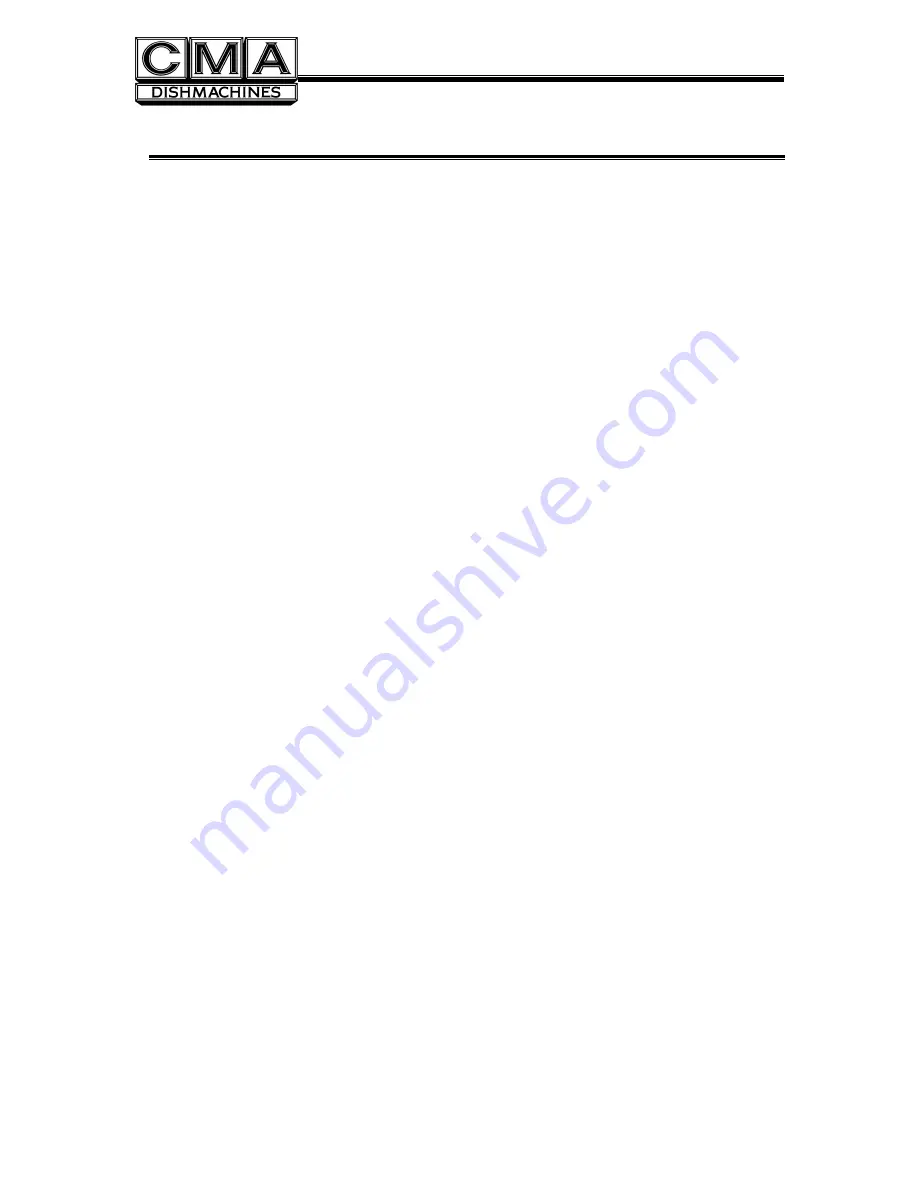
Getting Started
2. Getting Started
2.1.
Introduction to CMA-44
The CMA-44 is designed to give maximum cleaning in 44 inches. It represents the cleaning
power of machines twice its length. The curtains incorporated in the machine minimize transfer
from tank to tank during the wash and sanitizing procedures.
Energy costs for running the CMA-44 have been greatly reduced by the introduction of stage
washing. This design allows the heavy food soil to be removed in the first station, which provides
a relatively clean dish before it reaches the wash stage in the center tank.
The supply water to the CMA-44L must be a minimum of 140°F, while the CMA-44H requires two
supply lines; one at a minimum water temperature of 180°F (for RINSE), and the other at a
minimum temperature of 140° F (for FILL). Either model requires the supply water to be provided
at 24-PSI (Pounds per Square Inch) minimum with 6 GPM (Gallons Per Minute) flow rate and 200
GPH (Gallons Per Hour) recovery rate. The pipe supplying the water must be 3/4”. The plumbing
connection is located at the top back of the machine.
The CMA-44 features a scrap tray that may be emptied on a periodic basis without interruption of
the flow of work and the manner in which the tank is filled ensures that the dishes are always
rinsed with fresh water instead of re-circulated water. The CMA-44L is designed to deliver 0.8
gallons of fresh rinse water and the CMA-44H is designed to deliver 0.94 gallons of fresh rinse
water for each rack. This water flows from the rinse and power wash tank into the pre-wash tank
and then overflows into the scrap tray carrying debris with it, thereby providing a much cleaner
environment for the wash and rinse cycles.
A single-phase CMA-44 is available for installations where the only power available is 208V-
230V/1-PH.
There are also enhancements that can be chosen when desired such as an optional “Auto-Fill”
function, optional Vent Hood Adaptors and other machine accessories such as stainless steel
dishtables. Call (800) 854-6417 for more information.
This manual is structured to provide a complete reference guide to the CMA-44. It is presented in
a manner that all users will be able to comprehend and use as an effective tool in supporting the
operation and maintenance of the dishmachine. The first section explains how the machine is
packaged and what to look for when receiving the machine.
Instructions are provided in the manual explaining how to unpack the machine and then install
and set up the machine for use. Requirements are given for plumbing, wiring, and space
considerations.
These attributes of the machine are always taken into consideration by our well-
trained sales representatives prior to the order being placed
. In the manual, additional installation
guidance is given to ensure the machine can run at optimum conditions.
The
Operation
Section of the manual may be used for instruction and procedures when required.
We make this portion of the manual easy to understand so that all levels of operators may be
able to read and comprehend the operation of the machine. The function of the machine itself is
mostly automatic and takes little training to put into full operation. The Operation Section also
includes diagnostic considerations for the machine when problems occur.
We are committed to providing the best machines and customer service in the food industry and
your feedback is welcome.
MODEL CMA-44 Installation & Operation Manual Rev. 2 .15B
Page
3