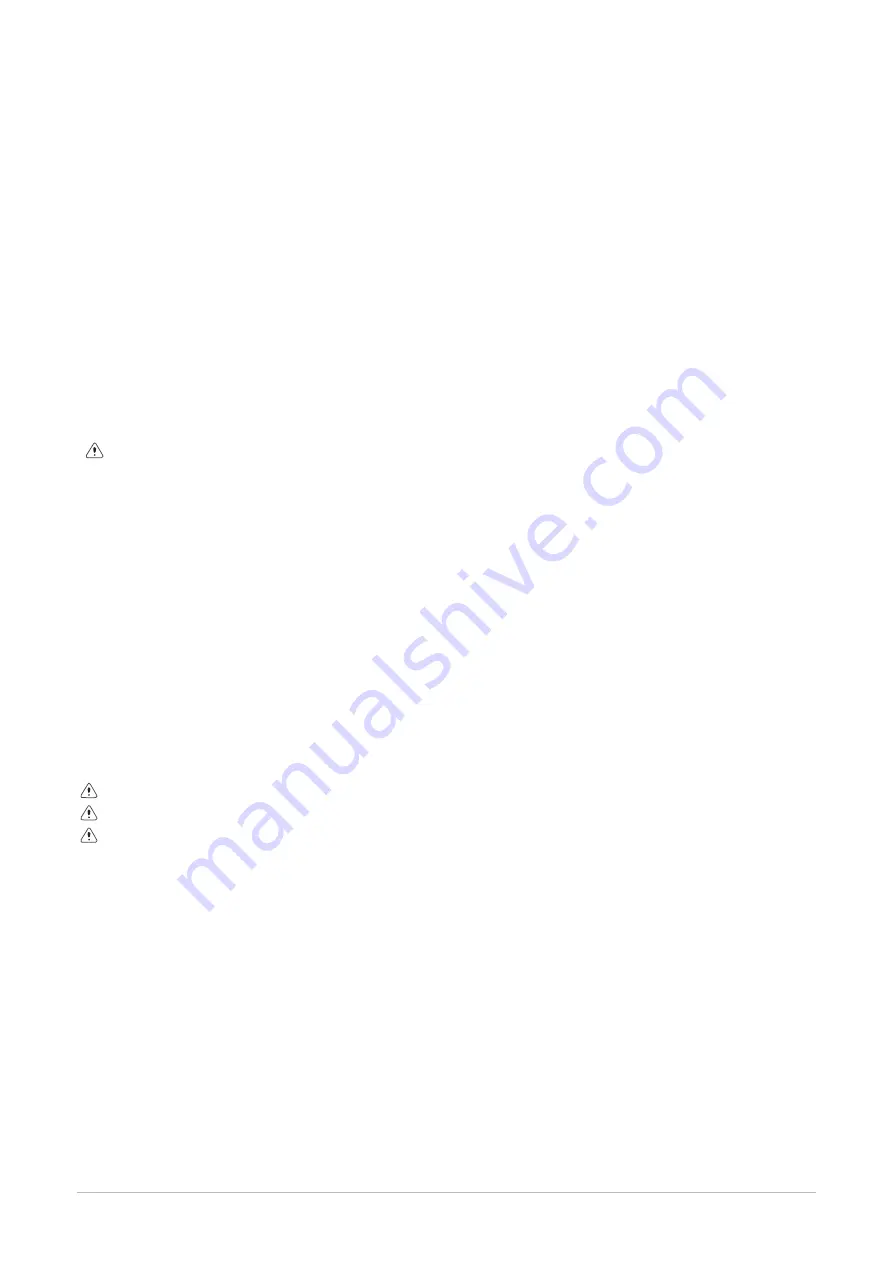
5.9 Vacuum operations
Make sure that all the service outlets are closed with proper caps; if caps are not present a leak of refrigerant can be possible.
With the taps of the motor condenser closed, drain the system.
Using a gauge group, connect the vacuum pump on both connections of the taps, make sure that the solenoid valve or any intermediate taps
are open, proceed with the vacuum.
Stop the pump at a pressure of about 100 Pa and leave it under vacuum for a few hours; a slight initial rise of pressure is normal, followed by
stabilization.
If the pressure continues to rise, it means there are either small leaks or humidity is present. In the first case, repeat the operations in the
paragraph on checking for leaks in the manual for the refrigerant pipes.
In the second case, recharge the system with refrigerant gas up to 100KPa and re-create the vacuum as described above.
Once the pressure is permanently stable, move on to the next phase, which is charging.
5.10 Refrigerant Charge
Check the type of refrigerant on the serial number label
The unit
is
shipped with a nitrogen-tight charge.
The refrigerant charge must to be completed during the start-up phase, based on the type of indoor unit and on the pipe development.
Refrigerant charge for combination with remote condenser
With the system under vacuum, close the taps of the gauge group and disconnect the vacuum pump.
Connect the refrigerant gas tank, venting the air out of the hose for connection to the gauge group.
Open the tap of the liquid line.
Open the taps of the gauge group and let liquid-state refrigerant enter using an appropriate pump.
Once charging is complete, open the gas tap so that the unit is ready to be started.
5.11 Adding oil
During operation the lubricating oil is partially mixed with the refrigerant and dragged along the refrigeration lines.
It is essential to guarantee the oil return to the compressors, especially in part load operation.
Evaluate the opportunity to add oil if the connecting pipes have a particularly extensive development.
Periodically check the oil level of the compressor on the dedicated indicator or on the schrader socket, especially after periods of
reduced load operation.
Use only Copeland EMKARATE RL32 3MAF oil.
5.6 Liquid line
The liquid line must be insulated if it is exposed to the sunlight or it crosses zones with a temperature higher than the external one, otherwise
it can be free.
Avoid excessive diameters to not cause an excessive refrigerant charge.
5.7 solenoid valve on the liquid line
It is not necessary to install a solenoid valve.
The electronic thermostatic valve operates as a solenoid valve, also in case of blackout.
5.8 Checking for leaks
1
Check carefully that the evaporator unit taps are closed.
2
Connect the pressure gauges with the service fittings (on the taps or on the connection pipes).
3
Pressurise the system with nitrogen:
mode 1: up to PS (see the label) and wait few hours
mode 2: up to PS x 1,43 law (as according to UNI-EN 378-2)
CAUTION: EXPLOSION DANGER
4
Spray using a leak detector spray taps and pipes and check if bubbles are present (gas leaks).
5
Discharge the nitrogen from the unit.
16
Содержание MSE-XSC3 100.4
Страница 1: ...MSE XSC3 90 4 160 4 Installation and operating manual...
Страница 3: ...Index of contents 1 4 2 6 3 8 4 10 5 14 6 18 7 26 8 35 9 47 10 52 11 53 12 54 57 3...
Страница 19: ...Connections performed by the Customer 19...
Страница 50: ...9 15 Compressor replacement 50...
Страница 51: ...9 16 Exchanger replacement 51...