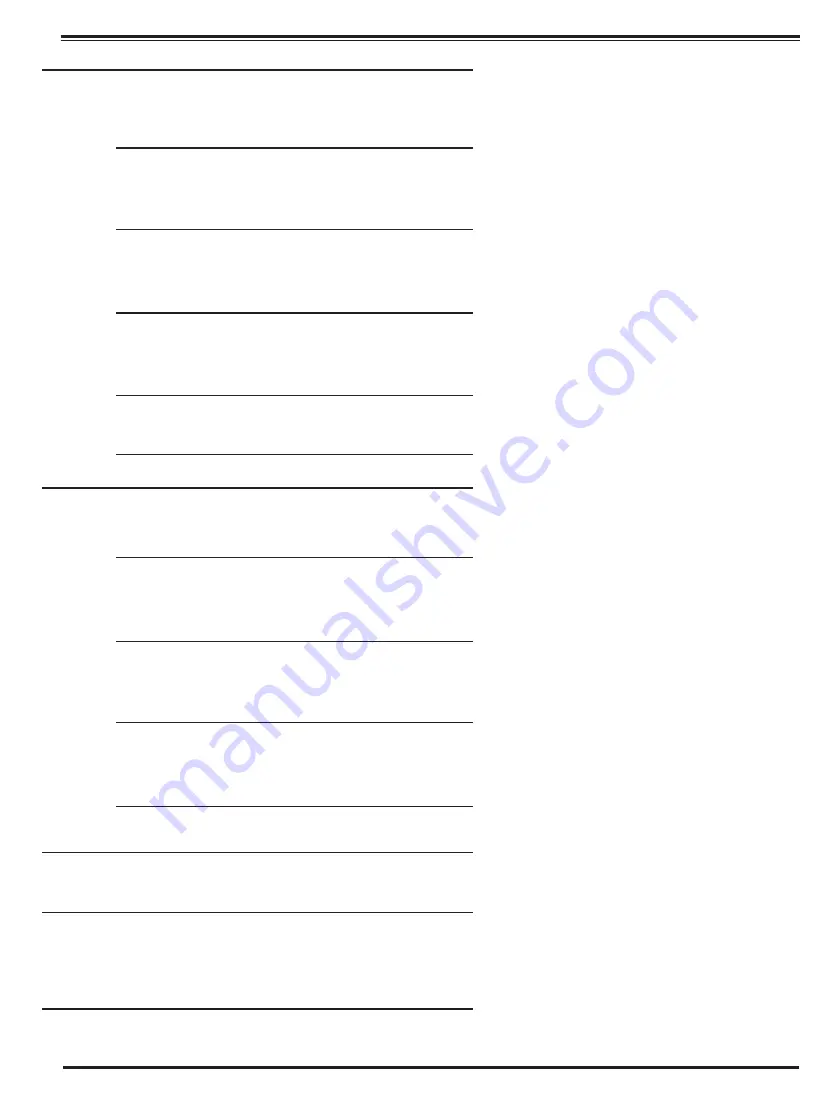
FREEDOM OF MOVEMENT
The following procedures can be used to determine if the
valve opens and closes fully. During this test the diaphragm
can be checked for damage.
1.The Powertrol Valve will have a control to open and close
the valve. Position the control so that pressure is applied to
the cover chamber (above the valve diaphragm). This will
close the Powertrol Valve. Check the drain from the control
that discharges to atmosphere.
Once the liquid from the lower diaphragm chamber is drained
the discharge should stop. If the discharge continues after the
normal time it takes to drain then the diaphragm is damaged,
or the stem nut is loose, or the stem o-ring is leaking. If the
discharge is continuous from both chambers then there is a
possibility that the diaphragm or the pilot control is damaged.
If the valve is equipped with a "Dry Drain" (control drain piped
to downstream end of the valve) then same procedure is fol-
lowed except the CK2 Shutoff Cock on the downstream end
of the valve must be closed and the drain line disconnected
and drained to atmosphere. It can then be checked as above.
Measurement of the vertical travel of the stem (diaphragm
assembly) will make it possible to determine if the travel, or
stroke is restricted. The following chart provides this mea-
surement. It is necessary to have either the X101 Valve
Position Indicator or X105 Limit Switch Assembly installed on
the valve to visually check the travel.
