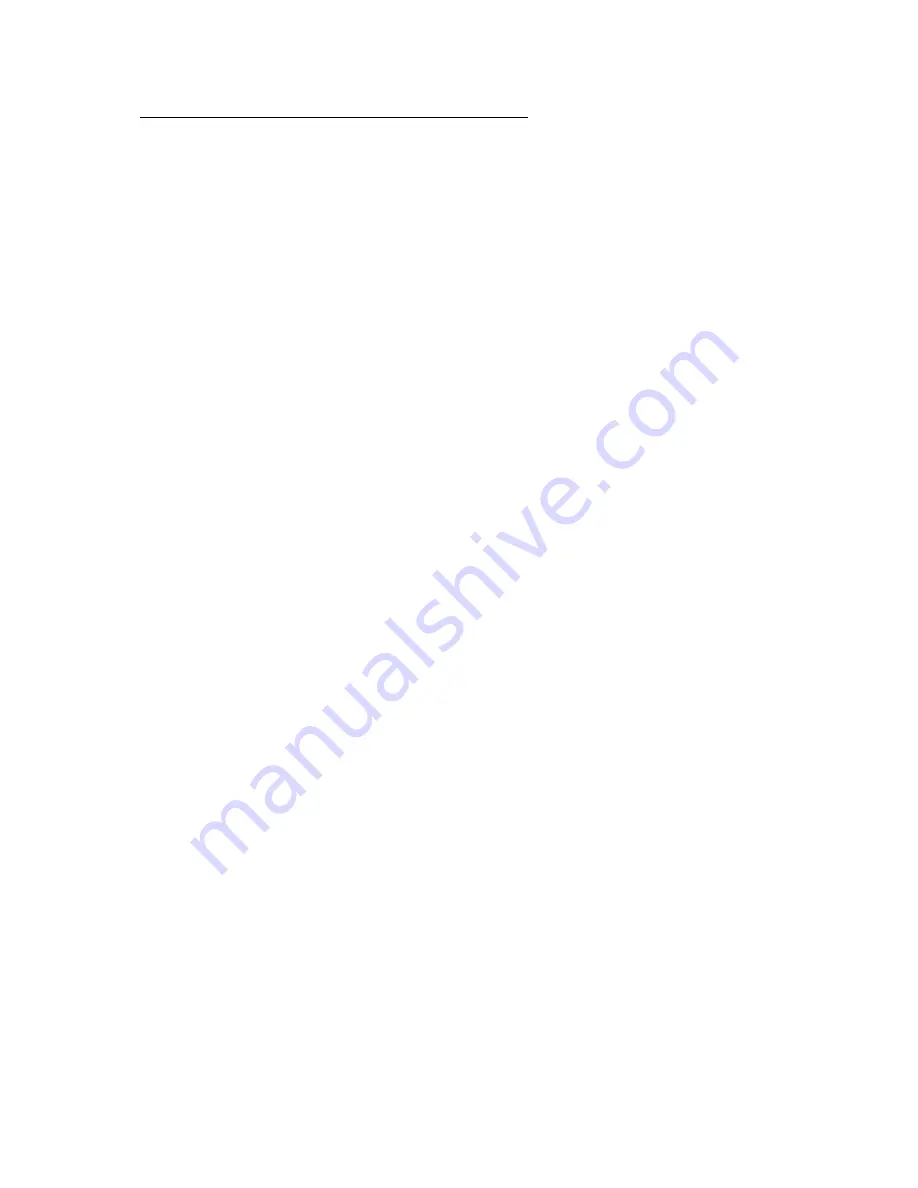
13
326142000
IMPORTANT: The following CO
2
and liquid disconnects disconnecting and connecting procedure for
soft drink tank replacement or filling soft drink tank in place must be performed in order as follows:
To disconnect soft drink tank from Unit syrup system.
A.
Disconnect liquid disconnect from soft drink tank. NOTE - Disconnecting liquid quick
disconnect from soft drink tank first prevents syrup from backflowing through Unit syrup flow
regulator which may alter regulator adjustment.
B.
Second, disconnect CO
2
quick disconnect from soft drink tank.
NOTE: Unit control panel is equipped with a hidden ‘‘SECURITY SWITCH’’ located between ‘‘FILL 1’’
and ‘‘ERROR RESET’’ control switches (see Figure 5). Pressing in and holding ‘‘SECURITY SWITCH’’
for 3-seconds deactivates control switches preventing tampering with Unit normal operation. To
reactivate control switches, press in and hold ‘‘SECURITY SWITCH’’ for 3-seconds.
