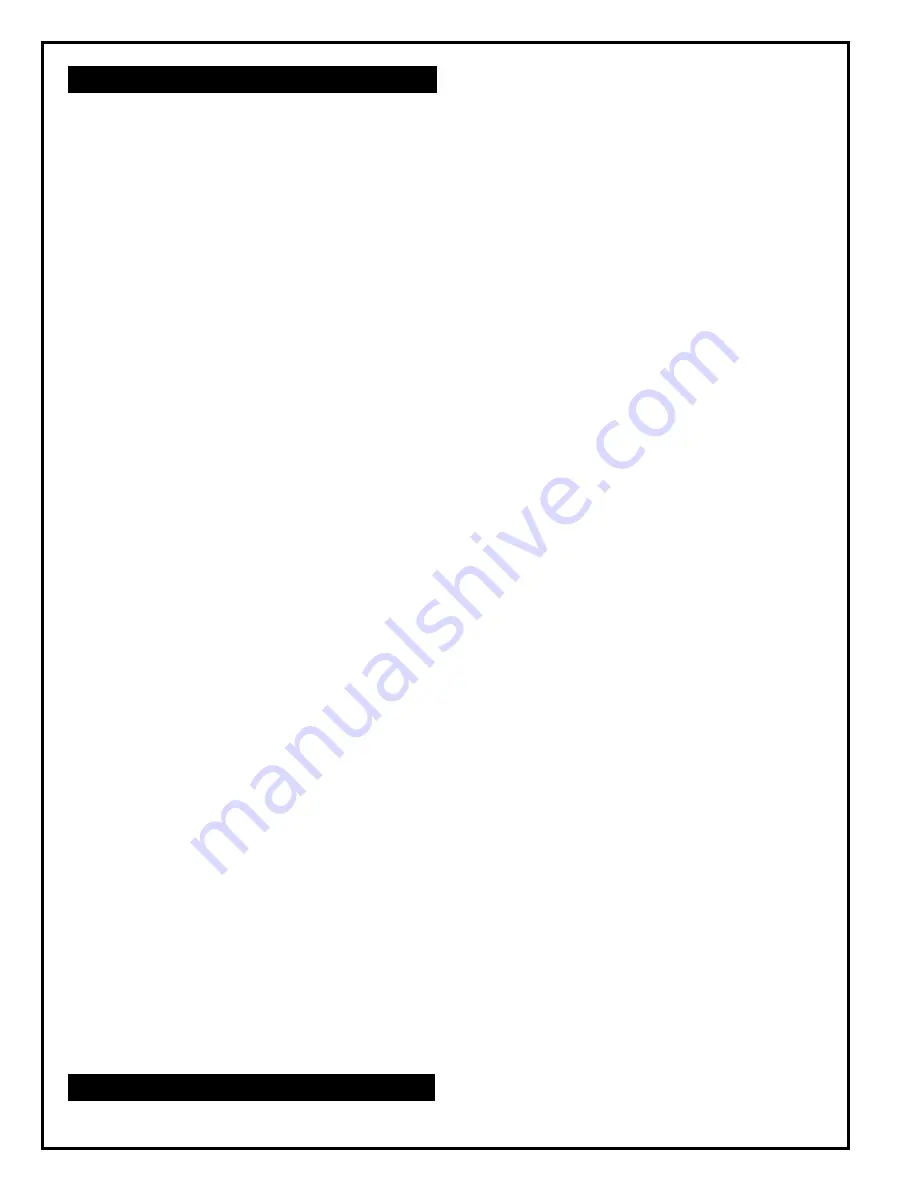
4
OPERATING INSTRUCTIONS
55 STALL-TYPE NUTRUNNERS
The 55 stall-type nutrunner is designed to develop maximum
rated torque at 90 psig. Torque output is controlled by a
pressure regulator in the air supply line. Adjust the regulator
until the desired torque is reached.
55 JOINT RATE NUTRUNNERS
The 55 joint rate tool is designed to give repeatable torque and
automatic shut off, regardless of the joint conditions (i.e. soft
pull, hard pull). Target torque is achieved through the use of an
in-line pressure regulator. Note: To ensure automatic shut off,
the air pressure should not be adjusted below 40 psig at the tool,
with the tool operating.
Operational check: Grip tool securely and be prepared to
counteract stall torque in case joint rate device improperly
functions. THIS IS A HIGH TORQUE TOOL.
THROTTLE POSITION
The throttle lever may be repositioned to accommodate proper
location for task and to avoid entrapment. Repositioning of the
angle head is done by loosening housing lock nut No. 867521,
and lifting the angle head until the spline on the angle head
clears the gear case and can be rotated to the position desired.
Lower the angle head back into place and tighten housing lock
nut.
