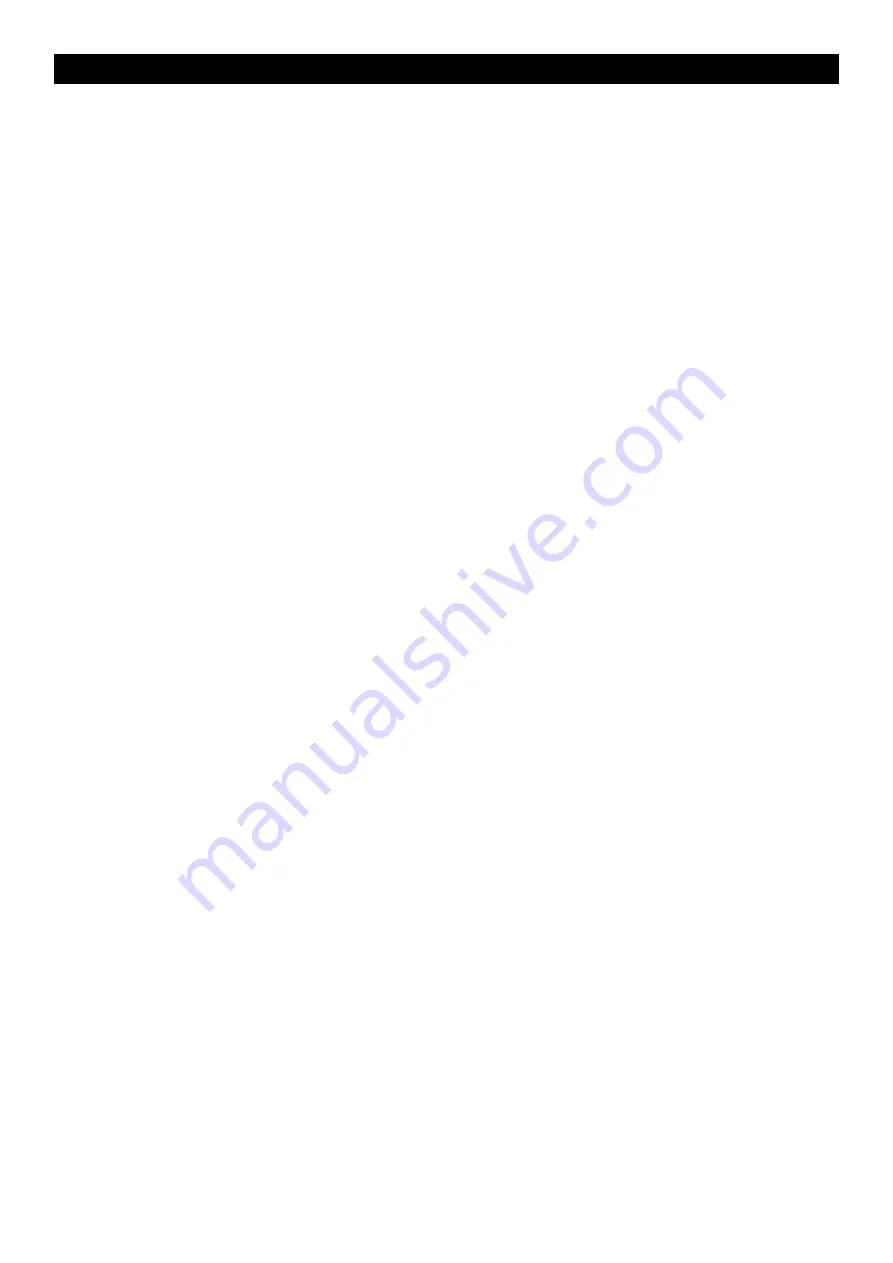
INDEX
1 - GENERAL INFORMATION...............................................................................................................................................3
2 - TECHNICAL DATA...........................................................................................................................................................3
3 - GENERAL SAFETY REGULATION.....................................................................................................................................3
4 - SAFETY DEVICES.............................................................................................................................................................3
5 - TRANSPORT.....................................................................................................................................................................4
6 - UNPACKING...................................................................................................................................................................4
7 - INSTALLATION ................................................................................................................................................................4
7.1 Installation place...............................................................................................................................................................................4
7.2 Workplace requirements..................................................................................................................................................................5
7.3 Electric hook up.................................................................................................................................................................................6
Sense of rotation check
8 - LAYOUT OF FUNCTIONAL PARTS...................................................................................................................................7
9 - IDENTIFYING WARNING SIGNALS.................................................................................................................................8
10 - IDENTIFICATION OF CONTROL....................................................................................................................................9
11- WORKING POSITION.....................................................................................................................................................9
12 - CORRECT OPERATION CHECKS..................................................................................................................................9
13 - OPERATION.................................................................................................................................................................11
13.1 Rim clamping......................................................................................................................................................................................11
Light-alloy rim clamping
13.2 Tubeless and supersingle tires...........................................................................................................................................................12
Bead losening
Demounting
Mounting
13.3 Tubed tires...........................................................................................................................................................................................17
Bead losening
Demounting
Mounting
13.4 Rims with split ring...............................................................................................................................................................................20
Bead losening and demounting
Mounting
14 - ORDINARY MAINTENANCE.......................................................................................................................................24
15 - TROUBLE SHOOTING..................................................................................................................................................25
16- MOVING THE MACHINE.............................................................................................................................................25
17- STORING......................................................................................................................................................................25
18- SCRAPPING A MACHINE............................................................................................................................................26
19- DATA ON SERIAL PLATE...............................................................................................................................................26
20- ACCESSORIES..............................................................................................................................................................27