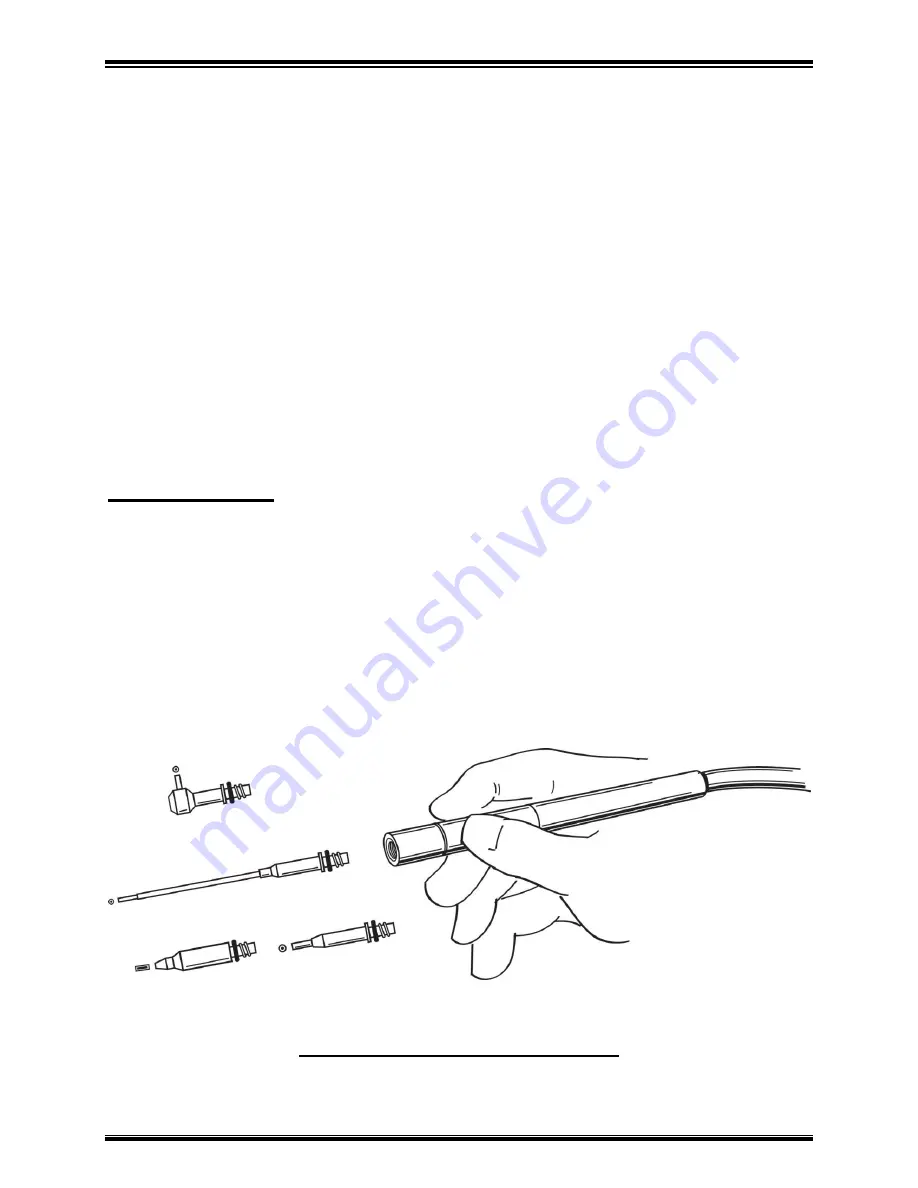
Section 3: Using the MicroBlaster
MicroBlaster MB1005
Comco Inc.
3-8
Issue Date: September 2003
Nozzle Size
The type of work to be done usually dictates the type of nozzle that must be used with
the MicroBlaster. A very tiny, precise cut or hole requires a small nozzle. If the blast
pattern is not critical, a large nozzle is preferred. With larger nozzle openings, more
abrasive can flow, and thus cutting speed is increased and efficiency will improve.
Comco offers many different sizes and configurations (see Figure 3-2 and Table 3-4),
from a 0.015" diameter round nozzle, to 0.012" x 0.150" rectangular. For most
applications a round nozzle would be preferred due to the precise spray pattern.
However when abrading large areas, a rectangular nozzle may be used as a "brush" or
"fan", which accomplishes such jobs faster than could a round nozzle. Narrow cuts may
be obtained with much less trouble and at greater speed if a rectangular nozzle is used
and properly oriented with respect to the cut.
As shipped from the factory, the MB1005 has the 0.030" diameter Hi/Performance
nozzle installed in the handpiece. This nozzle will provide the best cutting for general
applications and will handle all of Comco’s abrasives (except walnut shells).
Nozzle Selection
The nozzles provided with your MicroBlaster are chosen because of their wide range of
applications. However, since every application is different, these nozzles may not
always give the best results. For this reason, many different nozzle sizes and
configurations are available for different cutting purposes (see Table 3-4). All are
fabricated from the hardest grade of long wearing tungsten carbide bonded into
aluminum holders.
Nozzles and holders which turn the abrasive flow 90 degrees are often useful and are
available for some sizes. Comco can also custom-engineer special nozzles for unique
applications.
Figure 3-2: Changing the Nozzle
Rev. 1/04