AIR SUPPLY
For maximum performance, use a 1/2" I.D. air hose no longer
than 8' in length. If additional length is required, a 5/8" or larger
hose should be connected to the 1/2" hose.
The air hose should be cleared of accumulated dirt and mois-
ture, then one (1) teaspoon of 10W machine oil should be
poured into the tool's air inlet before connecting the hose to the
tool.
LUBRICATION
An automatic in-line filter-lubricator is recommended as it in-
creases tool life and keeps the tool in sustained operation. The
in-line lubricator should be regularly checked and filled with a
good grade of 10W machine oil. Proper adjustment of the in-line
lubricator is performed by placing a sheet of paper next to the
exhaust ports and holding the throttle open approximately 30
seconds. The lubricator is properly set when a light stain of oil
collects on the paper. Excessive amounts of oil should be
avoided.
Application of the tool should govern how frequently it is
greased. It is recommended that the idler gears and right angle
gears receive a generous amount of NLGI 2-EP grease through
the grease fittings after 40 hours of operation.
STORAGE
In the event that it becomes necessary to store the tool for an
extended period of time (overnight, weekend, etc.), it should
receive a generous amount of lubrication at that time and again
when returned to service. The tool should be stored in a clean
and dry environment.
DISASSEMBLY — GENERAL—Stall Tools
Clamp the right angle head in a vise and loosen (left hand
threads) the motor housing. Hold the tool in a vertical position
with the right angle head up. Unscrew (left hand threads) and
remove the head and transducer housing from the motor
housing. Disconnect the wire connector, No. 202183, at the
transducer and remove the transducer and gear train from the
motor housing. Slip the complete motor unit out the front of the
housing. Clamp the angle head in the vise and unscrew (left
hand threads) the right angle housing lock nut, No. 867521, to
remove the transducer housing.
Joint Rate Clutch
Clamp the right angle head in a vise and loosen (left hand
threads) the clutch housing. Hold the tool in a vertical position
with the right angle head up. Unscrew (left hand threads) and
remove the head and transducer housing from the clutch
housing. Disconnect the wire connector, No. 202183, at the
transducer and remove the transducer and gear train from the
clutch housing. Clamp the clutch housing in the vise and
unscrew (left hand threads) the motor housing. Slip the com-
plete motor unit out the front of the housing. Clamp the angle
head in the vise and unscrew (left hand threads) the right angle
housing lock nut, No. 867521, to remove the transducer
housing.The joint rate device can be removed from the rear of
the housing by tapping on the front shaft with a plastic mallet.
The bearing can be driven off the shaft by tapping on the front
shaft with a plastic mallet with the bearing hanging in a vise.
Remove the retainer ring to disassemble the drive shaft subas-
sembly.
"M" Right Angle Head
Using a suitable spanner wrench, unscrew (left hand threads)
the bearing cap, No. 864396. Remove the square drive spindle,
No. 867643, ball bearing, No. 842517, and driven gear by
clamping the square drive in the vise. Drive the right angle
housing, No. 867506, away from the square drive using a soft-
faced mallet. The ball bearing can now be removed by pressing
the square drive end of the spindle through the bearing I.D.
Press the smaller end of the spindle through the gear to remove
the driven gear. Screw a 1/40 NC bolt into the pinion gear.
Clamp the head of the bolt in the vise and use a soft-faced mallet
to drive the housing off the gear. If this method fails, it will be
necessary to use a suitable puller.
"P" Right Angle Head
Using a suitable wrench, unscrew (left hand threads) the bear-
ing cap, No. 203250. Remove the square drive spindle, No.
203249, ball bearing, No. 842517, and driven gear No. 203251,
by clamping the square drive in the vise. Drive the right angle
housing, No. 203247, away from the square drive using a soft-
faced mallet. Remove the spindle retainer nut, No. 203248, with
wrench. The ball bearing can now be removed by pressing the
square drive end of the spindle through the gear to remove the
driven gear. Remove the grease plug, No. 867546, and, using
a suitable driver, drive the pinion gear out of the right angle
housing.
"T" Right Angle Head
Loosen the bearing cap lock screw, No. 867997, and unscrew
(left hand threads) the bearing cap, No. 867509. Remove the
square drive spindle, No. 867510; ball bearing, No. 867547; and
driven gear by clamping the square drive in the vise. Drive the
right angle housing away from the square drive using a soft-
faced mallet. Press the square drive end of the spindle through
the bearing I.D. to remove the ball bearing. The driven gear may
be removed by pressing the smaller end of the spindle through
the gear. Remove the grease plug, No. 867546, and, using a
SERVICE INSTRUCTIONS
Содержание 55NJLT
Страница 19: ...19...
Страница 20: ...20 670 Industrial Drive Lexington SC 29072 Phone 803 359 1200 Fax 803 359 2013...