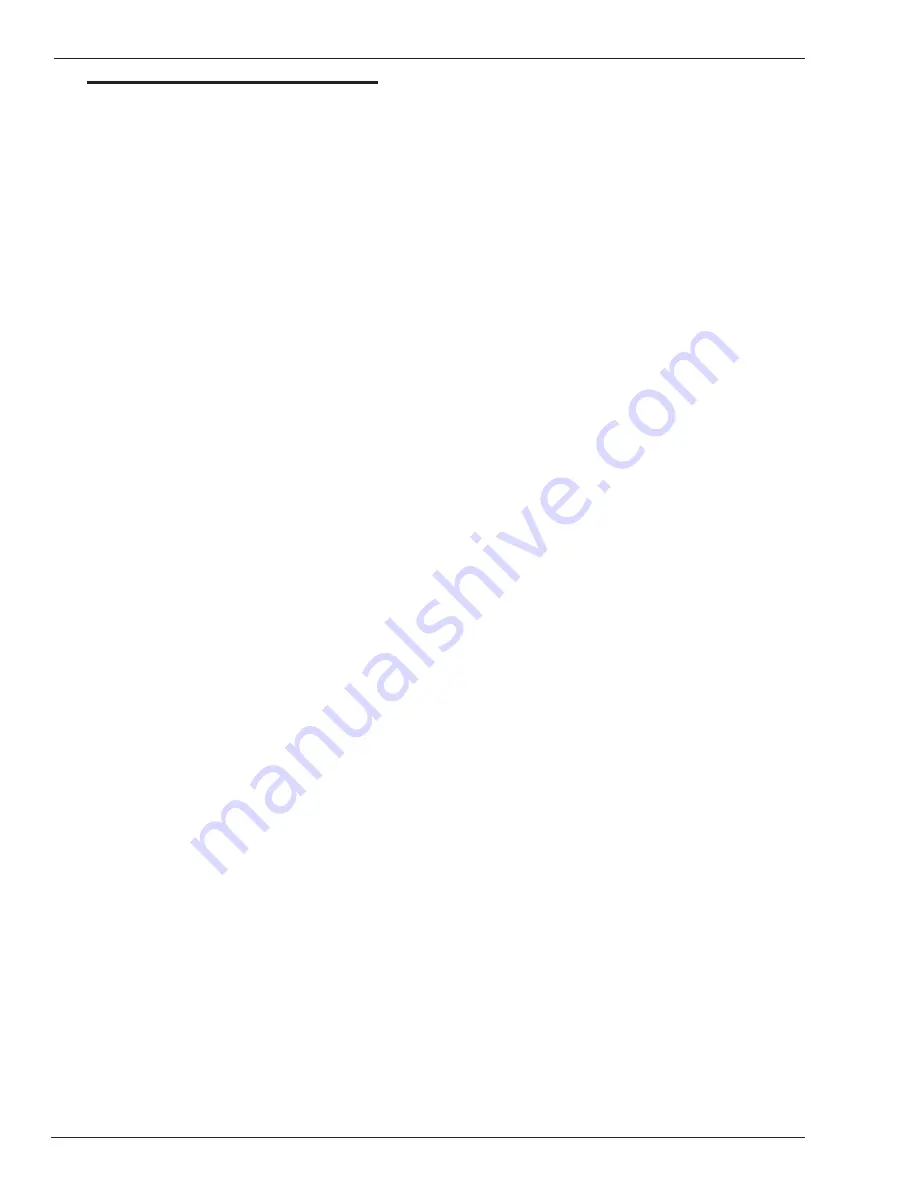
TRANSMIG 2RT
INSTALLATION/SETUP
INSTALLATION/SETUP 3-2
Manual 0-5196
NOTE
The welding circuit may or may nor be earthed
for safety reasons. Changing the earthing ar-
rangements should only be authorised by a
person who is competent to assess whether
the changes will increase the risk of injury,
e.g. by allowing parallel welding current return
paths which may damage the earth circuits of
other equipment. Further guidance is given in
IEC 60974-13 Arc Welding Equipment - Instal-
lation and use (under preparation).
B. Assessment of Area
Before installing welding equipment, the user shall make
an assessment of potential electromagnetic problems in
the surrounding area. The following shall be taken into
account.
1. Other supply cables, control cables, signalling and
telephone cables; above, below and adjacent to the
welding equipment.
2. Radio and television transmitters and receivers.
3. Computer and other control equipment.
4. Safety critical equipment, e.g. guarding of industrial
equipment.
5. The health of people around, e.g. the use of pace-
makers and hearing aids.
6. Equipment used for calibration and measurement.
7. The time of day that welding or other activities are to
be carried out.
8. The immunity of other equipment in the environment:
the user shall ensure that other equipment being used
in the environment is compatible: this may require
additional protection measures.
The size of the surrounding area to be considered will
depend on the structure of the building and other activities
that are taking place. The surrounding area may extend
beyond the boundaries of the premises.
C. Methods of Reducing Electromagnetic Emissions
1. Mains Supply
Welding equipment should be connected to the
mains supply according to the manufacturer’s
recommendations. If interference occurs, it may be
necessary to take additional precautions such as
filtering of the mains supply. Consideration should
be given to shielding the supply cable of permanently
installed welding equipment in metallic conduit or
equivalent. Shielding should be electrically continuous
throughout its length. The shielding should be
connected to the Welding Power Source so that good
electrical contact is maintained between the conduit
and the Welding Power Source enclosure.
2. Maintenance of Welding Equipment
The welding equipment should be routinely maintained
according to the manufacturer’s recommendations. All
access and service doors and covers should be closed
and properly fastened when the welding equipment
is in operation. The welding equipment should not
be modified in any way except for those changes
and adjustments covered in the manufacturer’s
instructions.
3. Welding Cables
The welding cables should be kept as short as possible
and should be positioned close together but never
coiled and running at or close to the floor level.
4. Equipotential Bonding
Bonding of all metallic components in the welding
installation and adjacent to it should be considered.
However, metallic components bonded to the work
piece will increase the risk that the operator could
receive a shock by touching the metallic components
and the electrode at the same time. The operator
should be insulated from all such bonded metallic
components.
5. Earthing/grounding of the Work Piece
Where the work piece is not bonded to earth for electri-
cal safety, nor connected to earth because of its size
and position, e.g. ship’s hull or building steelwork,
a connection bonding the work piece to earth may
reduce emissions in some, but not all instances. Care
should be taken to prevent the earthing of the work
piece increasing the risk of injury to users, or damage
to other electrical equipment. Where necessary, the
connection of the work piece to earth should be made
by direct connection to the work piece, but in some
countries where direct connection is not permitted, the
bonding should be achieved by suitable capacitance,
selected according to national regulations.
6. Screening and Shielding
Selective screening and shielding of other cables
and equipment in the surrounding area may alleviate
problems of interference. Screening the entire welding
installation may be considered for special applications.
Содержание 2RT TRANSMIG
Страница 6: ......
Страница 36: ...TRANSMIG 2RT INSTALLATION SETUP INSTALLATION SETUP 3 20 Manual 0 5196 Notes...
Страница 46: ...TRANSMIG 2RT REPLACEMENT PARTS REPLACEMENT PARTS 6 2 Manual 0 5196 Notes...
Страница 49: ......