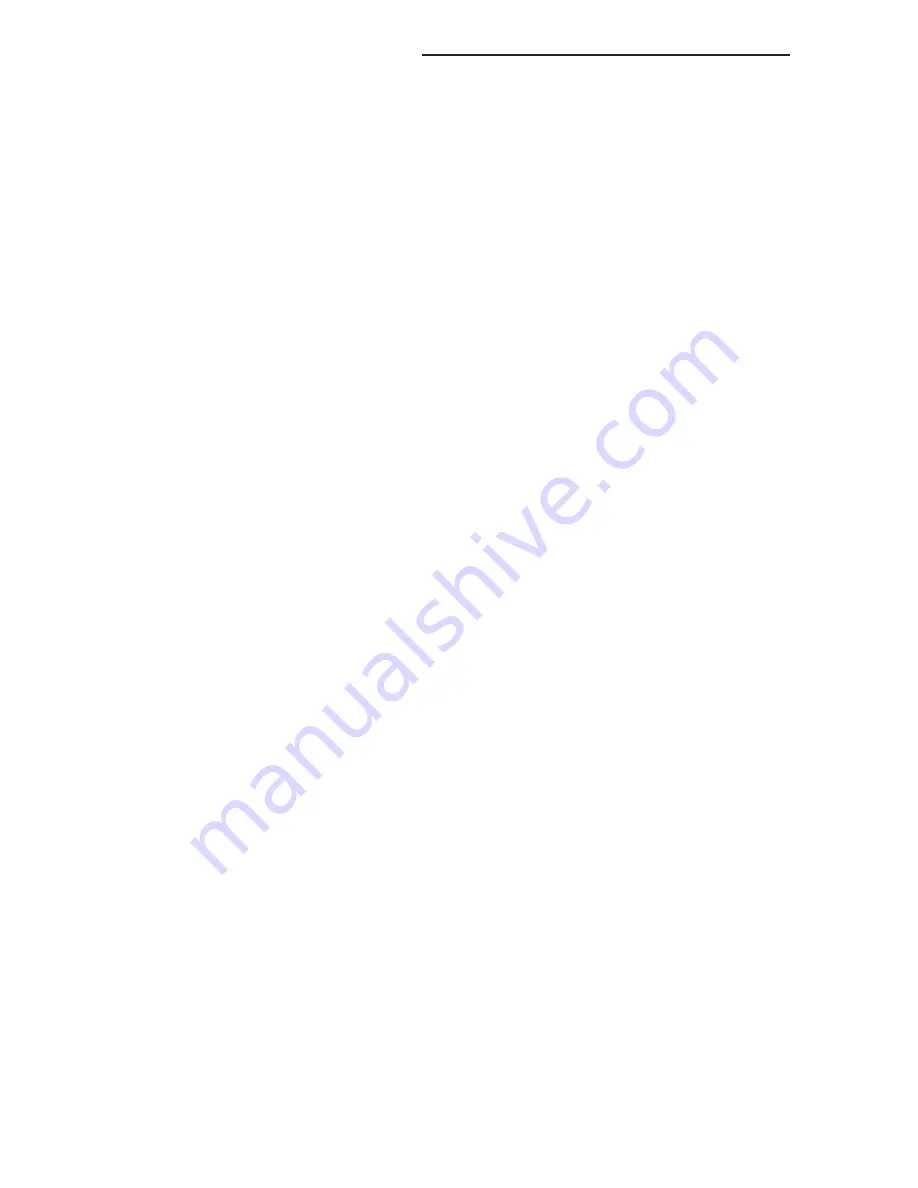
SHIFT MECHANISM
DESCRIPTION
The gear shift mechanism provides six shift posi-
tions which are:
•
PARK (P)
•
REVERSE (R)
•
NEUTRAL (N)
•
DRIVE (D)
•
Manual SECOND (2)
•
Manual LOW (1)
OPERATION
Manual LOW (1) range provides first gear only.
Overrun braking is also provided in this range. Man-
ual SECOND (2) range provides first and second gear
only.
DRIVE range provides first, second, third, and
overdrive fourth gear ranges. The shift into overdrive
fourth gear range occurs only after the transmission
has completed the shift into D third gear range. No
further movement of the shift mechanism is required
to complete the 3-4 shift.
The fourth gear upshift occurs automatically when
the overdrive selector switch is in the ON position.
