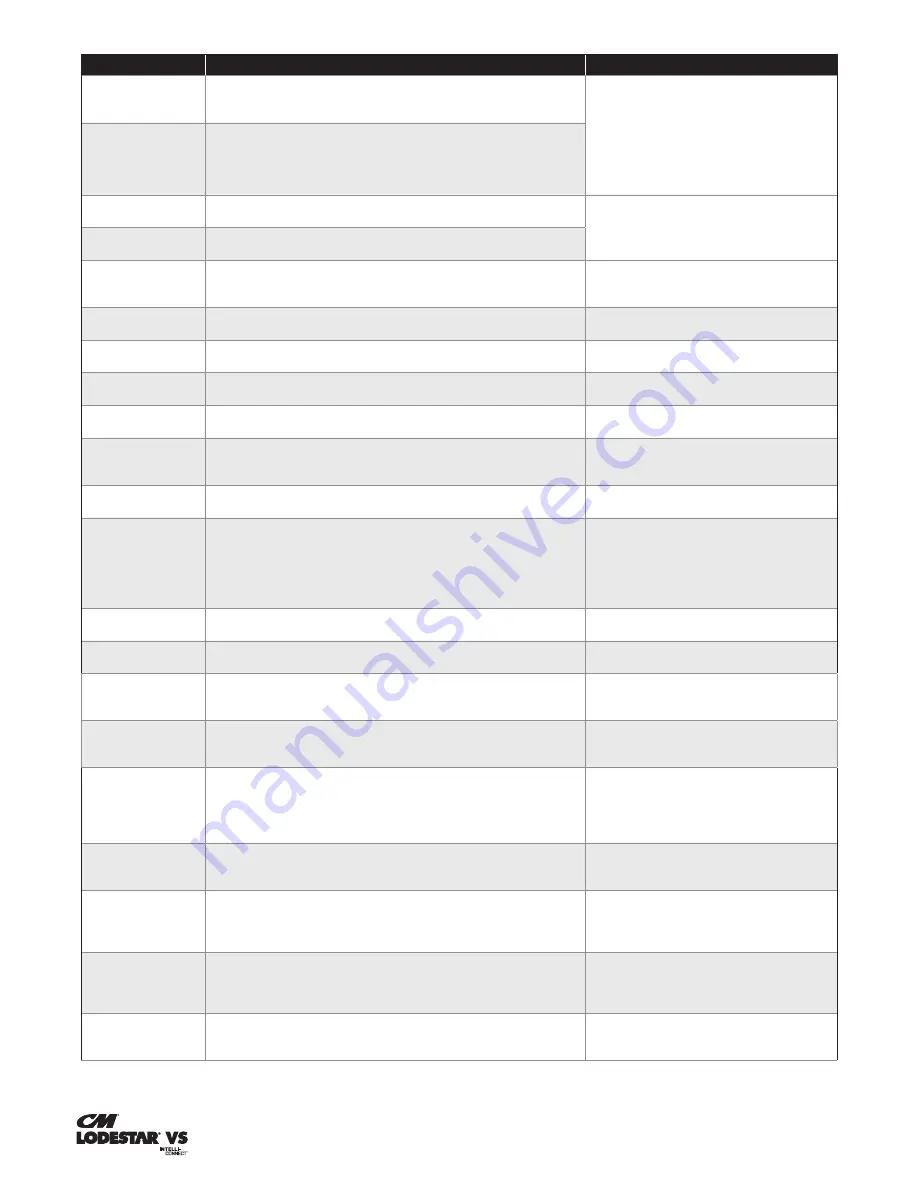
33
P/N: 192047082 (REV AD) 627NH
March 2022
VARIABLE SPEED ELECTRIC CHAIN HOIST WITH
OPTION
Fault Code
Fault or Indicator Name/Description
Corrective Action
OH1
Heatsink
MaxTemp
Overheat Fault. There are two situations that result in an overheat fault. The first
occurs when the measured heatsink exceeds 105°C. The second is the result of a
fault in the internal 24VDC cooling fan.
1.
Ensure that the heatsink cooling fans are
functioning.
2. Ensure that the heatsink is free from dirt and
debris.
3. Ensure that the inverter’s ambient temperature is
within specifications.
