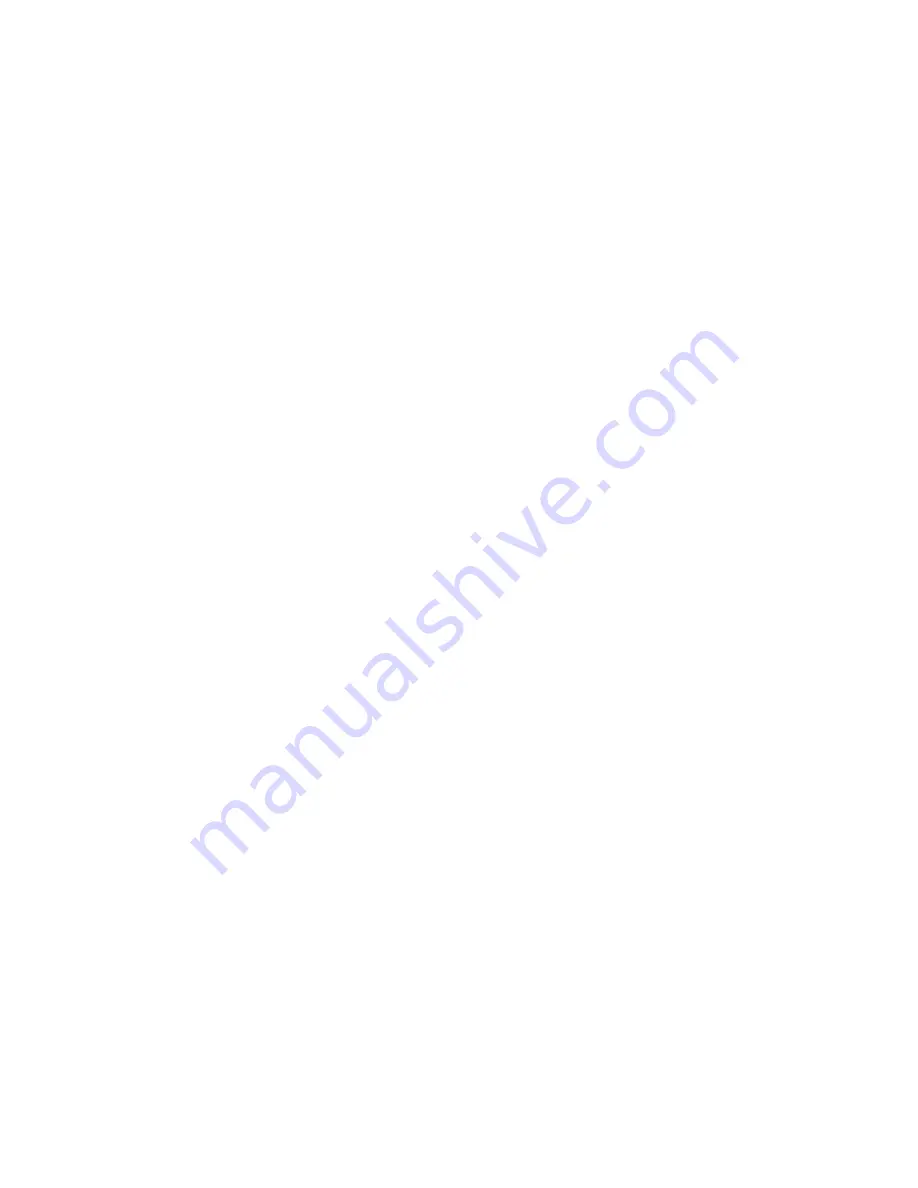
Profire EV/LNEV Burner
Chapter 2
750-364
2-5
gas pressure switches must be closed to prove proper gas
pressure.
A normally open vent valve, if required, is located between
the two automatic gas valves. This valve is shut when the
automatic gas valves are open. When the automatic valves are
closed, the vent valve is open for venting gas to the outside,
should any be present.
F. Installation
Locate the burner properly. The burner is designed for
operation with the blast tube level. Do not tilt the burner up
or excessively downward. Installation of the refractory oven
or combustion cone, shipped with the burner. Allow enough
clearance at the rear of the burner to allow the housing to
swing open for service and maintenance. Boilers operating
with combustion pressures above atmospheric pressure must
be sealed to prevent escape of combustion products into the
boiler room. The burner mounting flange is designed to
provide for a seal. The face of the boiler and burner flange
must be sealed with a rope gasket (not supplied with the
burner). Make sure the dry oven and burner blast tube are
concentric. For maximum safety, it is recommended that
boilers not operating under pressure should also be sealed.
