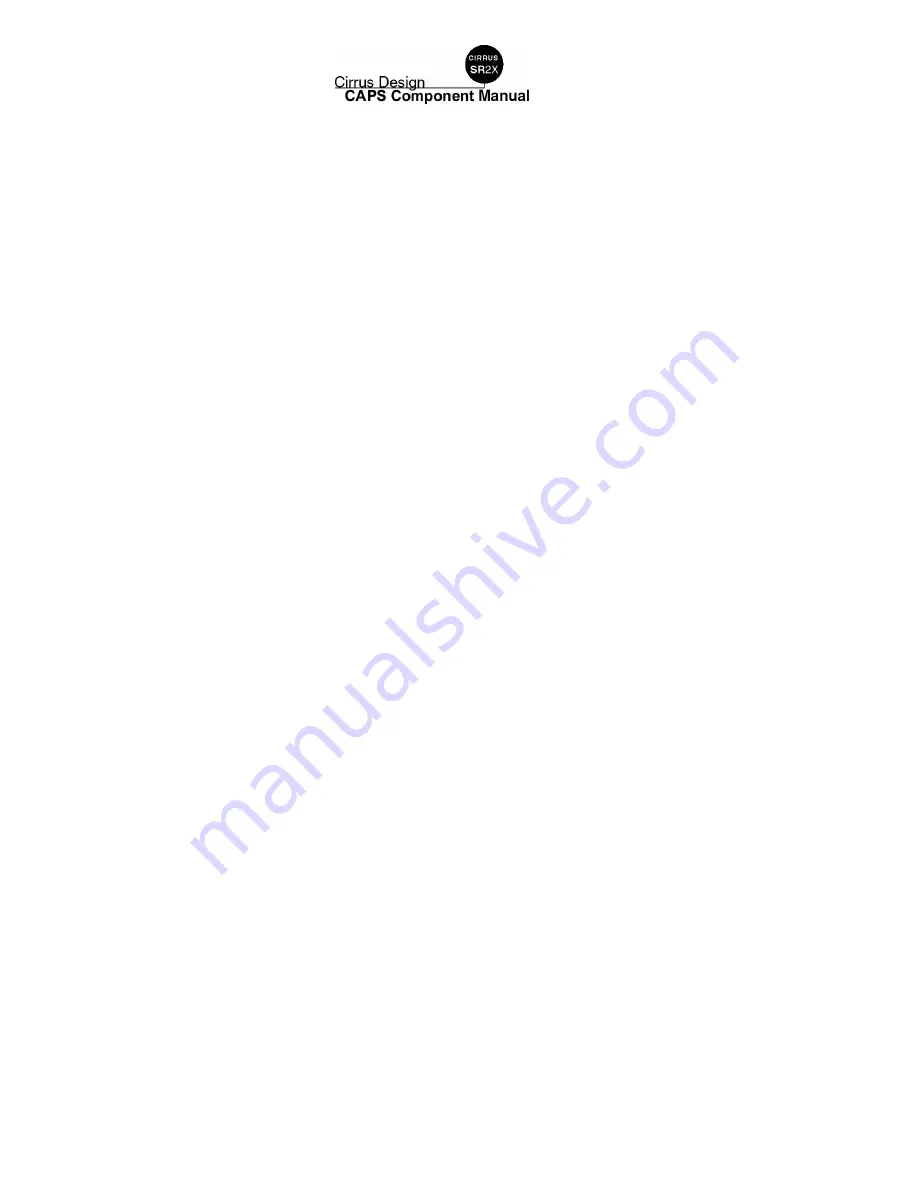
12128-001
95-01
Page 6
15 Sept 2002
C. Incremental Bridle and Deployment Bag (See Figure 95-013)
The rocket motor is attached to the deployment bag via a set of Teflon sheathed stainless steel cables,
or rocket lanyards, and an incremental bridle. The incremental bridle consists a length of nylon web-
bing that is folded in half and sewn with a series of bartack stitches. Upon activation these stitches are
peeled away to provide proper rocket/bag dynamics by acting as a shock absorber. The incremental
bridle, which is connected to the end of the rocket lanyards is protected from the rocket exhaust by a
heavy kevlar sheath.
A deployment bag is used to contain the packed parachute assembly within the fuselage enclosure
and stage its deployment and inflation sequence. The parachute assembly is packed into two compart-
ments within the deployment bag. The innermost compartment contains the canopy and is secured by
an internal flap that is locked in place with a series of locking loops to ensure that the canopy cannot
be extracted from its compartment until the suspension lines, stored in the outer compartment, are
pulled taut, and the line stows are extracted from the locking loops that hold the flaps closed.
