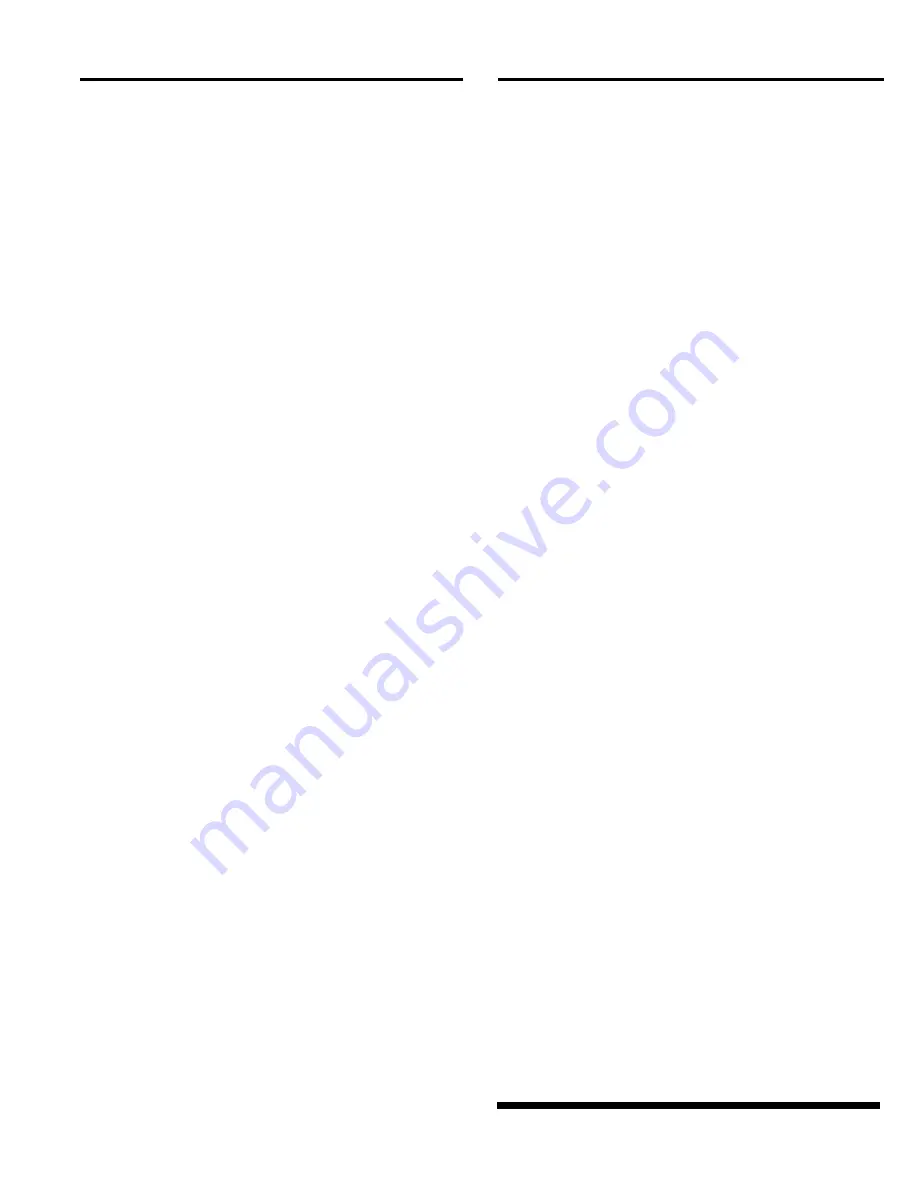
DCM-161 MINI TUMBLE BLAST CABINET
Page 7
6.3
Reduction In Blast Cleaning Rate
6.3.1
Low media level reducing media flow. Check
and fill if low.
6.3.2
Incorrect metering valve adjustment. Adjust per
Section 4.3.
6.3.3
Reduced air pressure. This may be caused by a
malfunctioning regulator, a dirty filter element in the air
filter, partially closed air valve, leaking air line, or other
air tools in use.
6.3.4
Blockage in media line or gun. See Section 6.8.
6.3.5
Worn gun parts such as nozzle or air jet. Inspect
and replace all worn parts.
6.3.6
Worn media hose. Check hose for leaks and soft
spots. Replace worn or damaged hose.
6.3.7
Moist media. Frequent bridges or blockage in
the area of the metering valve can be caused by
moisture. See Section 6.5.
6.4 Plugged
Nozzle
6.4.1
Media mixture too rich. Adjust media/air mixture
per Section 4.3.
6.4.2
Remove nozzle and check for blockage from
foreign material. If the standard tumble barrel allow large
particles to pass and block the nozzle, use the optional
1/16" hole barrel. See Section 7.1.
6.5 Media
Bridging
6.5.1
Frequent bridging or blockage in the media
metering valve can be caused by damp media. Media
becomes damp by blasting parts that are slightly oily,
from moisture in the compressed air line, or from
absorption.
6.5.2
To avoid contaminating media from the
workpiece, all parts put into the cabinet should be clean
and dry. If parts are oily or greasy, degrease and dry
them prior to blasting.
6.5.3
Moist compressed air may be due to a faulty
compressor that overheats, or pumps oil or moisture into
the air line, too long an air line permitting moisture to
condense on the inside, and from high humidity. Drain
the air filter and receiver tank regularly. If the problem
persists, it may be necessary to change media more
often, or install an aftercooler or air dryer.
6.5.4
Absorption. Some media tends to absorb
moisture from the air, especially fine-mesh media in high
humidity areas. Empty the media and store it in an
airtight container when cabinet is not in use.
6.6
Neither Media Nor Air Comes Out The Nozzle
When The Blast Cycle is Engaged.
6.6.1
Door interlocks not engaging. Check adjustment
per Section 4.4.
6.6.2
Pressure regulator may be turned down or off.
Check pressure on pilot regulator.
6.6.3
Make sure that the air compressor is on and air
supply valves are open.
6.7
Blockage In Media Hose
6.7.1
Media obstructions. Usually caused when the
media mixture is too rich. Adjust media/air mixture per
Section 4.3.
6.7.2
Wet or damp media. See Section 6.5.
6.8 Media
Surge
6.8.1
Heavy media flow. Adjust per Section 4.3.
6.9
Poor Suction In Media Hose
6.9.1
Nozzle is worn. Replace if worn 1/16" or more.
6.9.2
Blockage in media hose or nozzle. See Sec. 6.4.
6.10
Blow-Back Through Media Hose
6.10.1
Blockage in nozzle. Remove the nozzle and
check blockage.
6.10.2
Air jet washer (Fig. 6 item 5) not tightly sealed
against air jet. Tighten the bushing into the gun body.
6.11 Static
Shocks
6.11.1
Cabinet not grounded. Abrasive blasting
generates static electricity. The cabinet must be
grounded to prevent static buildup. See Section 2.3.
6.12
Dust Leaking From Dust Bag
6.12.1
Check for damaged or loose fitting dust bag.