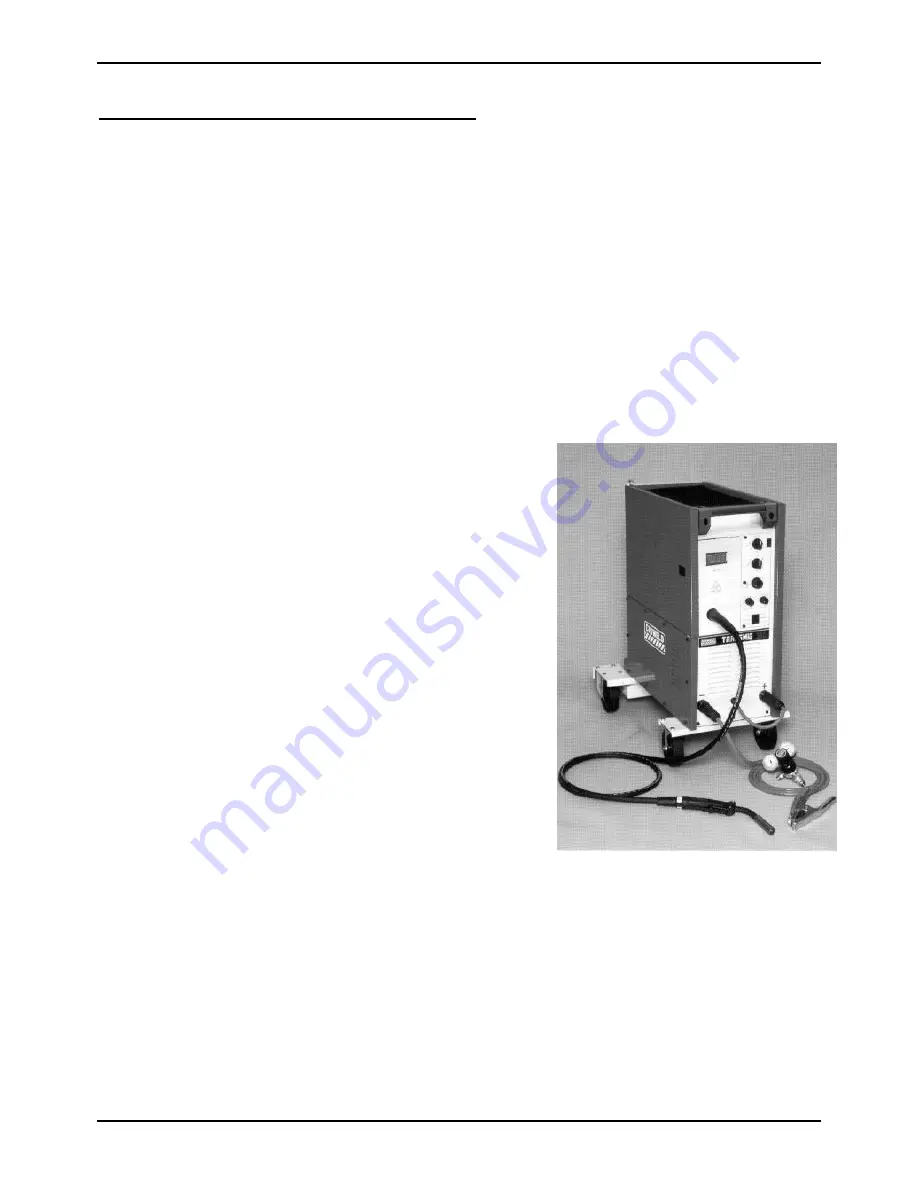
Transmig 210, 250, 310, 330
Page 14 of 31 DOC No: MIGTRN0001
Date: 14/09/98 Issue No: 2
4. SET UP FOR COMPACT TRANSMIGS
Refer to Figure 4 for the plant setup of a compact Transmig.
a) Remove all packaging materials.
b) Fit the fixed and swivel wheels to the Power Source.
WARNING 2: To obtain adequate air flow and cooling for the Power Source components, the
four wheels must be fitted. Alternatively, the Power Source may be raised
140mm from the floor using supports that do not restrict airflow.
c) Connect the work lead to the negative welding terminal (-) [positive welding terminal (+)
for flux cored wire].
d) Connect the
TORCH
lead to the positive welding terminal (+) [negative welding terminal
(-) for flux cored wire].
e) Position a gas cylinder on the rear tray and lock securely to the Power Source cylinder
bracket with the chain provided. If this arrangement is not used then ensure that the gas
cylinder is secured to a building pillar, wall bracket or otherwise securely fixed in an
upright position.
f) Fit the gas Regulator/Flowmeter to the gas
cylinder.
g) Connect the gas hose from the rear of the Power
Source to the Flowmeter outlet.
h) Two dual groove feed rollers are supplied as
standard with the plant. These can accommodate
0.6, 0.8, 0.9 and 1.2 diameter hard wires. Select
the roller required with the chosen wire size
marking facing outwards.
i) Fit the electrode wire spool to the wire reel hub
located behind the wire compartment door.
Ensure that the drive dog-pin engages the mating
hole in the wire spool. Push the 'R' clip into place
to retain the wire spool securely. The wire should
feed from the bottom of the spool.
j) Fit the TWECO MIG torch to the wire feed unit
by releasing the torch locking screw in the brass
torch adaptor and pushing in the torch fitting until
the plastic torch casing meets the brass adaptor.
Tighten the torch locking screw securely. Also
ensure that the adjacent black knurled screw in the
wire feeder casting is securely tightened. Remove the contact tip from the torch.
k) Connect the two black torch trigger leads to the torch trigger terminals.
l) Lift up the wire feeder pressure lever and pass the electrode wire through the inlet guide,
between the rollers, through the outlet guide and into the torch.
m) Lower the pressure lever and with the torch lead reasonably straight, feed the wire through
the torch. Fit the appropriate contact tip.
CAUTION 3: The electrode wire will be at welding voltage potential whilst it is being fed
through the system.
Figure 4 - Compact Transmig Setup