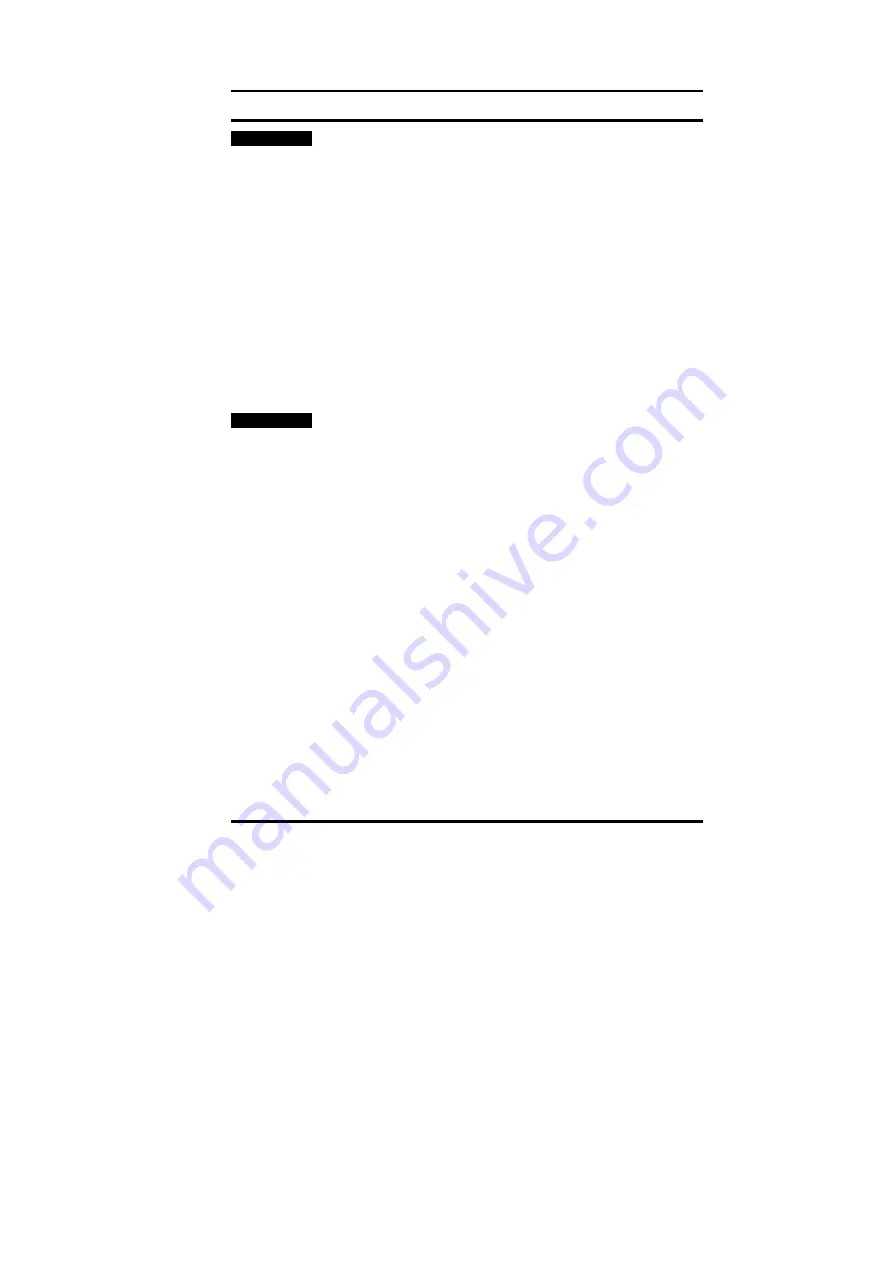
Issue Number: 3
17
5 Cyclic
Data
NOTE
“OUT data” and “IN data” describe the direction of data transfer as
seen by the PLC scanner.
5.1
What is Cyclic Data?
Cyclic data is a method data transfer that must be set-up during
network configuration, but is transmitted automatically once
configuration is complete. The high-speed data transfer is achieved by
transmitting only a 16-bit data value for each cyclic channel over the
Profibus-DP network, and relying on local mapping information within
the Unidrive to ensure the correct data is sent to the correct locations.
This method relies on the PLC program writing and reading data values
to and from the registers allocated to the node during network
configuration, and the source and destination of IN and OUT data being
set-up correctly in the Unidrive itself.
The flexibility of the Unidrive Profibus-DP interface means that each
cyclic data OUT channel can be directed to any read-write Unidrive
parameter. Similarly, each cyclic data IN channel can use any Unidrive
parameter as a source of data.
NOTE
The mapping configuration cannot be changed dynamically, as the
UD70 must be reset before changes to the mapping become active.
5.2
What is Data Consistency
If a data format is selected that requires full data consistency, this
guarantees that the data on the Profibus is not updated with the new
data values until ALL data words have been written into the Profibus
buffer memory.
Consistent data may be important when using the 4-word non-cyclic
data format. Without consistency, it is possible for 2 of the 4 words to
go on one network cycle, with the data value updated on the next cycle.
If the command was a write command, this could result in the previous
data value being written to the new parameter, and could have
disastrous consequences.
Using data consistency can often put restrictions on data manipulation
within the master controller, and may require the use of special
functions within the master controller, and these can take longer to
execute. (Consult the supplier of the master controller for further
information.)