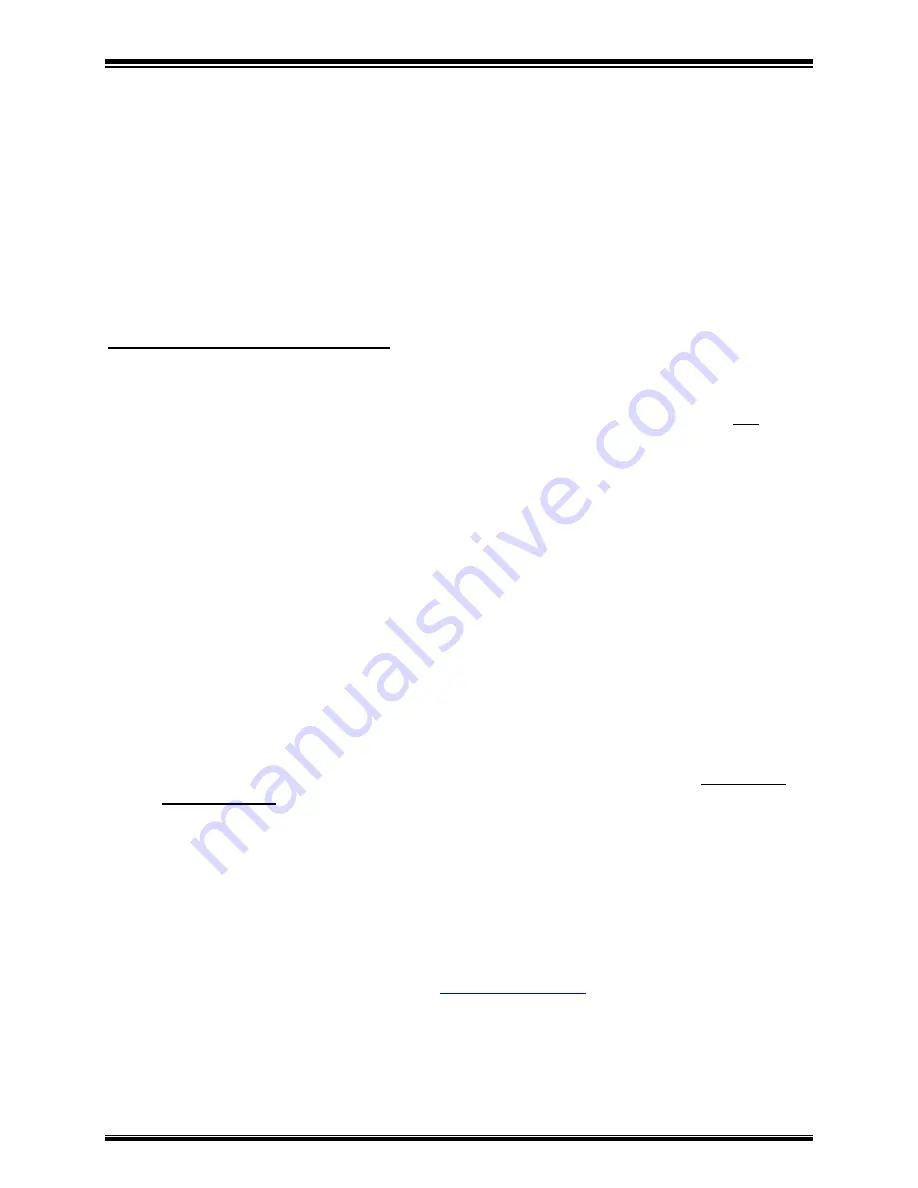
Section 4: Maintenance
MicroBlaster MB1000
Comco Inc.
4-8
Issue Date: July 2016
Moisture
Contamination of the abrasive powder due to moisture is one of the most common
problems associated with micro-abrasive blasting. Moisture causes the powder to
“clump up”, preventing it from flowing freely from the tank. Though no fault of the
MicroBlaster, it will not work efficiently if the abrasive you put in it becomes
contaminated by moisture. If the cutting action of your MicroBlaster appears to be
degraded but air is flowing freely from the nozzle, the problem is usually caused by
moisture in the abrasive powder. See Section 5 for information on how to check for
moisture in the powder.
Where the Moisture Comes From
Moisture can contaminate your powder in two ways: before it is put into the machine, or
after it is put into the tank. If your powder is stored in an area of high humidity, or the
containers are not kept properly sealed, you are putting contaminated powder into your
MicroBlaster, which will cause poor performance. Inspect your powder storage facility
and handling procedures on a monthly basis.
Abrasive powder should never be exposed to moist air with a relative humidity in excess
of 40% for more than a short time. Contaminated abrasive powder should be discarded.
The abrasive powder could also become contaminated with moisture after it has been
put into the MicroBlaster. If the unit sits depressurized for long periods of time, moisture
can enter through the Quick Fill valve and contaminate the powder. To prevent this form
of contamination, fill the tank with only the amount of abrasive you expect to use that
day. Only fill the tank at the beginning of the work shift. Don’t fill the tank and let it sit
overnight.
The most common cause of moisture contamination, however, comes from the air
compressor that feeds the MicroBlaster. Water condensation occurs in compressed air
no matter how low the relative humidity might be. For trouble-free operation, the air that
mixes with abrasive media must have less than 200 ppm moisture and less than 10 ppm
oil. The water traps of most compressors are not sufficient to provide this level of
dryness. A positive air dryer should always be installed in the air line and it should be
well maintained. Inspect the air dryer monthly to be sure it is operating properly.
Old or poorly maintained air compressors are also a source of oil contaminants in the air
supply. Oil in the air supply will not only affect abrasive flow, it can cause major
component failures within your MicroBlaster, resulting in costly repairs. If you suspect oil
in the air supply, you should install an oil filter in the line, in addition to an air dryer.
Comco maintains an extensive library of technical bulletins that address issues including
the effects of moisture on the micro-abrasive blasting process and methods for reducing
moisture contamination. They are available by contacting Customer Service at 1-818-
841-5500 or by viewing our website
– to download an electronic
copy.
3/21