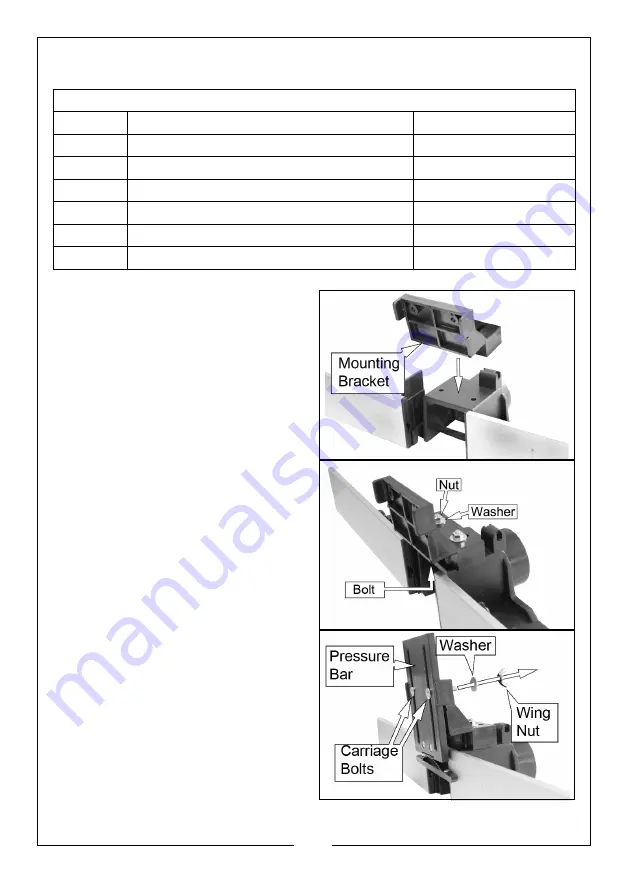
12
Parts & Service: 020 8988 7400 / E-mail: [email protected] or [email protected]
FITTING THE DOWNWARD PRESSURE BAR
1. Fit the mounting bracket to the
central part of the main fence as
shown.
2. Secure in place using 2 x M6 x 40
bolts (from below), 2 washers and
2 x M6 nuts supplied.
3. Position the pressure bar and lock
in position using the 2 carriage
bolts, 2 washers and 2 wing nuts
provided.
Parts needed for this step
1 x
Mounting Bracket
2 x
Bolt
M6 x 40
2 x
Nut
M6
4 x
Washers
6mm
1 x
Pressure Bar
2 x
Carriage Bolts
M6 x 35
2 x
Wingnuts
M6
Содержание CBTSR
Страница 28: ......