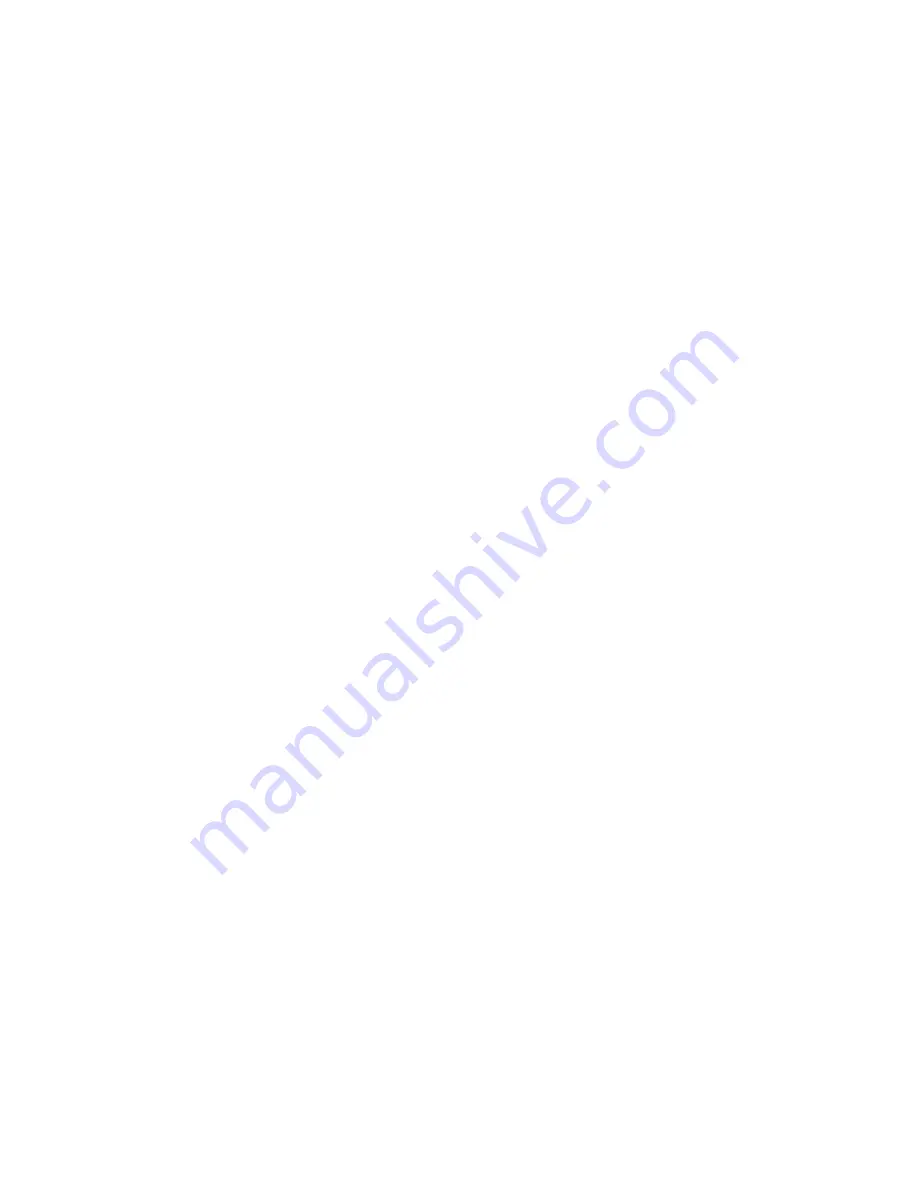
Page 5
ASSEMBLY INSTRUCTIONS
STRAIGHT FLOOR MODEL CONVEYORS
Motor or drive end is preferably located toward rear of plant away from Call Counter.
When removing drive end from crate (and during erection), do not lift or exert force on the link drive sprocket.
Avoid shock to either the motor, or the motor control box mounted (on the drive end section) adjacent to the
electric motor.
ERECTION
1.
Position all Conveyor sections on floor in general location for erection, with motor or drive end toward
rear of plant.
2.
Position base assemblies on floor in final locations. Allow at least 14” from the curved end of the track
for clothes clearance, and 14” from the side track to the wall, whenever the Conveyor is placed close to a
wall.
3.
Place vertical columns in base assemblies.
4.
Place coupler sections on the top of each intermediate column; no coupler being required on either of the
two end columns.
5.
Place drive end section on top of the rear colomn, and the 180 degree return end on top of the front
column.
6.
Insert the ends of two straight track sections (or equal length) into the ends of the 180 degree track
section of the drive end; the opposite ends of the straight track sections into the first coupler. Line up the
holes in the straight track sections with the mounting holes in the 180 degree track section and in the
first coupler. Insert bolts in the mounting holes but do not tighten. Place the head of the bolts on the
inside of the tubular track; a round washer and crown nut on the outer end of each bolt.
7.
Continue to install the remaining pairs of straight track sections between adjacent couplers. Line up the
holes in the straight track sections with the mounting holes in the couplers. Insert bolts (with washer
and nut) in the mounting holes of the couplers but do not tighten.
8.
Do not insert the ends of the last of the straight track sections into the ends of the 180 degree return end
section.
9.
Loosen the motor mounting plate on the drive end; slide motor mounting plate forward, so that the chain
can be lifted free of the small chain sprocket on the drive motor. This will permit free rotation of the
large link drive sprocket.
10. Feed each preassembled link assembly into the tubular track; joining each successive link assembly by
connecting a short swivel link to the end of an adjacent link by means of the cross pin in the swivel link.
Feed the links around the link drive sprocket so that the roller sleeve of each J bolt enters a tooth of the
link drive sprocket. Be sure the name CISSELL on each link faces to the outside.
11. Feed the links of the last link assembly into the 180 degree track section of the return end assembly;
insert the ends of the track section into the ends of the 180 degree track section of the return end; insert
bolts in the mounting holes, but do not tighten. Join the final adjacent end links of the link assemblies
by connecting the short swivel link to the adjacent end link by means of the cross pin in the swivel link.
12. Align track; butt the ends of each adjacent track section tightly and then tighten the track bolts. Do not
leave a space between the ends of the adjacent track sections as this will materially reduce the life
expectancy of the (nylon) plastic roller wheels.
Содержание MAN77
Страница 10: ...Page 10 DIMENSIONS AND CLEARANCE GARMENT BAG...