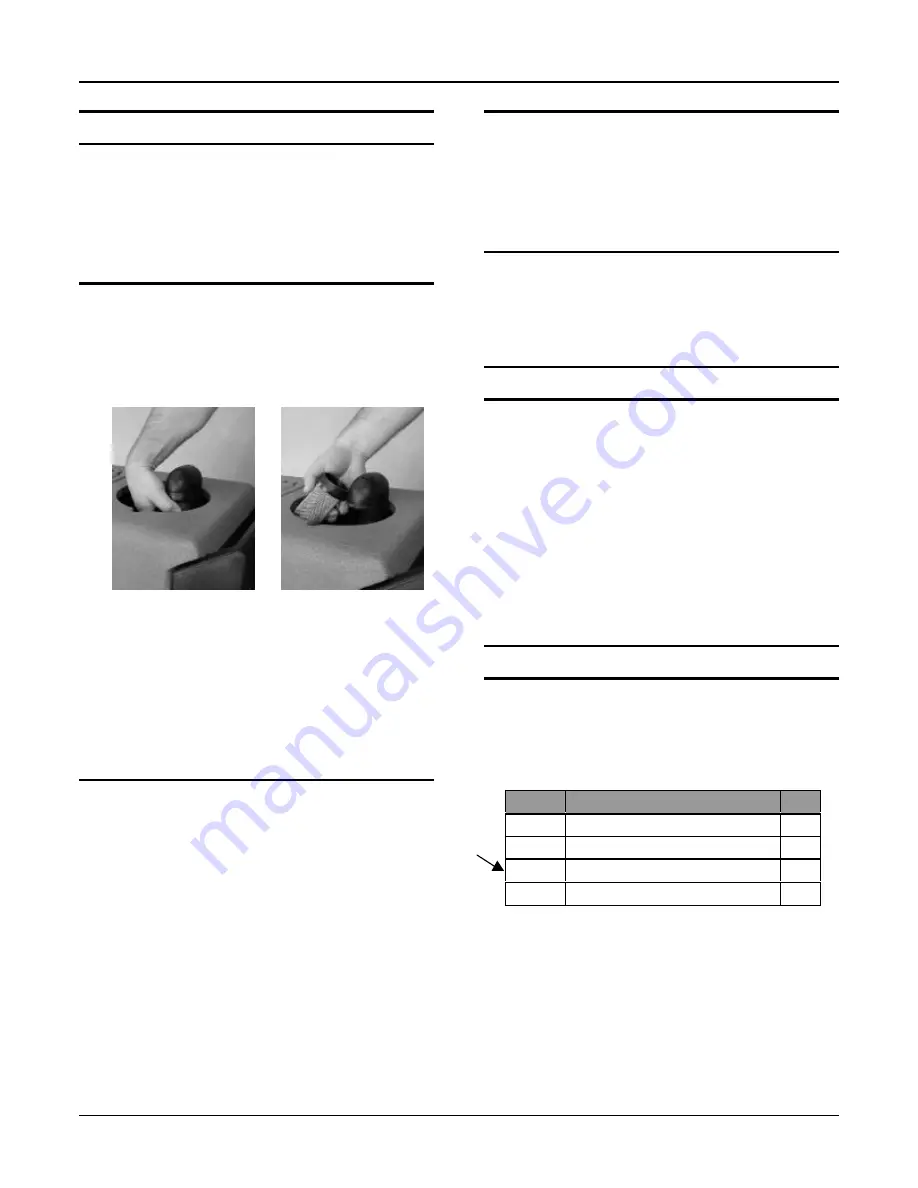
36456-E3H-Raptor CE (04-01)
7
OPERATION
MACHINE MAINTENANCE
To keep machine in good working condition, simply
follow machine’s daily, weekly and monthly
maintenance procedures.
FOR SAFETY: When servicing machine, unplug
cord from wall outlet.
DAILY MAINTENANCE
(Every 4 Hours of Operation)
1. Empty and rinse out recovery tank thoroughly.
2. Remove float shut-off screen from recovery tank
and clean (Figure 12.)
3. When solution tank is empty, remove and clean
solution filter screen located in the bottom of the
solution tank.
4. Wipe off power cord and check for damage,
replace if necessary. Coil cord neatly after use.
5. Clean machine with an all purpose cleaner and
damp cloth.
WEEKLY MAINTENANCE
(Every 20 Hours of Operation)
1. Inspect vacuum hoses for holes and loose cuffs.
2. Inspect spray pattern for plugging. If plugged,
remove spray tips and soak them in acetic acid
solution for up to six hours. Do not use pointed
objects to unplug tips, damage will occur.
FOR SAFETY: When using machine, follow mixing
and handling instructions on chemical containers.
3. Inspect cord and cord grip for damage. Replace
immediately if damaged.
4. Lubricate metal shaft on recovery tank drain with
water resistant oil.
5. Lubricate female hose couplers with lightweight
oil.
MONTHLY MAINTENANCE
(Every 80 Hours of Operation)
1. Lubricate wheels with water resistant oil.
2. Inspect machine for water leaks and loose
hardware.
QUARTERLY MAINTENANCE
(Every 250 hours of Operation)
Check vacuum motor for carbon brush wear. Replace
motor if worn to a length of 10mm (0.38”) or less.
STORING MACHINE
1. Before storing machine, be certain to drain and
rinse tanks of all water.
2. Store machine in a dry area in the upright position.
3. Open recovery tank lid to promote air circulation.
ATTENTION: Do not expose to rain. Store
indoors.
ATTENTION: If storing machine in freezing
temperatures, be sure that machine and solution
system are completely drained and dry.
RECOMMENDED STOCK ITEMS
Refer to Parts List section for recommended stock
items. Stock items are clearly identified with a bullet
preceding the parts description. See example below:
PART #
DESCRIPTION
QTY.
J-30.
LID, DOME
1
•
J-38GRANITE
TOP,SOL TANK ROTO GRANITE
1
J-39.5GRANITE
HANDLE,WASTE TANK ROTO GRANI
1
J-39GRANITE
WASTE TANK, ROTO GRANITE
1
FIG. 12