4. Replace the 24 VDC fan.
5. Replace the heatsink thermistor(s).
OH2
(Flashing)
Overheat 2
Overheat Alarm. Signal is input by external terminal. H01.XX = 39
OH3 Motor
Overheat 1
Motor Overheating 1. Thermistor analog input detects motor overheating.
See L01.03.
1. Check the motor rated current value, E02.01.
2. Increase cycle time OH4 Motor or reduce the load.
OH4 Motor
Overheat 2
Motor Overheating 2. Thermistor analog input detects motor overheating.
See L01.04.
OL1
Motor
Overloaded
Motor Overload Fault. Inverter output exceeds the inverter overload level.
1. Ensure drive is programmed with proper motor full
load Amps (E02.01).
2. Reduce the load.
OL2
INV Overload
Inverter Overload Fault. Inverter output exceeds the inverter overload level.
1. Reduce the load.
2. Extend the acceleration time.
OPE01
kVA Selection
kVA Settings Fault. Inverter kVA setting range is incorrect.
1. Check O02.04 constant for proper kVA.
OPE02
Parameter Range Setting Error. Parameter settings are set outside the
parameter range.
1. Press enter to view parameter.
2. Change parameter to appropriate setting.
OPE03
Terminal
Multi-Function Input Settings Fault. Set values other than F and FF
are duplicated.
1. Check the settings for H01.01 to H01.07. Verify that
the same input is not used twice.
OPE04
Terminal
Parameters do not match. The drive, control board, or terminal board has been
replaced, and the parameter settings between the controll board or terminal board
do not match.
1. Press ENTER to view the parameter.
2. Change parameter(s) to appropriate settings.
3. Set A01.05 = 5550.
OPE07
Analog Selection
Multi-Function Analog Input Setting Fault. Set values other than 00 and 0F
are duplicated.
1. Check setting for H03.02 and H03.10. Verify that
the same value is not used twice.
OPE08
Terminal
Selection Parameter error. A parameter has been changed that is not available
in the present control method.
1. Undo the last parameter change (if known).
2. Scroll through modified constants for obvious
setting error.
3. Perform a user initialize (A01.05 = 1110).
CAUTION: All settings will be restored to
the factory defaults.
OPE10
V/fPtm Setting
V/f Parameter Setting Error.
1. Check parameters E01.04 to E01.11.
OPE23
Load Check
Check C05.04 ≤ C05.07 ≤ C05.09.
1. Load check setting error.
OT1
Overtorque
Det 1
Overtorque Detection Level 1 Fault. Current is higher than set value (L06.02)
for more than set time (L06.03).
1. Check for proper programming of L06.02 and
L06.03.
OT2
Overtorque
Det 2
Overtorque Detection Level 2 Fault. Defined by L06.05. Alarm defined by L06.04.
1. Check for proper programming for L06.XX constant.
OV
DC Bus Overvolt
Overvoltage Fault. The DC bus voltage exceeds overvoltage level.
Detection level: 230V class - approximate 410V; 460V class - approximate 820V.
1. Extend the deceleration time.
2. Check for proper DBU operation.
3. Check the resistor.
4. Check the line voltage.
5. If on a load break hoist, check the gear box.
OV (flashing)
DC Bus Overvolt
Overvoltage Fault. Overvoltage occurs during stop. Main circuit DC voltage rises
above the detection level while the drive output is off. Detection level: 410V or
more for 230V; 820V or more for 460V.
1. Check the line voltage.
PF
Input Pha Loss
Input Phase Loss Fault. Inverter input power supply has open phase.
1. Check the line voltage.
2. Remove power.
3. Retighten the input terminal screws.
4. Check the fuses.
RR
DynBrk Transistr
Braking Transistor Fault. Internal Braking transistor failed.
1. Verify that the external braking resistor is
connected to the proper terminals.
2. Confirm that the proper resistor is installed.
3. Check for a short circuit across the braking resistor.
UL1
Upper Limt 1 Err
Upper Limit 1 - SLOW DOWN Indicator. Hoist has reached upper slow approach
limit. No action is required. Slow approach limits can be disabled by following the
instructions on page 19.
1. May not require corrective action.
2. Check the position of the limit switch.