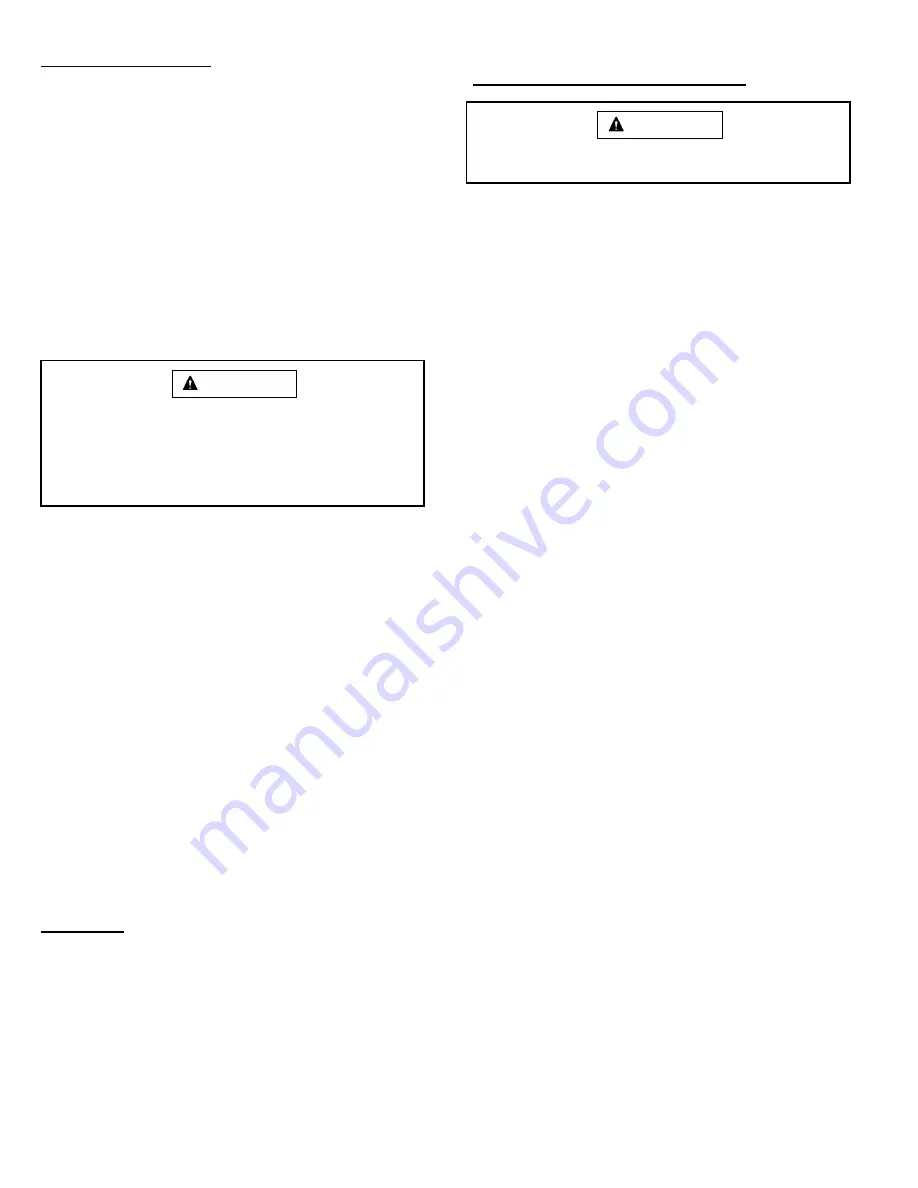
Page 4 of 9
507708-01
Issue 1337
Installation Of Line Sets
DO NOT fasten liquid or suction lines in direct contact
with the floor or ceiling joist. Use an insulated or suspen
-
sion type of hanger. Keep both lines separate, and always
insulate the suction line. Long liquid line runs (30 feet or
more) in an attic will require insulation. Route refrigeration
line sets to minimize length.
DO NOT let refrigerant lines come in direct contact
with foundation. When running refrigerant lines through
the foundation or wall, openings should allow for a sound
and vibration absorbing material to be placed or installed
between tubing and foundation. Any gap between founda-
tion or wall and refrigeration lines should be filled with a
vibration damping material.
If ANY refrigerant tubing is buried, provide a 6 inch
verticle rise at service valve. Refrigerant tubing lengths
up to 36 inches may be buried without further special
consideration. For lengths above 36 inches, consult
your local distributor.
CAUTION
Before making braze connections, be sure all joints
are clean. Before heat is applied for brazing, dry nitrogen
should be flowing through the tubing to prevent oxidation
and scale formation on the inside of the tubing.
The following is the recommended method for making
braze connections at the refrigerant line connections:
1. Debur and clean refrigerant tube end with emery
cloth or steel brush.
2. Insert tubing into swage fitting connection.
3. Wrap wet rags over valves to protect from heat.
4. Allow dry nitrogen to flow through refrigerant lines.
5. Braze joint, using a suitable brazing alloy for copper
to copper joints.
6. Quench the joint and tubing with water using a wet
rag. Leave rag on fitting body and re-wet with water
to help cool area.
Leak Check
Refrigeration lines and indoor coil must be checked for
leaks after brazing and before evacuation. The
recommended procedure is to apply a trace amount of
vapor refrigerant (approximately two ounces or 3 psig)
into the line set and indoor coil, then pressurize with 150
psig of dry nitrogen. Use a refrigerant leak detector to
check all joints. The system may also be checked for
leaks using a halide torch or pressure and soapy solution.
After completion of leak check, relieve all pressure from
system before evacuation.
Evacuating And Charging Instructions
WARNING
It is unlawful to release refrigerants into the atmosphere.
These outdoor units are pre-charged at the factory
with adequate refrigerant to handle
15 feet
of refrigerant
tubing.
1. Connect the vacuum pump to the center hose of
the manifold gauge set, the low-pressure manifold
gauge to the vapor service valve and the
high pressure manifold gauge to the liquid service
valve.
2. The valves should be kept in the “front seated”
(closed) position. This will allow evacuation of the
refrigeration lines and the indoor coil, without dis-
turbing the factory charge in the outdoor unit.
3. Follow the vacuum pump manufacturer’s
instructions. Allow the pump to operate until the
system has been evacuated down to 300 microns.
Allow the pump to continue running for an addition-
al 15 minutes. Turn OFF the pump and leave the
connections secured to the two (2) service valves.
After 5 minutes, if the system fails to hold 1000
microns or less, check all connections for tight fit
and repeat the evacuation procedure.
4. Isolate the vacuum pump from the system by
closing the shutoff valves on the gauge-set.
Disconnect the vacuum pump.
5. After evacuation of the connecting lines, remove the
service valve cap and fully insert the hex wrench
into the stem. A back-up wrench is required on the
valve body to open the valve stem. Back-out
counterclockwise until the valve stem just touches
the coined edge.
Replace service valve cap and torque to
8-11 ft-lb on 3/8” valves; 12-15 ft-lb on 3/4” valves;
15-20 ft-lb on 7/8” valves.