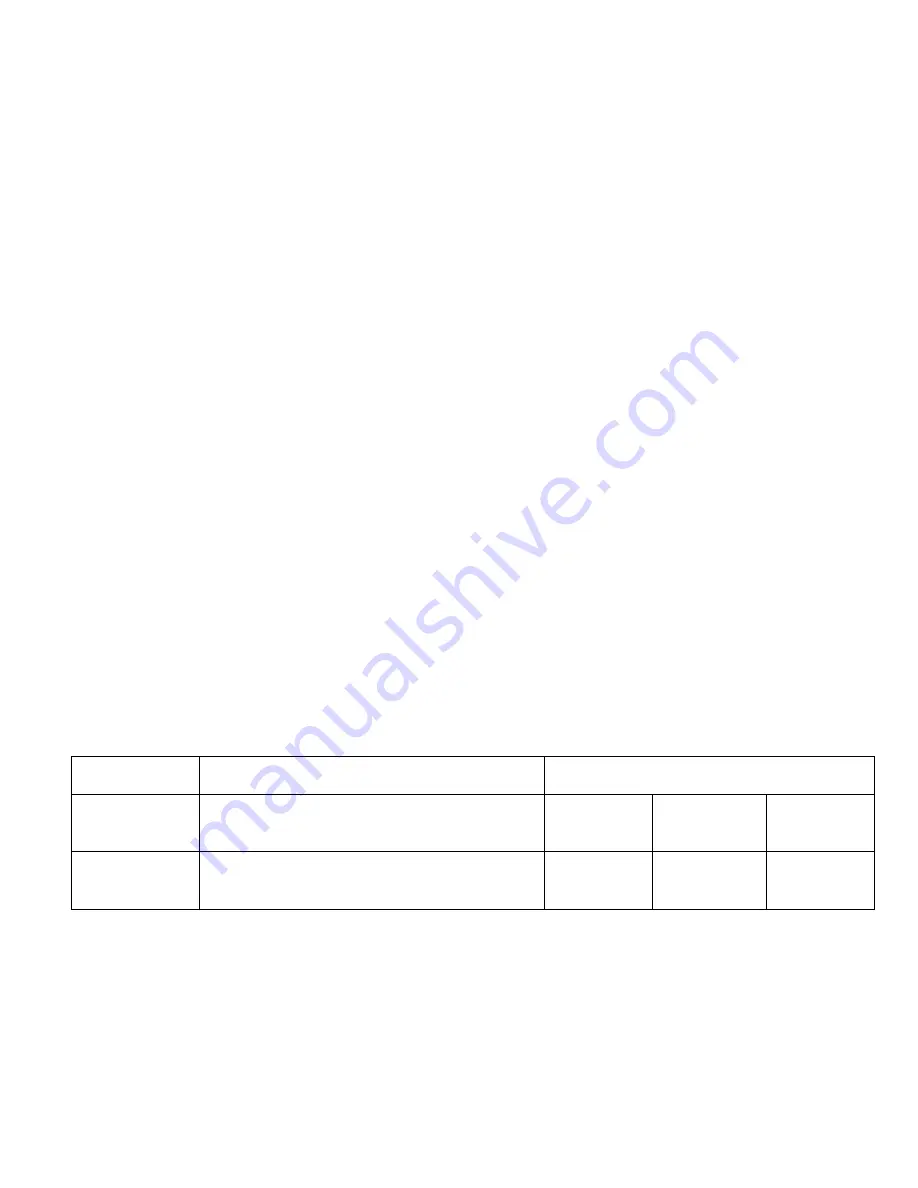
FOREWORD
Instruction manual covers Imo Pump Series A3D pumps. Series of pumps have been designed to meet
requirements for hydraulic, distillate, lubricating, residual and crude oil applications. Because of large
number of operating conditions, it is necessary to have a variety of construction and material combinations
to meet job requirements. Model of each pump is identified on pump nameplate. Correct use of manual
requires identification of Figure(s) applicable to pump assembly and seal arrangement. Refer to Table 1,
assembly drawings, Figures 3, 7, 8, 9, 10 and mechanical seal drawings, Figure 2, for applicable pump seal
selection. Packing pumps are illustrated in Figures 4, 5, 6. If pump type is not specifically identifiable in
manual, contact Imo Service Department with pump model and serial number for assistance 704-289-6511.
Instructions given herein cover generally the operation and maintenance of subject equipment.
Should any questions arise which may not be answered specifically by these instructions, they
should be referred to Imo Pump for further detailed information and technical assistance.
Manual cannot possibly cover every situation connected with operation, adjustment, test, overhaul and
maintenance of equipment furnished. Every effort is made to prepare text of manual so that engineering
and design data is transformed into most easily understood wording. Imo Pump, in furnishing this
equipment and this manual, must presume that operating and maintenance personnel assigned thereto
have sufficient technical knowledge and experience to apply sound safety and operational practices which
may not be otherwise covered herein.
In applications where Imo Pump furnished equipment is to be integrated with a process or other machinery,
these instructions should be thoroughly reviewed to determine proper integration of equipment into overall
plant operational procedures. On critical or dangerous equipment, provide suitable safety and emergency
systems to protect personnel and property from injury due to pump malfunction. If pump handles
flammable, toxic, corrosive or explosive fluids, provide for safety in event of pump leakage or malfunction.
If installation, operation, and maintenance instructions are not correctly and strictly followed and observed,
serious damage to pump could result. Imo Pump cannot accept responsibility for unsatisfactory
performance or damage resulting from failure to comply with instructions.
Table 1
SERIES A3D TYPICAL PUMP ASSEMBLY DRAWINGS
MECHANICAL
SEALS
PACKING
PUMPS
Rotor Size
106, 118, 137, 156, 187, 218, 250, 275, 337,
312, 350, 400
106,118
137,156,187
218,250,275
Figure No.
3, 7, 8, 9, 10
4
5
6
Figure 1 - Definitions of Model Designators