2. Pressurize soft drink tanks containing syrup, then connect tanks to Unit syrup systems. ‘‘OFF 1’’, ‘‘OFF 2’’,
‘‘SYRUP 1’’, and ‘‘SYRUP 2’’ fault messages will continue to be displayed.
ADJUSTING BRIX (WATER-TO-SYRUP) ‘‘RATIO’’ OF DISPENSED PRODUCT
The following steps 1 through 9 are instructions for adjusting Brix (Water-to-Syrup ‘‘Ratio’’ (mixture) of
dispensed product on one system.
1. Press ‘‘FILL 1’’ switch to fill No. 1 syrup system sold-out float. ‘‘SYRUP 1’’ fault message will go out and
‘‘FILL 1’’ fault message will come on. ‘‘OFF 1’’, ‘‘OFF 2’’, and ‘‘SYRUP 2’’ fault messages will continue to be
displayed.
2. Press ‘‘AUTO BLEND 1’’ switch to fill No. 1 system product blender tank with product. ‘‘FILL 1’’ fault
message will go out when ‘‘AUTO BLEND 1’’ switch is pressed. When product blender tank is full, press
‘‘FILL 1’’ switch to prevent more product from entering tank. ‘‘OFF 1’’, ‘‘OFF 2’’, and ‘‘SYRUP 2’’ fault
messages will continue to be displayed.
3. Open No. 1 product blender tank product sample valve (see Figures 2 and 6) and take sample
(approximately 6-ounces) of product in cup or glass.
NOTE: Temperature compensated hand-type refractometers (P/N 511004000) are available from The
Cornelius Company.
4. Check product BRIX with a temperature compensated hand-type refractometer. BRIX should read 13.5
±
0.5. If BRIX is not within tolerance, adjust white syrup flow regulator for No. 1 syrup system as follows:
A.
Loosen jamb nut on syrup flow regulator.
B.
Turn regulator adjusting screw to the left (counterclockwise) no more than 1/8-turn at a time to reduce
syrup flow rate or turn screw to the right (clockwise) no more than 1/8-turn to increase flow rate.
C.
Tighten jamb nut on syrup flow regulator, then lightly tap regulator to register adjustment.
5. Place container under No. 1 product sample valve. Open valve to purge product out of product blender
tank, line, and valve, then close valve. ‘‘OFF 1’’, ‘‘OFF 2’’, and ‘‘SYRUP 2’’ will continue to be displayed.
6. Press ‘‘AUTO BLEND 1’’ switch to run new batch of product into product blender tank. When product
blender tank is full, press ‘‘FILL 1’’ switch to prevent more product from entering product blender tank.
‘‘OFF 1’’, ‘‘OFF 2’’, and ‘‘SYRUP 2’’ fault messages will continue to be displayed.
7. Repeat steps 3 and 4 preceding to check product sample for BRIX.
8. Repeat steps 5 through 7 preceding until proper BRIX adjustment is achieved.
9. Repeat steps 1 through 8 preceding to adjust BRIX of dispensed product on No. 2 system. After
completing BRIX on No. 2 system, ‘‘OFF 1’’ and ‘‘OFF 2’’ fault messages should continue to be displayed.
Содержание 326142000
Страница 23: ...16 326142000 THIS PAGE LEFT BLANK INTENTIONALLY ...
Страница 33: ...26 326142000 THIS PAGE LEFT BLANK INTENTIONALLY ...
Страница 37: ...30 326142000 FIGURE 5 OPERATING CONTROLS ...
Страница 38: ...31 326142000 FIGURE 6 UNIT INTERNAL COMPONENTS ...
Страница 59: ...52 326142000 FIGURE 12 WATER STRAINER SCREEN AND DOUBLE LIQUID CHECK VALVE ...
Страница 66: ...59 326142000 FIGURE 16 REFRIGERATION FLOW DIAGRAM ...
Страница 67: ...60 326142000 FIGURE 17 WIRING DIRGRAM ...
Страница 77: ...326142000 70 4 5 6 7 8 11 12 14 15 79 84 85 87 88 115 117 118 4 FIGURE 20 FCB FLOW DIAGRAM ...
Страница 86: ...79 326142000 THIS PAGE LEFT BLANK INTENTIONALLY ...