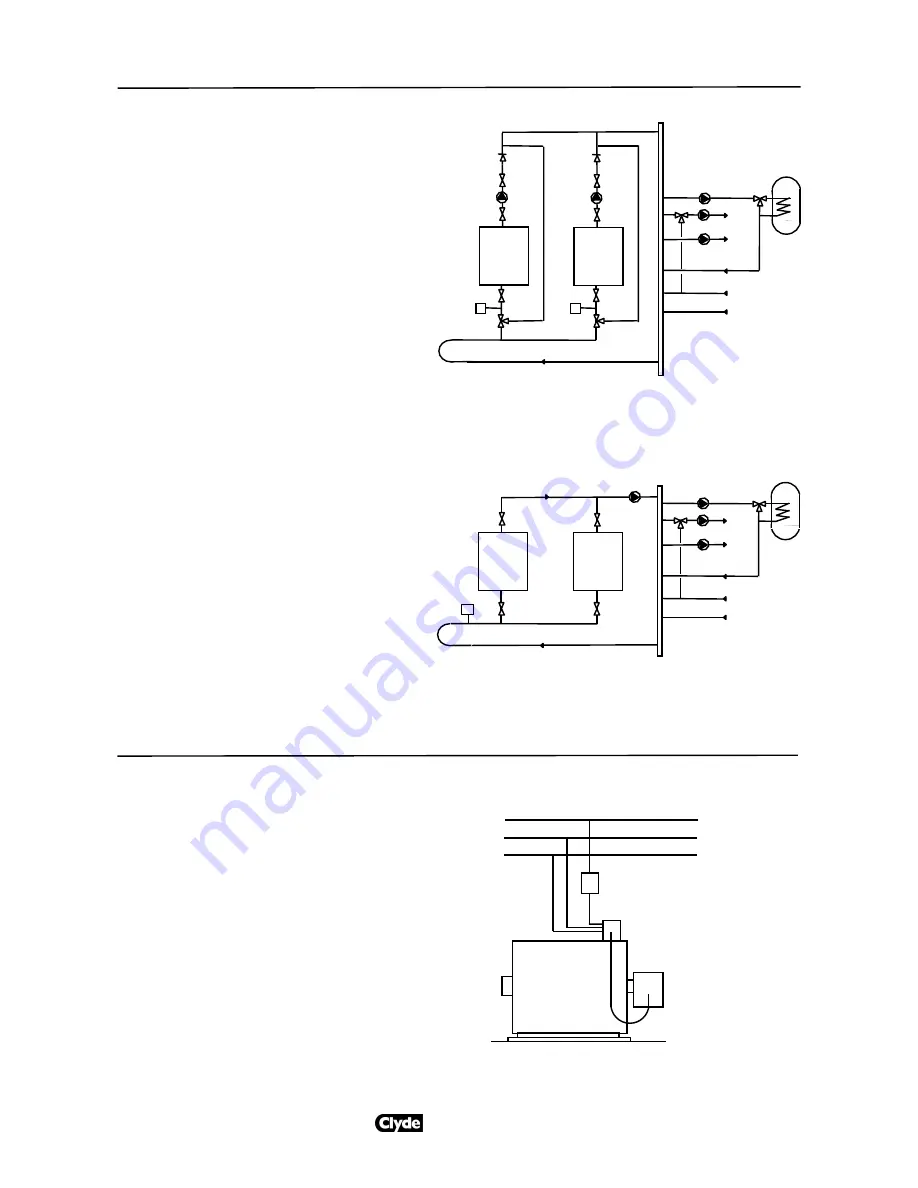
Installation requirements
Fig 5 - Electricity supply
Electrical supply (Refer Fig 5)
230Vac 1ph burners are supplied as standard. The fused
supply should be taken to the control panel only. The
harness and connector supplied will feed the burner.
The electricity supplies to the burner and boiler control
panel must be wired in accordance with IEE Regulations. A
separate supply and isolating switch is required for each
boiler in the plant room.
All isolating switches and fuses must be provided by the
installer. Burner start/run currents for fuse specification are
available on request. Burner wiring diagrams and technical
data are also available on request.
All connections between the boiler control panel and the
burner are made through harnesses with matching plugs
and sockets, supplied as standard.
Note:
Fig 5 is only diagrammatic. Double pole switches with
the required minimum separation must always be used.
Air supply
Air for ventilation and combustion must be provided for
gas fired boilers in accordance with either BS
6644:2011 or IGE/UP/10. Air supply for oil fired boilers
must conform to BS 5410 : Part 2.
Chimney design
The CKRS boiler is designed to operate with a
pressurised combustion chamber and the chimney is
not required to assist the burner in overcoming the
boiler resistance. The chimney must cater for the total
internal resistance of the flue system from each boiler
outlet and not impose an additional load on the
burner.
Water circulation (Refer Fig 4)
The flow water temperature from the boiler must reach
60°C (gas firing) or 50°C (oil firing) within 10 minutes
of the boiler being brought into operation. Thereafter,
water circulation should be maintained through the
boiler such that the boiler flow water temperature is
always above 60°C (gas firing) or 50°C (oil firing). A
pump overrun facility is necessary to ensure that
water circulation is maintained for at least three
minutes after the boiler is switched off.
There are several ways of providing boiler protection,
eg shunt pumps, primary loops, etc. A typical boiler
pump and 3-port valve arrangement is shown in Fig
4a and b.
For multi-boiler systems a ‘reverse return’ pipework
configuration is required to ensure equal distribution
of water flow through the boilers.
Water treatment
Whenever a new boiler is connected to an existing
system, the pipework must be thoroughly cleaned and
flushed. Carnot recommend that a permanent means
of filtration be fitted into the return pipework, such as a
sludge trap, hydrocyclone or full flow duplex filters.
The boiler guarantee will be invalid if waterways are
blocked by debris or carbonate deposits. Long term
water treatment is essential to the economic operation
and life of both new and refurbished heating systems.
For full information on cleaning, flushing and
protecting hot water systems, refer to BSRIA
Application Guide AG 1/2001.
T
T
T
Fig 4a Multiple boilers with individual pumps
Fig 4b Alternative arrangement for boiler protection with a primary
loop
•
•
•
•
•
Boiler
Burner
loom
Isolator
& fuse
L
Control
panel
Burner
N
E
Single
phase
motor
EDS801/3 page5