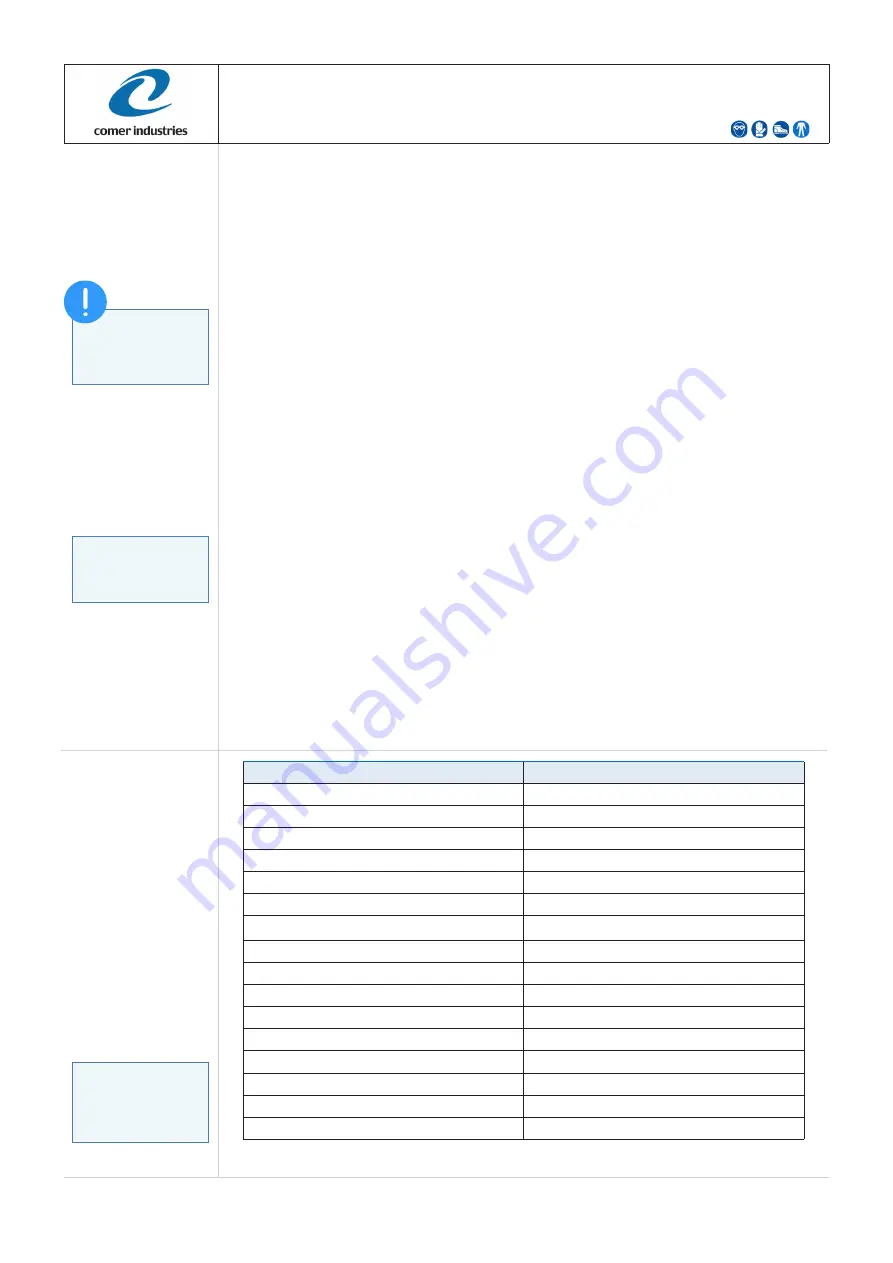
First issue 10/14
Release A10/14
PGRF
5/9
To guarantee long life and excellent performance to the gear unit, maintenance opera-
tions must be done on a regular basis.
Before
maintenance operations, authorized people must disconnect the unit power supply,
putting it “out of order”, taking all the necessary precautions to ensure it cannot be restar-
ted accidentally or any of its moving parts.
During
maintenance operations:
•
it is forbidden to work with machines in movement,
•
wear suitable protection (IPG),
•
avoid accidental restart of the unit ,
•
oil leaks should not be a source of danger,
•
do not handle units that are still very hot.
ORDINARY MAINTENANCE
includes:
•
check of oil level and oil leaks,
•
oil topping off,
•
oil replacement,
•
grease topping off,
•
periodical inspection
.
EXTRAORDINARY MAINTENANCE
include:
•
disassembly and reassembly;
•
replacement of wearing or damaged parts;
•
bearing replacement;
•
oil seals replacement.
MALFUNCTION AND ANOMALIES
When
malfunctions/anomalies are found:
•
schedule an immediate/anticipated general overhaul;
•
replace damaged or faulty components with new components if necessary.
MAINTENANCE
When
maintenance operations
are
finished
, restore all
safety conditions of
functioning
Note:
Instruction for
extraordinary maintenance
are NOT described
in this manual
Note:
described
maintenance intervals
could be different with
different machine duty
cycle
MAINTENANCE
INTERVALS
Inspection and Operations
Intervals
Oil leakage
before functioning
Brake functioning
before functioning
Oil and surface temperature
on functioning
Noise and vibrations
on functioning
FIRST OIL CHANGE
only after initial 100 service hours
Oil level check
every
500
service hours or monthly
Unit and plugs cleaning, oxidation, damage
every
500
service hours
ORDINARY MAINTENANCE
every
2000 service hours
or at least once a year
Oil replacement
ordinary maintenance
Presence of water in the oil
after oil draining
Brake test
ordinary maintenance
Screws/plugs tightening torque
ordinary maintenance
EXTRAORDINARY MAINTENANCE
every 5000 service hours
Oil seals replacement
extraordinary maintenance
Bearings replacement
extraordinary maintenance
Brake disks and springs replacement
extraordinary maintenance
ORDINARY MAINTENANCE
Maintenance operations must be carried out by qualified, trained and authorised personnel