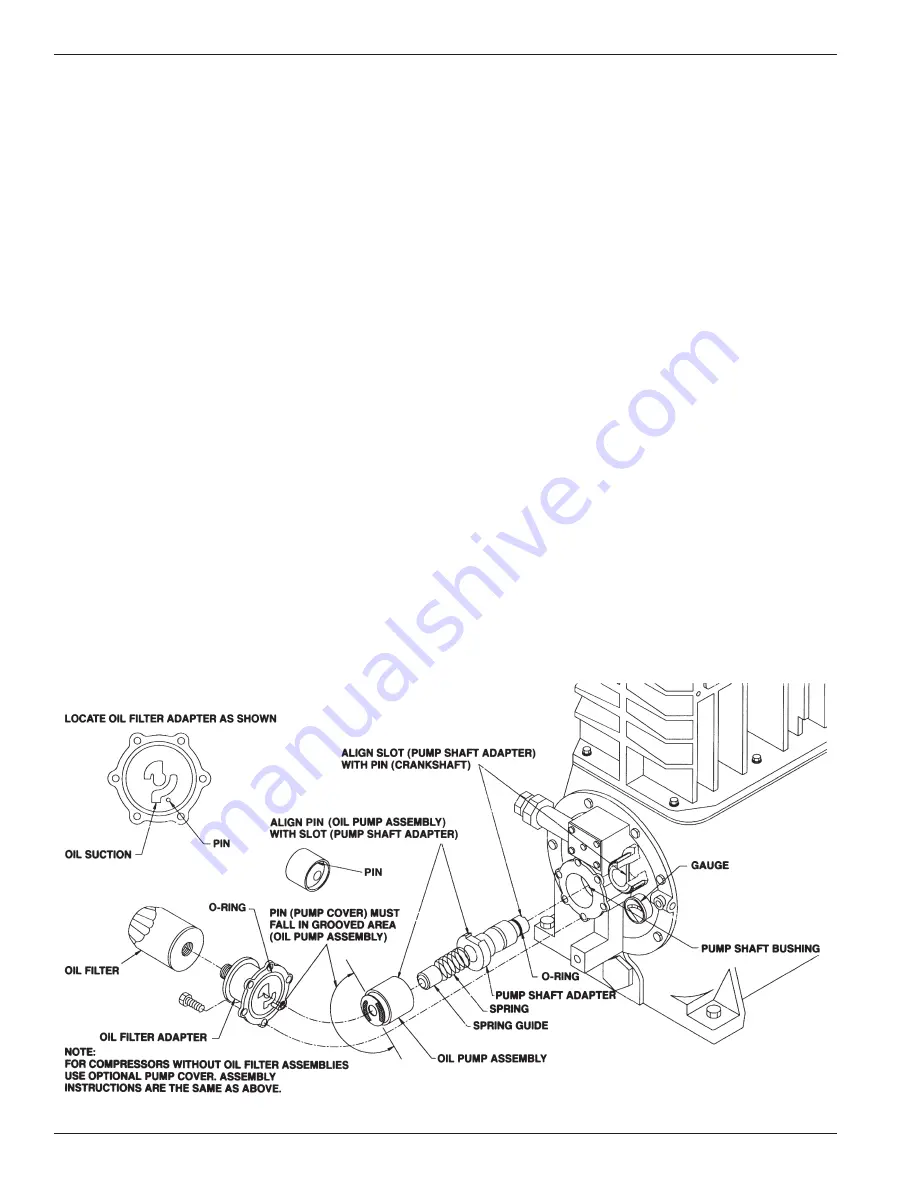
Figure 4.8: Oil pump inspection
4.7.3 Replacing Crankcase Roller Bearings
To inspect the roller bearings, remove the flywheel from
the crankshaft and then remove the bearing carrier and
crankshaft from the crankcase. If corrosion or pitting is
present, the roller bearings should be replaced. When
replacing roller bearings, always replace the entire
bearing and not just the cup or the cone.
1. To replace the bearings, press the cups out of the
crankcase and bearing carrier and press the cones off
the crankshaft.
2. Press the new bearings into position and reassemble
the crankshaft and bearing carrier to the crankcase.
When reinstalling the bearing carrier, make sure the oil
pump shaft slot is aligned with the pin in the crankshaft.
Make sure to install the bearing carrier gasket so the oil
passage hole is not blocked (see figure 4.7).
3. In order to check the crankshaft endplay, the oil pump
must first be removed (see section 4.8).
4. Press the end of crankshaft towards the crankcase; if a
clicking noise or motion is detected, the crankshaft has
too much endplay. See Appendix B.
5. To reduce endplay, remove the bearing cover and
remove a thin shim. Recheck the endplay after replacing
the bearing cover.
6. When there is no detectable endplay, the shaft must
still be able to rotate freely. If the crankshaft sticks
or becomes abnormally warm, then the crankshaft
bearings are too tight. If the crankshaft is too tight,
add more shims, but make sure not to over shim.
(Appendix B lists the proper crankshaft endplay). When
the crankshaft can be rotated freely by hand with
proper endplay, the rest of the compressor may be
reassembled. If the crankshaft roller bearings are too
tight or too loose, premature bearing failure will result.
7. Reinstall the oil pump and flywheel and check the run
out as shown in Appendix B.
4.8 Oil Pump Inspection
If the compressor operates for a prolonged period
with dirty or contaminated crankcase oil, damage to
the oil pump and bearings may result.
1. To check the oil pump, unbolt the pump cover and
remove the oil pump, spring guide, spring and oil
pump shaft adapter as shown in figure 4.8.
2. Inspect the gears in the oil pump for corrosion or
pitting and replace if necessary.
3. Check the oil pump shaft bushing in the bearing
carrier. If the bushing is corroded, pitted or worn,
the oil pump shaft bushing should be replaced.
Inspect and replace other parts as necessary.
4. Before reassembling the oil pump mechanism,
replace the O-rings in the oil pump cover and on
the oil pump adapter shaft (see figure 4.8).
5. Rotate the drive pin in the crankshaft to a vertical
position for easiest reassembly.
18
Содержание D791
Страница 27: ...Appendix C Outline Dimensions Model D891 Single Stage with 107B Mounting Inches Centimeters 27 ...
Страница 33: ...33 ...
Страница 51: ...51 ...