Mark the position of the stem on the X101 or X105 when the
valve is closed. Reposition the control so that pressure is
applied below the diaphragm and the cover chamber is
drained. Determine the extent of the stem travel. Check this
movement with the stem travel chart. If the stroke is different
than listed (5% to 10%) then there is good reason to believe
something is mechanically restricting the stroke of the valve
at one end of its travel. If it is determined that flow does not
stop through the valve when in the indicated "closed" position,
the obstruction probably is between the disc and the seat, or
in the power unit chamber below the diaphragm. If the flow
stops, the obstruction is likely in the cover chamber above the
diaphragm or possibly above the disc retainer. Refer to the
sectional view under Principle of Operation.
If operation of the valve a few times does not dislodge the for-
eign object obstructing the diaphragm assembly (stem) move-
ment then the valve must be disassembled and the problem
located and corrected. See disassembly instructions.
INCHES
1
1 1/4
1 1/2
2
2 1/2
3
4
6
8
10
12
14
16
MM
25
32
40
50
65
80
100
150
200
250
300
350
400
INCHES
0.3
0.4
0.4
0.6
0.7
0.8
1.1
1.7
2.3
2.8
3.4
3.9
4.5
MM
8
10
10
15
18
20
23
43
58
71
86
99
114
SYMPTOM
Valve fails to
close.
Valve fails to
open.
Valve closes but
leakage occurs.
O-Ring failure
*POSSIBLE
CAUSE
Stem stuck in open position.
Worn diaphragm
or loose upper
stem nut
Foreign object on
valve seat.
Pressure not being
released from power
unit chamber.
Operating
pressure not
getting into valve
cover.
Insufficient
line pressure.
Stem stuck in
closed or semi-
open position.
Worn diaphragm
or loose upper
stem nut.
Foreign object on
top of disc retainer
Pressure not being
released from
cover chamber.
Operating pressure not
applied into power
unit chamber.
Worn disc or seat.
Mineral deposits
on stem cause
abrasion on ring.
TEST
PROCEDURE
Vent power unit cham-
ber. Apply pressure to
cover chamber. Valve
should close.
Apply pressure in
power unit chamber
and vent cover.
Continuous flow from
cover indicates this
trouble.
Valve opens okay but
only closes part way.
Make sure
pressure is being
released by opening a
fitting into the cham-
ber. If valve then clos-
es refer to remedy.
Use pressure gauge
or loosen cover plug
to check for pressure.
Check line pressure.
Vent cover. Apply
pressure to power unit
chamber.
Apply pressure in
power unit chamber
and vent cover.
Continuous flow from
cover indicates this
problem.
Valve closed okay
but won't open all
the way.
Open a fitting or
remove a plug from
cover chamber if
cover chamber vents
and valve opens, see
remedy.
Loosen a fitting in this
chamber to check for
pressure at this point.
The best procedure
here is to disassemble
the valve and inspect
these parts.
Remove pressure
from both cover and
power unit chambers
and apply line pres-
sure to valve. Open
line from power unit
chamber and observe
continuos flow.
REMEDY
Disassemble, examine
all internal parts for
cause of the sticking
condition and clean off
scale deposits.
Disassemble and
replace diaphragm or
tighten the valve stem
nut.
Try operating valve a
few times. This might
dislodge the object. If
this fails, disassemble
and remove the
obstruction.
Check control
system. Tube line or
nipple might be plugged
up.
Clean tubing or pipe fit-
tings into cover cham-
ber. Open CK2 Isolation
Valve in control lines.
Establish line pressure.
Disassemble, examine
all internal parts for
cause of the sticking
problem, and clean off
scale deposits.
Disassemble and
replace diaphragm or
tighten valve stem nut.
Try operating valve a
few times. This might
dislodge the object. if
this fails disassemble
and remove the
obstruction.
Check control system.
Check lines or pipe fit-
tings. Clean out any
plugged lines.
Clean tubing or pipe fit-
tings into power unit
chamber.
Replace worn parts.
Disassemble and
replace O-ring.
*Assuming control system is functioning properly.
STEM TRAVEL
(Fully open to fully closed)
VALVE SIZE
VALVE SIZE