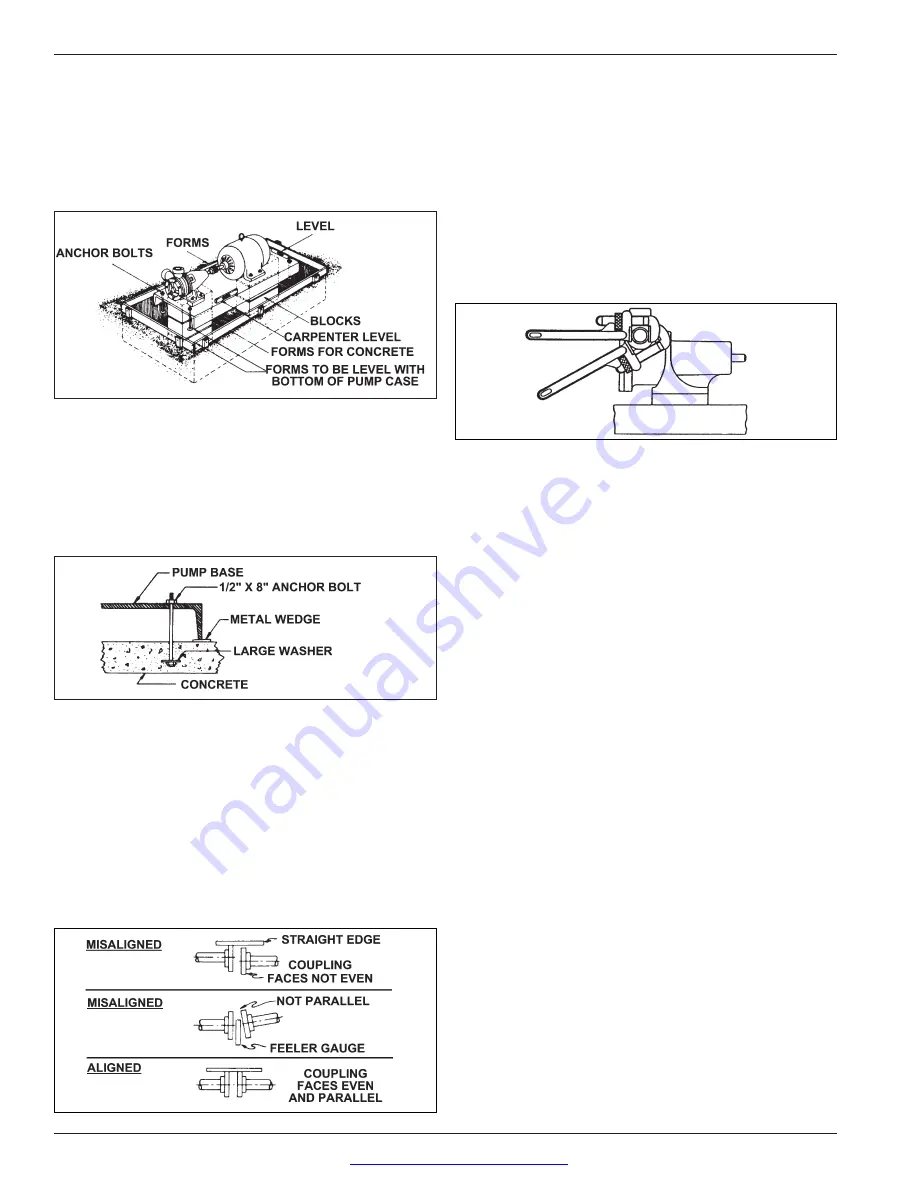
1.5 Pump Foundation—F-Models
Every pump deserves a firm, neat concrete foundation (see
figure 1.5). There are many ways to construct a foundation,
and the example in figure 1.5 is only a suggestion. The
important features are to make the foundation level, and
deep enough to get below the frost line for your locality.
See Appendix D for outline dimensions.
Figure 1.5
1.6 Level Base
After the concrete has set, check the pump base for level.
Drive metal shims under the base near the anchor bolts
as below. Tighten anchor bolts and recheck the base for
level. See figure 1.6.
Figure 1.6
1.7 Coupling Alignment—F-Models
The coupling alignment must be near perfect to give quiet,
long life service to the pump and driver.
The pump and
driver shafts are carefully aligned at the factory but
should always be checked after the pump is installed
and before the initial operation.
Lay a straight edge across coupling halves, top, and side;
both positions must line up to be correct (figure 1.7).
Figure 1.7
If misalignment exists, adjust the shims between the pump
base and the foundation until exact alignment is accomplished.
1.8 Back-up Wrench
To keep from breaking the pump nozzle or springing the
pump out of alignment, always use a back-up wrench as
shown in figure 1.8.
Use the proper wrench size, and be sure the pipe threads
are clean and evenly doped with the proper thread seal
for the service. Avoid using excessive pipe dope because
it may enter the pump and damage the mechanical seal.
Figure 1.8
1.9 Driver Installation
The wiring of your electric motor is extremely important and
must be done by a competent electrical contractor. The
wire size charts on pages 7 and 8 indicate the minimum
standards for wire sizes.
Improper motor wiring will cause you to experience
expensive motor difficulties from low voltage. If you
suspect you have low voltage, call your power company.
Connecting your motor for the voltage you have available
is important too. Be sure your motor is connected to
the proper voltage. Connecting to improper voltage will
completely destroy your motor.
With explosion-proof motor applications in humid climates,
the normal breathing and alternating temperatures of the
motor (warm during operation and cold when stopped) will
often cause moist air to be drawn into the motor housing.
This moist air will condense and may eventually add enough
free water to the inside of the motor to cause it to fail. To
prevent this, make a practice of running the motor and pump
at least once a week on a bright, dry day for an hour or so
(pump through the bypass system). During this time, the
motor will heat up and vaporize the condensed moisture. No
motor manufacturer will guarantee their explosion-proof or
totally enclosed motor against damage from moisture.
Engine drivers pose a special consideration. The
manufacturer's instructions must be followed. When the
Coro-Flo
®
Pump is equipped with an engine from the
factory, the engine speed should normally not exceed 3600
rpm. Excessive engine speed will overload the engine and
cause early failure. The engine loses 3% of its power for
every 1000 feet above sea level, so if your installation is at
a higher altitude than normal, consult the factory.
6
www.northridgepumps.com