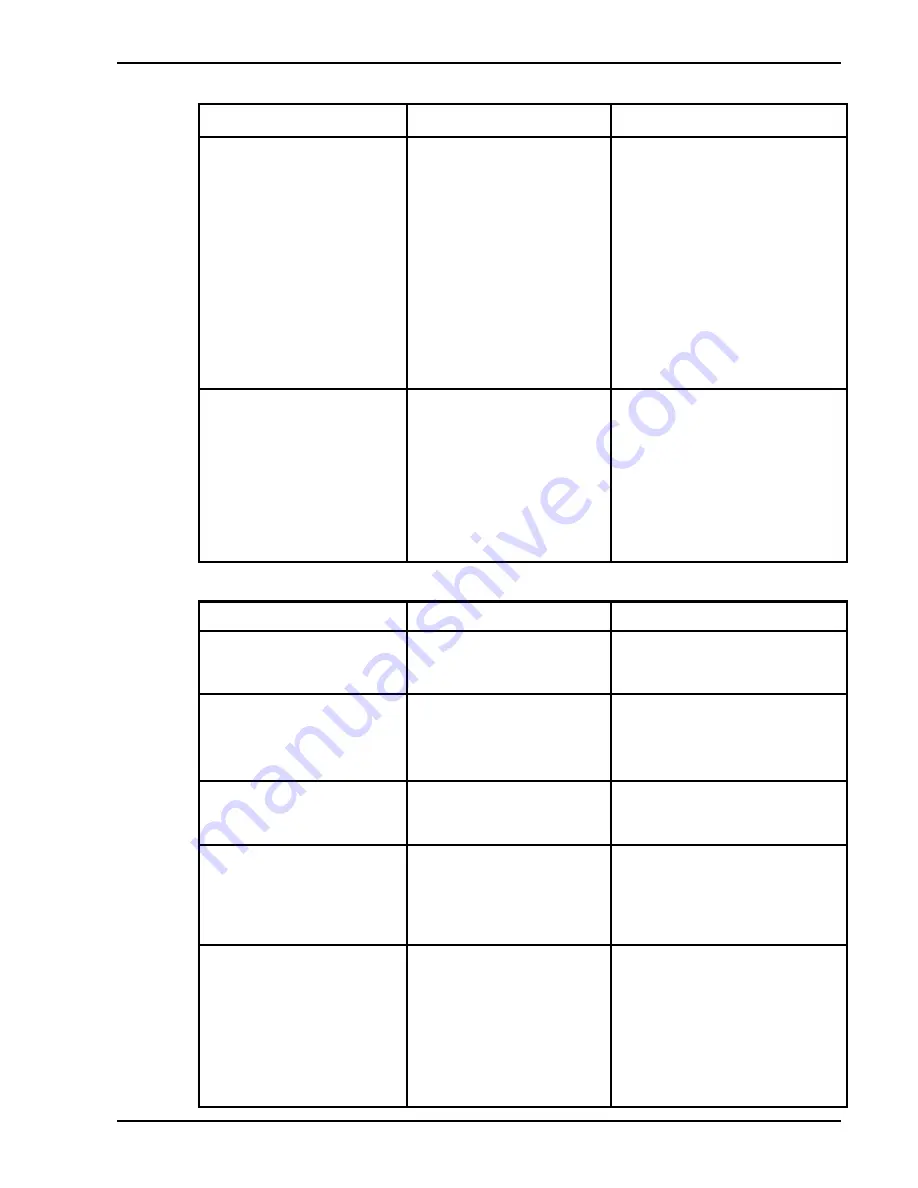
Transmig 210, 250, 310, 330
DOC No: MIGTRN0001 Page 29 of 31
Issue No: 2 Date: 14/09/98
Welding Problems (continued)
FAULT CAUSE REMEDY
7 Weld cracking A Weld beads too small A Decrease torch travel speed
B Weld penetration narrow
and deep
B Reduce current and voltage and
increase the MIG Torch travel
speed or select a lower
penetration shielding gas.
C Excessive weld stresses C Increase weld metal strength or
revise design
D Excessive voltage D Decrease voltage by reducing the
Voltage Control switches.
E
Cooling rate too fast E
Slow the cooling rate by
preheating part to be welded or
cool slowly.
8 Cold weld puddle A Faulty rectifier unit A Have an Accredited CIGWELD
Service Agent test then replace
the faulty component.
B Loss of a phase in the
Mains supply voltage.
B Check mains power
C Loose welding cable
connection.
C Check all welding cable
connections.
D Low Mains supply voltage D Contact supply authority
10.3 Power Source Problems
FAULT CAUSE REMEDY
1 Indicator light is ON but
welding arc can not be
established.
Coarse Voltage Control
switch is in the
STANDBY
position.
Switch the Coarse Voltage
Control switch to a welding
setting.
2 Mains supply voltage is
ON. Indicator light is not lit
and welding arc can not be
established.
A
B
Primary fuse is blown.
Broken connection in
primary circuit.
A
B
Replace primary fuse.
Have an Accredited CIGWELD
Service Agent check primary
circuit.
3 Mains indicator light is not
lit but welding arc can be
established.
Burnt out Indicator light. Have an Accredited CIGWELD
Service Agent replace Indicator
light.
4 Mains supply voltage is
ON and Indicator light is lit
but when the torch trigger
switch is depressed nothing
happens.
Torch trigger switch leads
are disconnected.
Reconnect.
5 Mains supply voltage is
ON, no wire feed but gas
flows from the MIG Torch
when the torch trigger
switch is depressed.
A Electrode wire stuck in
conduit liner or contact tip
(burn-back jam).
A Check for clogged / kinked MIG
Torch conduit liner or worn
contract tip. Replace faulty
components.
B Faulty control PCB B Have an Accredited CIGWELD
Service Agent investigate the
fault.