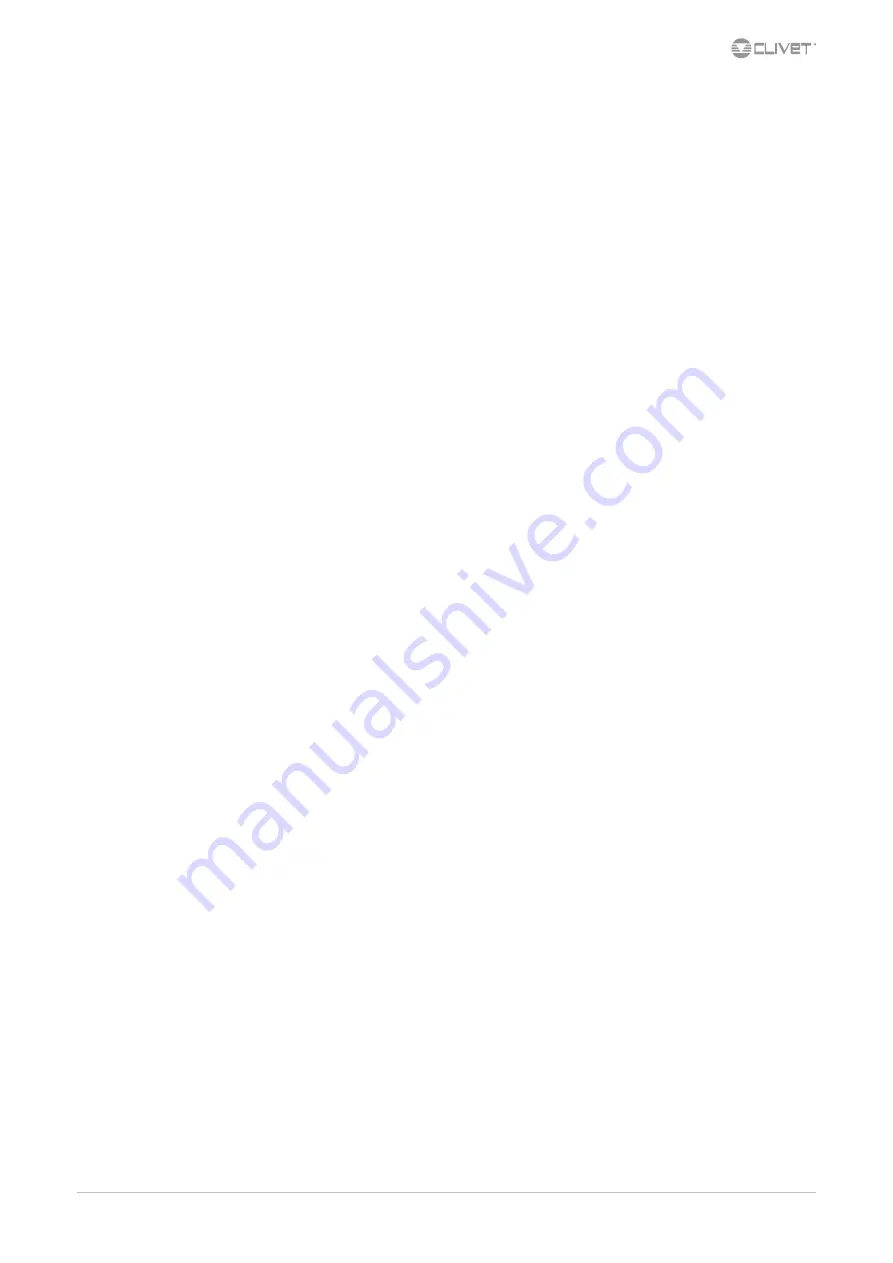
M43X41C6-03 MSE-SC
65D-180F
35
11 Residual
risks
General description
In this section the most common situations are indicated,as these
cannot be controlled by the manufacturer and could be a source of
risk situations for people or things.
Danger zone
This is an area in which only an authorised operator may work.
The danger zone is the area inside the unit which is accessible only
with the deliberate removal of protections or parts thereof.
Handling
The handling operations, if implemented without all of the protec-
tion necesssary and without due caution, may cause the drop or the
tipping of the unit with the consequent damage, even serious, to
persons, things or the unit itself.
