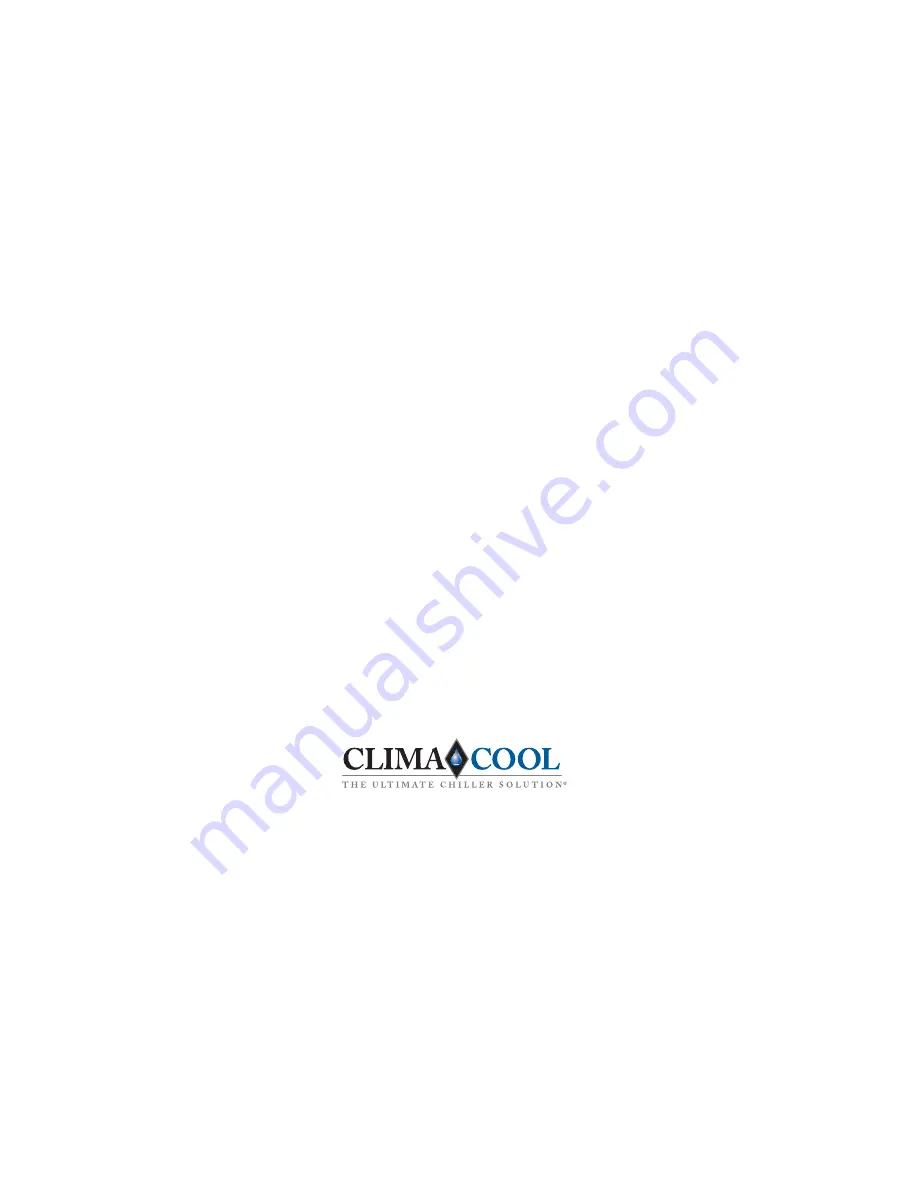
© 2006 ClimaCool Corp.
Doc# FLEX-IOM
*97B0064N01*
Rev.:
x
/10
ClimaCool works continually to improve its products. As a result, the design and specifications of each product at the time for order
may be changed without notice and may not be as described herein. Please contact ClimaCool's Customer Service Department
at (405) 745-3185 for specific information on the current design and specifications. Statements and other information contained
herein are not express warranties and do not form the basis of any bargain between the parties, but are merely ClimaCool's
opinion or commendation of its products. For the most current version of this document please visit www.climacoolcorp.com.
The management system governing the manufacture of ClimaCool's products is ISO 9001:2000 certified.
7300 S.W. 44th St.
Oklahoma City, OK 73179
405-745-3185
405-745-2072 (Fax)
www.climacoolcorp.com
®