The suspension lines are secured with a hook and loop closure. The four outer flaps are secured with
five steel curved release pins attached to the riser. The pins are extracted when the riser is pulled taut
during extraction. The deployment bag creates an orderly deployment process by allowing the canopy
to inflate only after the rocket motor has pulled the aircraft attachment harness, riser and suspension
lines taut and pulled the deployment bag off the canopy. This prevents any slack or uneven tension in
the suspension lines during canopy inflation that could result in a malfunction.
D. Parachute Assembly (See Figure 95-014)
The parachute slows the airplane to a descent speed that is conducive to a safe touchdown. The basic
structure of the parachute assembly consists of the canopy, suspension lines, and the slider; a compo-
nent used to aerodynamically reef the parachute and limit inflation loads.
(1)
Canopy and Suspension Lines
The 2400 sq ft round canopy, which creates the aerodynamic drag, is made up of a series of fab-
ric panels sewn together to form its desired shape. The canopy has a vent at its center to allow
some air to escape in a controlled manner and thus reduce oscillations and provide a stable
descent. Vent lines are attached to the perimeter of the vent and routed symmetrically across its
center to provide structural support and maintain its shape.
The suspension lines are attached to the “skirt” of the canopy and converge to a riser or set of
risers at the opposite end. The canopy structural integrity is enhanced by a “skeleton” of tapes
and webbings sewn nearly perpendicular to each other to the top surface of the canopy fabric.
Radial bands run from opposite suspension line attachment points, across the top of the canopy.
The skirt band, vent band, and lateral bands run around the circumference of the canopy.
The CAPS parachute is fabricated from woven textiles in the form of fabrics, tapes, webbing, and
thread. All of the textile components in CAPS are fabricated from either Kevlar or Nylon and are
woven to military specifications that define specific parameters such as yarn count, yarn twist,
weave type, and finish. To insure good aging characteristics, the only exception to the use of
Kevlar and Nylon is a Teflon cloth buffer on the risers at the suspension line attachment point.
A typical deployment load profile begins with a snatch force which occurs when the parachute
assembly is initially extracted from its container and pulled to full line stretch. When air begins to
fill the canopy, inflation loads result. The parachute is designed to deploy without generating
forces high enough to injure the airplane occupants.
Содержание CAPS
Страница 2: ......
Страница 4: ......
Страница 11: ...12128 001 95 01 Page 3 Figure 95 011 CAPS System and Deployment 15 Sept 2002 ...
Страница 13: ...12128 001 95 01 Page 5 Figure 95 012 CAPS Handle and Ignition System 15 Sept 2002 ...
Страница 15: ...12128 001 95 01 Page 7 Figure 95 013 Incremental Bridle and Deployment Bag 15 Sept 2002 ...
Страница 17: ...12128 001 95 01 Page 9 Figure 95 014 Parachute Assembly and Line Cutters 15 Sept 2002 ...
Страница 18: ...THIS PAGE INTENTIONALLY LEFT BLANK ...
Страница 21: ...12128 001 95 01 Page 13 Figure 95 015 Pyrotechnic Line Cutters Replacement Sheet 1 of 2 15 Sept 2002 ...
Страница 22: ...12128 001 95 01 Page 14 Figure 95 015 Pyrotechnic Line Cutters Replacement Sheet 2 of 2 15 Sept 2002 ...
Страница 27: ...12128 001 95 01 Page 19 Figure 95 016 CAPS Cover Installation 15 Sept 2002 ...
Страница 30: ...12128 001 95 01 Page 22 Figure 95 017 CAPS Rocket Assembly Sheet 1 of 2 15 Sept 2002 ...
Страница 31: ...12128 001 95 01 Page 23 Figure 95 017 CAPS Rocket Assembly Sheet 2 of 2 15 Sept 2002 ...
Страница 37: ...12128 001 95 01 Page 29 Figure 95 018 CAPS Activation System 15 Sept 2002 ...
Страница 38: ...12128 001 95 01 Page 30 Figure 95 019 Sheet 1 of 2 CAPS Test Fixture 15 Sept 2002 ...
Страница 39: ...12128 001 95 01 Page 31 Figure 95 019 Sheet 2 of 2 CAPS Test Fixture 15 Sept 2002 ...
Страница 40: ...THIS PAGE INTENTIONALLY LEFT BLANK ...