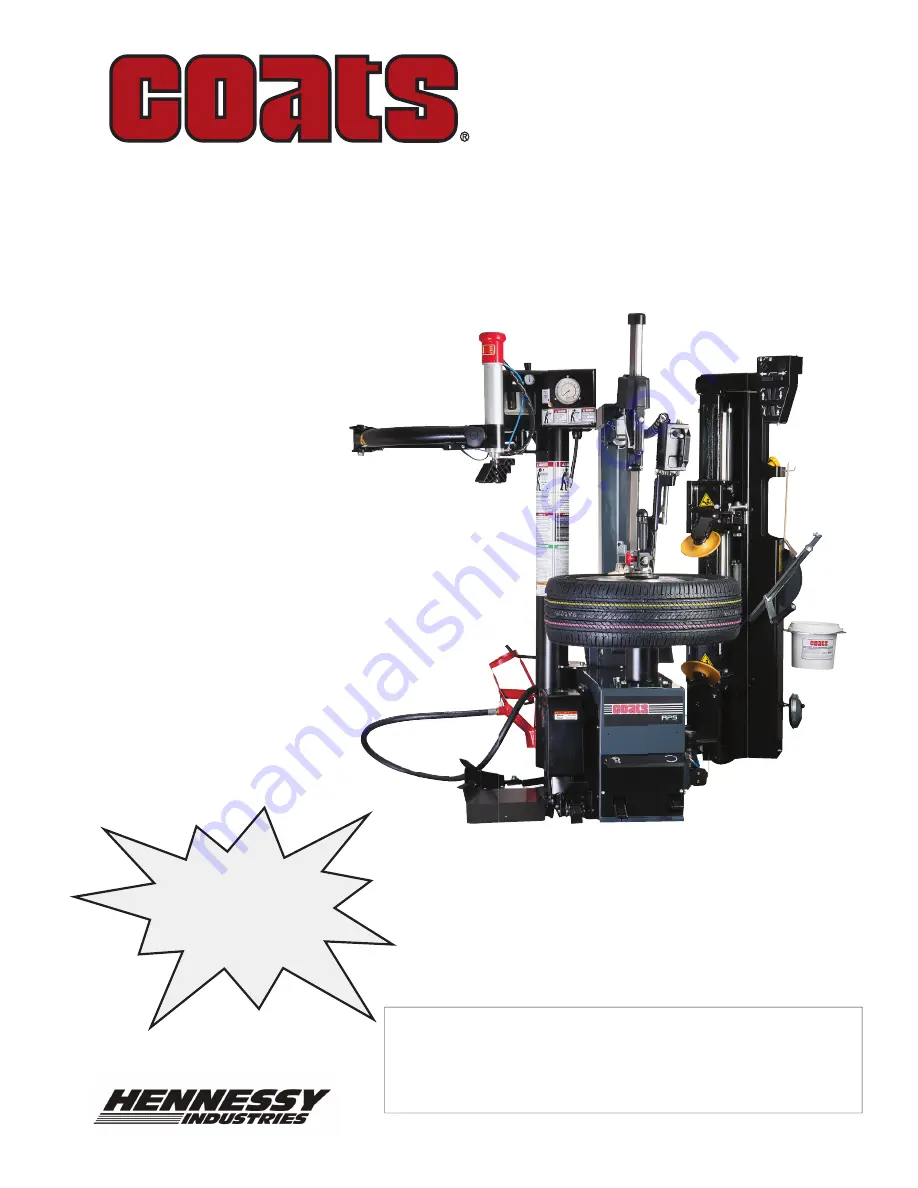
READ these instructions before placing unit in
service. KEEP these and other materials delivered
with the unit in a binder near the machine for ease
of reference by supervisors and operators.
Safety Instructions
Set Up Instructions
Operation Instructions
Maintenance Instructions
See
RIM Safety
page 4
Ì
Operating
Instructions
on page 6.
1601 J. P. Hennessy Drive, LaVergne, TN USA 37086 615/641-7533 800/688/6359 www.coatsgarage.com
Manual Part No.: 85610910 00
HENNESSY INDUSTRIES INC. Manufacturer of AMMCO
®
, COATS
®
and BADA
®
Automotive Service Equipment and Tools.
Revision:
3/17
APS 3000
Center Post Tire Changer
For servicing single piece automotive
and most tubeless light truck
tire/wheel assemblies.
Any other type, including tube type agricultrual, require
special handling. Tires identi
fi
ed as truck tires need to
adhere to OSHA standard 1910.177.