Handle the unit following the instructions provided in the present
manual regarding the packaging and in compliance with the local
regulations in force.
Should the refrigerant leak please refer to the refrigerant “Safety
sheet”.
Installation
The incorrect installation of the unit could cause water leaks,
condensate accumulation, leaking of the refrigerant, electric shock,
poor operation or damage to the unit itself.
Check that the installation has been implemented by qualified
technical personnel only and that the instructions contained in
the present manual and the local regulations in force have been
adhered to.
The installation of the unit in a place where even infrequent leaks of
inflammable gas and the accumulation of this gas in the area sur-
rounding the area occur could cause explosions or fires.
Carefully check the positioning of the unit.
The installation of the unit in a place unsuited to support its weight
and/or guarantee adequate anchorage may result in consequent
damage to things, people or the unit itself.
Carefully check the positioning and the anchoring of the unit.
Easy access to the unit by children, unauthorised persons or animals
may be the source of accidents, some serious.
Install the unit in areas which are only accessible to authorised
person and/or provide protection against intrusion into the danger
zone.
General risks
Smell of burning, smoke or other signals of serious anomalies may
indicate a situation which could cause damage to people, things or
the unit itself.
Electrically isolate the unit (yellow-red isolator).
Contact the authorised service centre to identify and resolve the
problem at the source of the anomaly.
Accidental contact with exchange batteries, compressors, air deliv-
ery tubes or other components may cause injuries and/or burns.
Always wear suitable clothing including protective gloves to work
inside the danger zone.
Maintenance and repair operations carried out by non-qualified
personnel may cause damage to persons, things or the unit itself.
Always contact the qualified assistance centre.
Failing to close the unit panels or failure to check the correct
tightening of all of the panelling fixing screws may cause damage to
persons, things or the unit itself.
Periodically check that all of the panels are correctly closed and
fixed.
If there is a fire the temperature of the refrigerant could reach values
that increase the pressure to beyond the safety valve with the
consequent possible projection of the refrigerant itself or explosion
of the circuit parts that remain isolated by the closure of the tap.
Do not remain in the vicinity of the safety valve and never leave the
refrigerating system taps closed.
Electric parts
An incomplete attachment line to the electric network or with incor-
rectly sized cables and/or unsuitable protective devices can cause
electric shocks, intoxication, damage to the unit or fires.
Carry out all of the work on the electric system referring to the
electric layout and the present manual ensuring the use of a system
thereto dedicated.
An incorrect fixing of the electric components cover may lead to
the entry of dust, water etc inside and may consequently electric
shocks, damage to the unit or fires.
Always fix the unit cover properly.
When the metallic mass of the unit is under voltage and is not
correctly connected to the earthing system it may be as source of
electric shock and electrocution.
Always pay particular attention to the implementation of the earth-
ing system connections.
Contact with parts under voltage accessible inside the unit after
the removal of the guards can cause electric shocks, burns and
electrocution.
Open and padlock the general isolator prior to removing the guards
and signal work in progress with the appropriate sign.
Contact with parts that could be under voltage due to the start up
of the unit may cause electric shocks, burns and electrocution.
When voltage is necessary for the circuit open the isolator on the
attachment line of the unit itself, padlock it and display the appro-
priate warning sign.
Moving parts
Contact with the transmissions or with the fan aspiration can cause
injuries.
Prior to entering the inside of the unit open the isolater situated
on the connection line of the unit itself, padlock and display the
appropriate warning sign.
Contact with the fans can cause injury.
Prior to removing the protective grill or the fans, open the isolator
on the attachment line of the unit itself, padlock it and display the
appropriate warning sign.
Refrigerant
The intervention of the safety valve and the consequent expulsion
of the gas refrigerant may cause injuries and intoxication.
Always wear suitable clothing including protective gloves and
eyeglasses for operations inside the danger zone.
Should the refrigerant leak please refer to the refrigerant “Safety
sheet”.
Contact between open flames or heat sources with the refrigerant
or the heating of the gas circuit under pressure (e.g. during welding
operations) may cause explosions or fires.
Do not place any heat source inside the danger zone.
The maintenance or repair interventions which include welding
must be carried out with the system off.
Hydraulic parts
Defects in tubing, the attachments or the removal parts may cause
a leak or water projection with the consequent damages to people,
things or shortcircuit the unit.