Typical Oil Supply Loop
Continuous oil circulation must be supplied to the burner at a
rate of 50 percent greater than the high fire burning rate. The
oil circulating pump should be located as close as possible to
the storage tank to keep suction lines short and minimize
suction loss. Pipe line sizes indicated on the following oil
piping schematics are of ample size to reduce pressure losses.
If heating of the fuel oil is required, the lines must be large
enough to prevent restriction of flow through any cold spots
in the system. Note that the supply line is approximately 20
inches or higher above the burner metering pump inlet to help
eliminate air problems. Above that is an adjustable, spring-
loaded back pressure valve that sets approximately 10 to 15
PSI on the circulating loop. The return line to the tank is
connected at the discharge port of the back pressure valve.
Since air rises to the highest point, it will rise from the supply
entrance and pass through the back pressure valve to the
return line and on to the tank. Metered oil is pumped (by the
metering pump) to the common port of a 3-way valve. With
the 3-way valve de-energized, the metered oil returns to the
tank through the back pressure valve and return line. When
the 3-way valve is energized, metered oil is passed on to the
burner oil nozzle and atomized by air from the compressor.
The proper strainers, check valves, vacuum, and pressure
gauges, etc. should be installed as indicated. All lines should
be pressure tested after installation.
Oil Circulating Loop Operation
An oil circulating pump provides continuous oil circulation to
the circulation loop. A back pressure valve holds 10 to 15 psi
on the loop system. With the oil supply line connected only to
the oil metering pump inlet, all oil must pass through the
pump. During pre-purge, unmetered oil flows through a
bypass section of the oil metering pump. Metered oil passes
through the metering section to a de-energized 3-way oil
valve (common port). Both unmetered and metered oil must
pass through the back pressure valve and return to an oil
storage tank. The oil metering pump will only meter oil. It
will not serve as a circulating pump. At trial for main flame
(main fuel), the 3-way oil valve is energized admitting
metered oil to the nozzle for atomization and fast smooth
ignition. Unmetered oil continues to flow through the bypass
section of the oil metering pump and returns to an oil storage
tank.
Circulating Oil Pump
A circulating oil pump is required to deliver fuel oil from the
storage tank to the burner at a minimum of 150% of the
maximum burner firing rate. The excess oil allows a margin
for piping error, viscosity changes in the fuel oil, and
circulating pump wear. Correct pipe sizing is determined by
circulating rate, not burner capacity. Install the pump as close
to the supply tanks as possible. Suction lift should be as low
as possible. Maximum suction of 15" Hg vacuum is good
practice for either light or heated heavy oil. The strainer
should be installed in the suction line just ahead of the
circulating pump to prevent foreign material from entering
the pump. Locate the strainer so it may be easily cleaned.
Back Pressure Valve
A back pressure valve, similar to Watson McDaniel type "R,"
needs to be installed on the return line. This valve must be
installed in an upright vertical position. Before installing the
valve, be sure to blow out the pipe line, removing all dirt, pipe
scale and sediment. This type of valve is actuated by the
system pressure which enters the body beneath the main
valve. Valve loading is provided by a spring that can be
adjusted to the desired set pressure.
To adjust the set pressure, remove the top cap, loosen the
brass locknut and adjust the pressure with the steel setscrew.
By increasing the compression on the spring, screwing down
the screw, you increase the set pressure within the limits of
the spring range. Reversing the setscrew lowers the set
pressure.
Adjust to 10-15 PSI for No.2 oil systems. When the desired
pressure is reached, tighten the locknut and replace the top
cap and gasket.
Gas Piping
Gas service and house piping must supply the quantity of gas
demanded by the unit at the pressure required at the burner
gas train inlet. All piping must be in strict accordance with
applicable codes, ordinances, and regulations of the
supplying utility. In the absence of other codes, piping should
be in accordance with the following standards: "National Fuel
Содержание FLX 1250
Страница 6: ...iv...
Страница 10: ...Chapter 1 GENERAL DESCRIPTION 1 4 750 364...
Страница 32: ...Chapter 3 Pressure Vessel Care 3 10 750 364...
Страница 49: ...Troubleshooting Chapter 6 750 364 6 5...
Страница 50: ...Chapter 6 Troubleshooting 6 6 750 364...
Страница 58: ...Chapter 7 Inspection and Maintenance 7 8 750 364...
Страница 65: ...Parts FLX 750 364 8 7 Temperature Controls 2 2 3354 817 3354...
Страница 66: ...FLX Parts 8 8 750 364 Level Controls...
Страница 69: ......
Страница 70: ...e mail info cleaverbrooks com Web Address http www cleaverbrooks com...