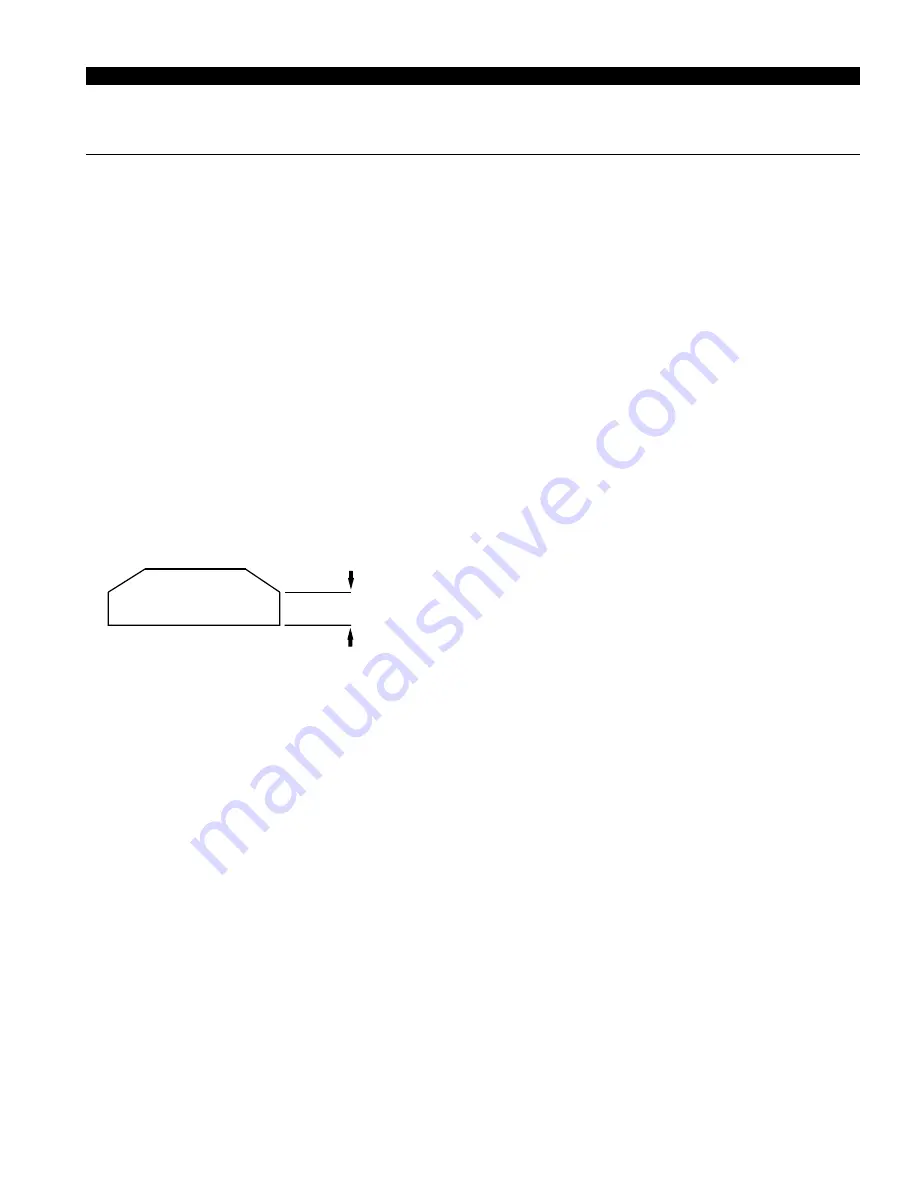
5
Safety Recommendations
WIRE BRUSHES
If a grinder is used for wire brushing applications the same
problems of balance, roundness, and trueness as experienced
with abrasive wheels prevail. Use quality wire brushes.
USE A PREVENTIVE MAINTENANCE PROGRAM
Tool abuse or poor maintenance procedures can amplify and
contribute to the vibration produced by the abrasive wheel. A
preventive maintenance program featuring scheduled periodic
inspections and proper maintenance is the best way to assure
safety in your portable grinding operations. A well managed
program can, for example, detect such things as speed varia-
tions due to wear, flanges or spindles that have been damaged
from abuse, or bad bearings damaged by foreign matter or lack
of lubrication. Problems such as these can affect the wheel
trueness when the grinder is running and contribute to the
vibration. Rotor blades that are worn or chipped can lock up
motor and result in grinding wheel spinoff and should be re-
placed. Rotor blades should be checked periodically and re-
placed if they measure less than 3/8" (9.5mm) at either end.
PROPER LUBRICATION
An automatic in-line filter-regulator-lubricator is recommended
as it increases tool life and keeps the tool in sustained operation.
The in-line lubricator should be regularly checked and filled with
a good grade of 10W machine oil. Proper adjustment of the in-
line lubricator is performed by placing a sheet of paper next to the
exhaust ports and holding the throttle open approximately 30
seconds. The lubricator is properly set when a light stain of oil
collects on the paper. Excessive amounts of oil should be
avoided.
STORAGE
In the event that it becomes necessary to store the tool for an
extended period of time (overnight, weekend, etc.), it should
receive a generous amount of lubrication at that time and run for
several seconds to distribute the oil before disconnecting from
the air supply. This will reduce the possibility of corrosion and
displace any water that may be trapped in the tool. Water trapped
in the tool could cause the governor to freeze and malfunction if
tool is exposed to freezing temperatures.
Note: Water in the air system increases tool maintenance costs
and can cause the tool to malfunction when it is stored and/or
operated in freezing conditions.
Proper repair procedures and the use of original Cleco service
parts and bearings rather than substitutes will return the tool to
factory specifications of precision and balance, and minimize
vibration.
The governor should be checked periodically to be sure the
governor mechanism is clean, in good operating condition, and
functioning properly. The 1200 Series grinders are equipped
with the CLECO SHUT-OFF disc which is designed to shut the
tool down in the event of excessive overspeed.
If the tool fails to run it may be due to the overspeed shut-off disc.
After the problem causing excessive overspeed has been cor-
rected, the 3/8" steel ball should be reseated in the governor
body and the shut-off disc assembly must be discarded and
replaced with a new assembly.
This information is a compilation of general safety practices
obtained from various sources available at the date of produc-
tion. However, our company does not represent that every
acceptable safety practice is offered herein, or that abnormal or
unusual circumstances may not warrant or require additional
procedures. Your work may require additional specific safety
procedures. Follow these procedures as required by your
company. For more information, see the latest edition of ANSI
B186.1, Safety Code for Portable Air Tools, and ANSI B7.1, Safety
Requirements for the Use, Care, and Protection of Abrasive
Wheels, available from the American National Standards
Institute, Inc., 11 West 42nd street, New York, NY 10036.
Replace if 3/8"
(9.5mm) or less
at either end.
Содержание 1200 Series
Страница 6: ...6 ...
Страница 9: ...9 NOTES ...