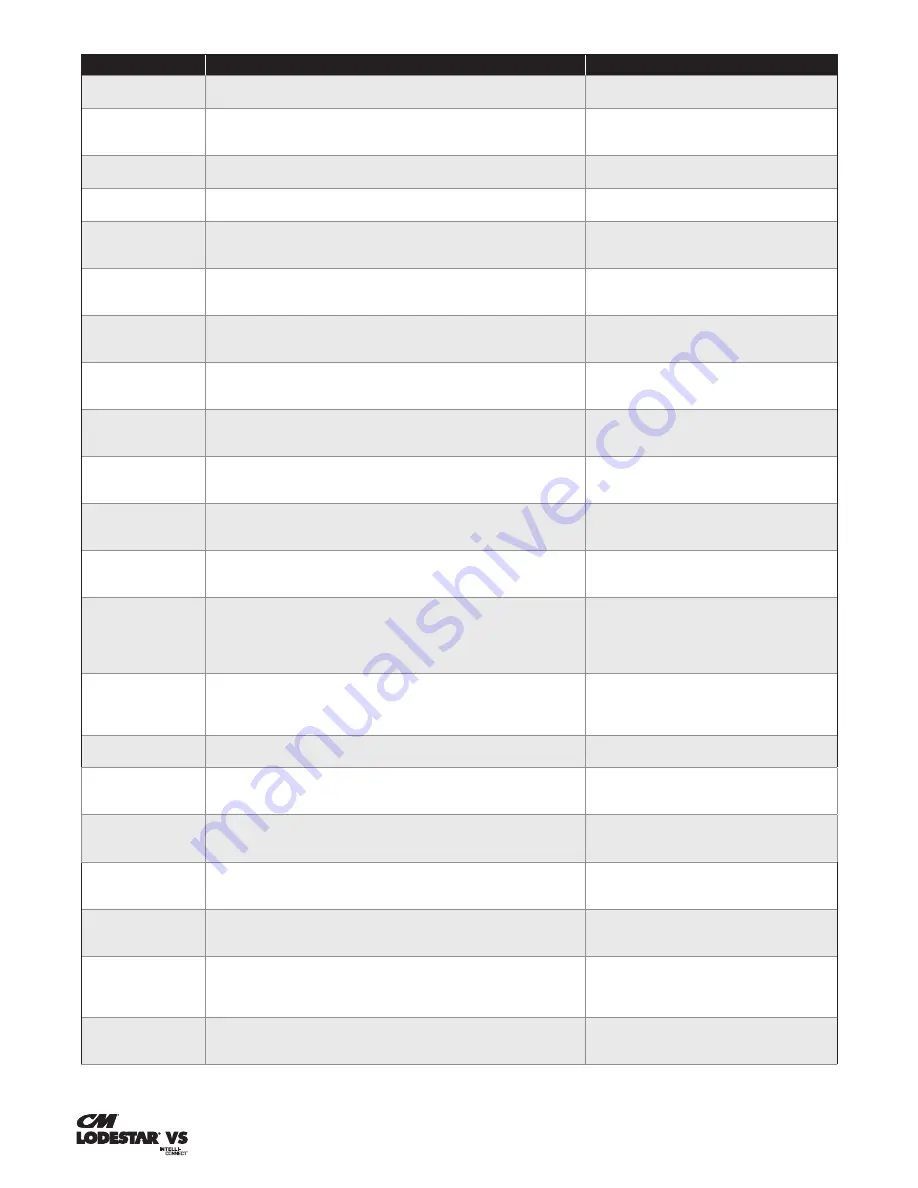
32
P/N: 192047082 (REV AD) 627NH
March 2022
VARIABLE SPEED ELECTRIC CHAIN HOIST WITH
OPTION
Fault Code
Fault or Indicator Name/Description
Corrective Action
CPF24
Drive Capacity Signal Fault. Entered a capacity that does not exist
(checked when the drive is powered up).
1. Cycle power to the drive.
2. Replace the drive.
CRST
Cannot reset. External fault occurred and reset button was pressed before motor
was completely stopped. Fault reset was being executed when a run command is
executed during a fault.