No upshift to fourth gear will occur if any of the fol-
lowing are true:
•
The transmission fluid temperature is below 10°
C (50° F) or above 121° C (250° F).
•
The shift to third is not yet complete.
•
Vehicle speed is too low for the 3-4 shift to occur.
•
Battery temperature is below -5° C (23° F).
SOLENOID
DESCRIPTION
The typical electrical solenoid used in automotive
applications is a linear actuator. It is a device that
produces motion in a straight line. This straight line
motion can be either forward or backward in direc-
tion, and short or long distance.
A solenoid is an electromechanical device that uses
a magnetic force to perform work. It consists of a coil
of wire, wrapped around a magnetic core made from
steel or iron, and a spring loaded, movable plunger,
which performs the work, or straight line motion.
The solenoids used in transmission applications
are attached to valves which can be classified as nor-
mally open or normally closed. The normally
open solenoid valve is defined as a valve which
allows hydraulic flow when no current or voltage is
applied to the solenoid. The normally closed sole-
noid valve is defined as a valve which does not allow
hydraulic flow when no current or voltage is applied
to the solenoid. These valves perform hydraulic con-
trol functions for the transmission and must there-
fore be durable and tolerant of dirt particles. For
these reasons, the valves have hardened steel pop-
pets and ball valves. The solenoids operate the valves
directly, which means that the solenoids must have
very high outputs to close the valves against the siz-
able flow areas and line pressures found in current
transmissions. Fast response time is also necessary
to ensure accurate control of the transmission.
The strength of the magnetic field is the primary
force that determines the speed of operation in a par-
ticular solenoid design. A stronger magnetic field will
cause the plunger to move at a greater speed than a
weaker one. There are basically two ways to increase
the force of the magnetic field:
1. Increase the amount of current applied to the
coil or
2. Increase the number of turns of wire in the coil.
The most common practice is to increase the num-
ber of turns by using thin wire that can completely
fill the available space within the solenoid housing.
The strength of the spring and the length of the
plunger also contribute to the response speed possi-
ble by a particular solenoid design.
A solenoid can also be described by the method by
which it is controlled. Some of the possibilities
include variable force, pulse-width modulated, con-
stant ON, or duty cycle. The variable force and pulse-
width modulated versions utilize similar methods to
control the current flow through the solenoid to posi-
tion the solenoid plunger at a desired position some-
where between full ON and full OFF. The constant
ON and duty cycled versions control the voltage
across the solenoid to allow either full flow or no flow
through the solenoid’s valve.
OPERATION
When an electrical current is applied to the sole-
noid coil, a magnetic field is created which produces
an attraction to the plunger, causing the plunger to
move and work against the spring pressure and the
load applied by the fluid the valve is controlling. The
plunger is normally directly attached to the valve
which it is to operate. When the current is removed
from the coil, the attraction is removed and the
plunger will return to its original position due to
spring pressure.
The plunger is made of a conductive material and
accomplishes this movement by providing a path for
the magnetic field to flow. By keeping the air gap
between the plunger and the coil to the minimum
necessary to allow free movement of the plunger, the
magnetic field is maximized.
21 - 252
AUTOMATIC TRANSMISSION - 48RE
DR
Содержание 48RE
Страница 4: ...Fig 1 48RE Transmission DR AUTOMATIC TRANSMISSION 48RE 21 133 AUTOMATIC TRANSMISSION 48RE Continued ...
Страница 48: ...HYDRAULIC FLOW IN NEUTRAL DR AUTOMATIC TRANSMISSION 48RE 21 177 AUTOMATIC TRANSMISSION 48RE Continued ...
Страница 49: ...HYDRAULIC FLOW IN REVERSE 21 178 AUTOMATIC TRANSMISSION 48RE DR AUTOMATIC TRANSMISSION 48RE Continued ...
Страница 50: ...HYDRAULIC FLOW IN DRIVE FIRST GEAR DR AUTOMATIC TRANSMISSION 48RE 21 179 AUTOMATIC TRANSMISSION 48RE Continued ...
Страница 57: ...HYDRAULIC FLOW IN MANUAL LOW 1 21 186 AUTOMATIC TRANSMISSION 48RE DR AUTOMATIC TRANSMISSION 48RE Continued ...
Страница 58: ...HYDRAULIC FLOW IN MANUAL SECOND 2 DR AUTOMATIC TRANSMISSION 48RE 21 187 AUTOMATIC TRANSMISSION 48RE Continued ...