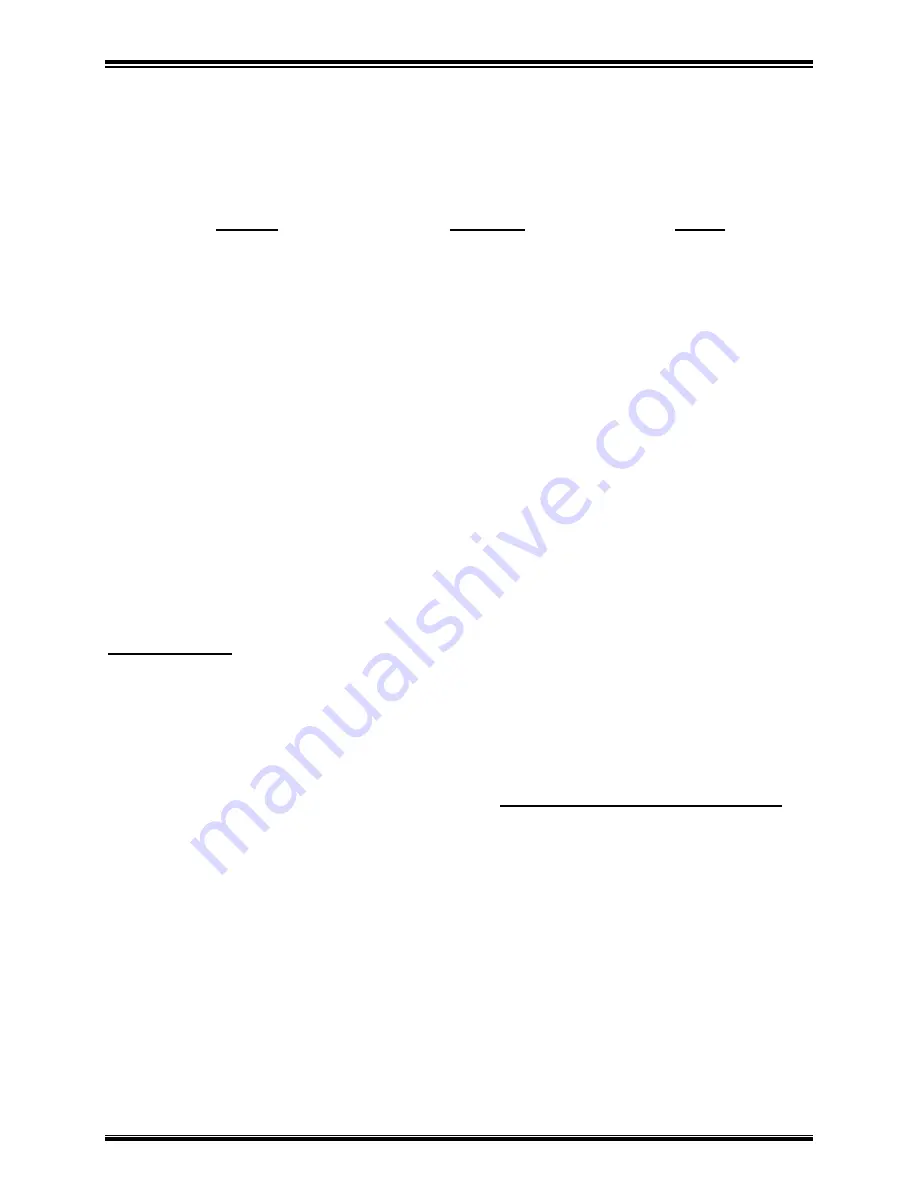
Section 3: Using the MicroBlaster
MicroBlaster MB1005
Comco Inc.
3-4
Issue Date: September 2003
Abrasive Selection
An abrasive material has three characteristics that affect its cutting action: hardness,
sharpness (shape), and particle size. The most common abrasive materials are listed
below.
Material
Hardness
Shape
Sodium Bicarbonate
Soft
Needle
Walnut Shell
Soft
Irregular
Plastic
Moderate
Block
Glass Bead
Hard
Sphere
Crushed Glass
Hard
Irregular
Aluminum Oxide
Very Hard
Block
Silicon Carbide
Extremely Hard
Block
The shape of individual particles of an abrasive material gives a good indication of its
cutting action. A spherical particle like a glass bead has virtually no cutting ability, while
a “blocky” shaped particle has points and edges that will cut and strip away surface
material on impact.
In conjunction with the basic shape of the abrasive particle, the hardness of the particle
must also be considered. For example, an irregular shaped particle such as crushed
glass may have sharper edges than a blocky particle like aluminum oxide, and would
typically cut most materials faster. However, since aluminum oxide is a much harder
substance, it will cut through hard materials with much more efficiency, since it is less
likely to shatter on impact.
Particle Size
Choosing the abrasive material defines both hardness and sharpness, so the only
variable remaining is size. Many different sizes of abrasive media are available for use
with the MicroBlaster (see Table 3-2). Particle sizes between 10 and 300 microns (800 -
75 grit) work best. Since the very small orifices in the MicroBlaster may be easily
clogged by oversized particles, it is very important that only those materials that have
been approved be used and only as directed. Extreme care should be taken that foreign
material is not allowed to fall into the powder.
Never try to salvage spent abrasive.
Typically, the larger the abrasive particle size, the faster the cutting. The MicroBlaster
propels the abrasive at a velocity approaching 500 feet per second. At this speed, the
increased mass of a larger particle will deliver a considerably larger impact to the work
surface. Also, coarser abrasives flow more freely than the finer ones, since they are less
likely to be affected by moisture from the atmosphere. Moisture is the biggest problem
you will face when working with abrasives, since moisture causes the fine abrasive
particles to stick together and “clump up”, preventing a free flow from the tank.
Problems associated with moisture in the abrasive powder are discussed in detail in
Section 4.