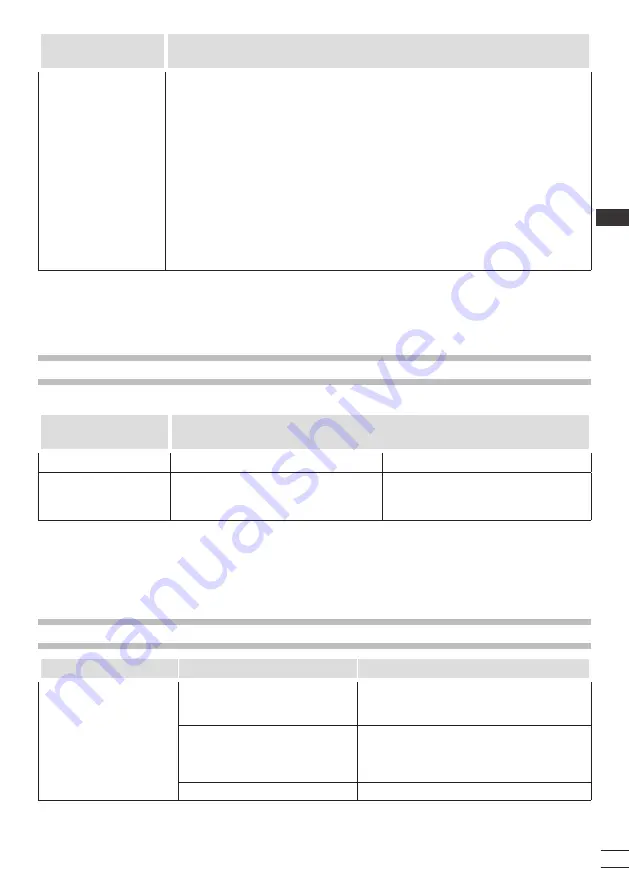
33
MAINTENANCE
SCHEDULE
JOB
Monthly
• Clean the water inlet filter (35 or 14):
refer to what has been explained previously.
• Clean the detergent suction filter (29)
.
It is normally enough to put the filter under running water or blow it with compressed
air to clean it. In the most difficult cases use a scale remover or replace it, contacting
an authorised assistance centre to buy the new filter.
• Clean the nozzle.
It is normally enough to put the pin (24) supplied through the hole of the nozzle to
clean it. If the results are not good, replace the nozzle purchasing it from an authorised
assistance centre.
The nozzle can be replaced using a 14 mm box spanner (not supplied).
• Check soundness of the water inlet and outlet circuits.
• Check tyre inflation pressure.
• Check clamping of the pump to the engine and the engine to the frame.
If clamping is found to be insecure do not, under any circumstances, use the
high pressure cleaner and contact a Specialized Technician.
CAUTION
• When working, the high pressure cleaner should not be too noisy and there should be no obvious drips
of water or oil underneath it. If this is the case have the machine checked by a
Specialized Technician
.
SPECIAL MAINTENANCE
Special maintenance must only be done by a
Specialized Technician
, complying with the following table.
MAINTENANCE
SCHEDULE
JOB
Every 200 hours
• Check the pump’s hydraulic circuit.
• Check pump clamping.
Every 400 hours
• Change pump oil.
• Check the pump suction/delivery valves.
• Check tightness of pump screws.
• Check the pump regulation valve.
• Check the safety devices.
• Every 200 hours, carry out alternately the maintenance intervals indicated in the table.
CAUTION
• The data given in the table are approximate. It might be necessary to carry out maintenance more
frequently in the case of particularly heavy work.
TROUBLESHOOTING
PROBLEMS
CAUSES
REMEDIES
When the switch (1) is
moved to
“1”
position,
LED (31) does not turn on
The switch to which the power
cable plug is connected is in
“0”
position.
Move the master switch to
“1”
position.
Tripping of system cutout device
to which the high pressure cleaner
is connected (fuse, RCCB, etc.).
Reset the cutout device.
IN CASE THIS TRIPS AGAIN, DO NOT USE
THE HIGH PRESSURE CLEANER AND
CONTACT A SPECIALIZED TECHNICIAN.
The plug is not properly fitted.
Disconnect the plug and fit it back correctly.
(continues on the next page)
EN
Содержание K Steel
Страница 2: ......
Страница 4: ...1 K Steel K Steel...
Страница 5: ...2 K Steel K Steel 7 15 10 21 7 15 10 21...
Страница 6: ...3 K Steel XL K Steel XL...
Страница 7: ...4 1 31 32 1...
Страница 9: ...6 37 7 2 6 3 3 40...
Страница 11: ...8 K Steel K Steel a b 13 35 18 34 19 27 27 28 29 11 23 a b 39 38 28...
Страница 12: ...9 K Steel XL K Steel XL K Steel XL K Steel XL 36 13 19 14 20 21 9 14 36...
Страница 13: ...10 K Steel XL K Steel XL K Steel K Steel 8 12 33 33 14 36 9 8 13 12 18 10 A...
Страница 14: ...11 K Steel K Steel 7 15 10 21 7 15 10 21 13 30 12 9 8 18...
Страница 15: ...12 K Steel K Steel K Steel XL K Steel XL K Steel K Steel 3 11 3 11 B B...
Страница 16: ...13 1 2 C D E F G...
Страница 17: ...14 K Steel XL K Steel XL K Steel K Steel H I L M I...
Страница 102: ...102 25 17 22 D 13 26 12 E 13 K Steel 8 19 35 13 18 L 14 KSteelXL 9 19 13 36 M 14 2 34 18 36 19 0 75 in I 14 25...
Страница 104: ...104 15 1 0 23 39 8 b 16 S 7 15 13 15 1 0 15 17 25 3 12 7 6 7...
Страница 105: ...105 33 10 K Steel 35 18 8 K Steel XL 14 21 27 20 9 35 14 29 24 14 200 RU...
Страница 106: ...106 400 200 1 1 3 1 0 1 35 14...
Страница 107: ...107 8 23 39 8 a 8 b 23 39 8 b 8 a 29 K Steel 7 15 K Steel 10 21 RU...
Страница 108: ...108 15 13 Total Stop 30 bar 435 psi 3 1 32 31 32 1 0...
Страница 114: ...114 16 S 7 15 13 15 1 0 15 17 25 3 12 7 6 7 33 10...
Страница 115: ...115 K Steel 35 18 8 K Steel XL 14 21 27mm 20 9 35 14 29 24 14 200 400 200 BG...
Страница 116: ...116 1 1 LED 31 0 1 RCCB 35 14 8 23 39 8 8 b 23 14 8 b 8 29...
Страница 117: ...117 KSteel7 15 KSteel10 21 RCCB 15 13 30 435 psi 1 32 31 32 1 0 BG...
Страница 118: ...NOTE...
Страница 119: ......