1. Wait for motor to come to complete stop.
2. Reset fault before issuing a run command.
DNE
Drive not ready
User is trying to give a run command while a FWD or REV is present at Power Up.
1. Check input terminals.
2. Check H01.01 to H01.07 programming.
EF (flashing)
External Fault
Both FORWARD/UP and REVERSE/DOWN commands are input at same time for
500 msec or longer.
1. Check control input wiring.
2. Check the sequence of operation.
EF0
Optional External
Fault
External fault input from communication option card.
1. Check communication option card connection
and signals.
2. Check external device for any fault(s).
EF1
External
Fault 1
External fault occurs on Terminal S1.
1. Check constant H01.01 for proper programming.
2. Check the conditions for input terminal S1
(U01.10).
EF2
External
Fault 2
External fault occurs on Terminal S2.
1. Check constant H01.02 for proper programming.
2. Check the conditions for input terminal S2
(U01.10).
EF3
External
Fault 3
External fault occurs on Terminal S3.
1. Check constant H01.03 for proper programming.
2. Check the conditions for input terminal S3
(U01.10).
EF4
External
Fault 4
External fault occurs on Terminal S4.
1. Check constant H01.04 for proper programming.
2. Check the conditions for input terminal S4
(U01.10).
EF5
External
Fault 5
External fault occurs on Terminal S5.
1. Check constant H01.05 for proper programming.
2. Check the conditions for input terminal S5
(U01.10).
EF6
External
Fault 6
External fault occurs on Terminal S6.
1. Check constant H01.06 for proper programming.
2. Check the conditions for input terminal S6
(U01.10).
EF7
External
Fault 7
External fault occurs on Terminal S7.
1. Check constant H01.07 for proper programming.
2. Check the conditions for input terminal S7
(U01.10).
GF
Ground Fault
Ground Fault. Current shorted to ground exceeds 50% of rated current in output
side of the drive. Setting L08.09 to 1 enable ground fault detection in models 2025
and 4014 or larger.
1. Disconnect motor from drive and check it for shorts
using a megger.
2. Ensure that R/C Surge Suppressors are used
across all brake contactor coils to prevent disturbance
by electrical transients.
HBB
Hardware Base Block. The Safe Disable Input channel is open.
1. Check if external safety circuit tripped and disabled
the drive.
2. If the Safe Disable function is not utilized, check if
the terminals HC and H1 are linked.
LC
Load Check Err
Load Check Fault. Load is greater than specified amount.
1. Reduce load.
2. Check Load Check sequence set-up (C05.XX).
LF
Output Phase
Loss
An open phase occurs at the inverter output.
1. Check for broken wires in output cable.
2. Check for open winding in the motor.
3. Check for loose terminals.
LL1 (flashing)
Lower Limit 1
Err
Lower Limit 1 - SLOW Down Indicator. Hoist has reached lower slow approach
limit. No action is required. If desired, slow approach limits may be disabled as
described on page 19.
1. May not require corrective action.
2. Check the position of the limit switch.
LL2 (flashing)
Lower Limit 2
Err
Lower Limit 2 - STOP Indicator. Hoist has reached lower limit. Run hoist UP
away from lower limit, or if limit is in an inappropriate place, reset limits as
described on page 19.
1. May not require corrective action.
2. Check the position of the limit switch.
MNT
Maintenance
Required
Maintenance Required Alert. Running time has exceeded C12.05.
1. Reset timer by MFI=5A or depress Mode/Service
key three times and enter within 2 seconds.
OC
Over Current
Output current exceeds 200% of inverter rated output current.
1. Check for a phase-to-phase short in the motor or
wiring using a megger.
2. Extend the acceleration/deceleration time.
3. Check torque limit setting.
OH (flashing)
Heatsnk Over
temp
Overheat Pre-Alarm. Heatsink is overheating. The temperature of the inverter’s
heatsink exceeded the setting in L08.02.
1. The inverter cooling fan has stopped.
2. Reduce the ambient temperature.