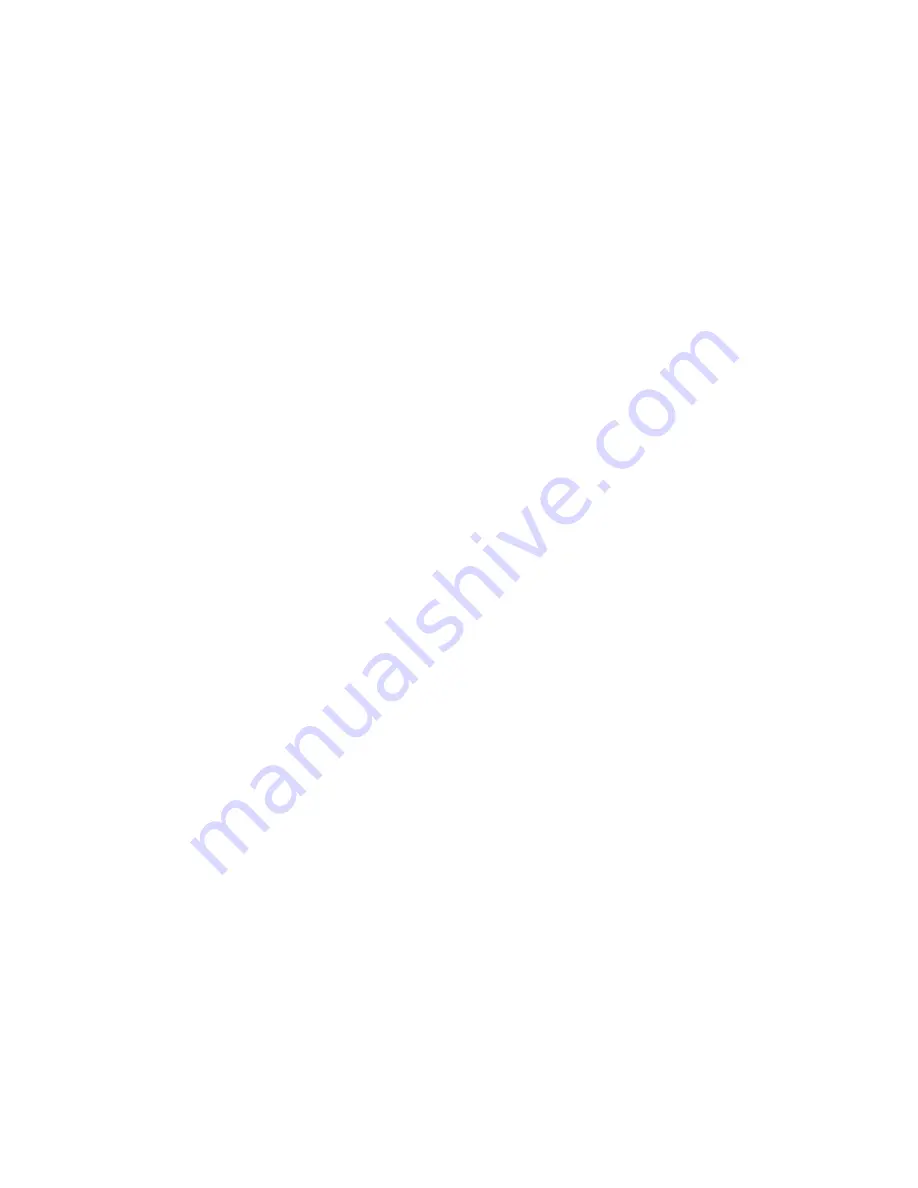
34 GENERAL INFORMATION AND MAINTENANCE
ally check that you can gain access to all of
the transmission pan bolts. If you can, pro-
ceed to step 8; if not, proceed to step 2.
2. Place a jack under the transmission
with a block of wood (a piece of a 2x4 will do)
between the jack and the transmission pan.
3. Raise the jack until the wood block
contacts the transmission pan.
4. Remove the crossmember-to-trans-
mission mount bolts and the crossmember-
to-frame bolts.
5. Raise the transmission SLIGHTLY—
just enough to take the weight of the trans
mission off of the crossmember.
6. Turn the crossmember sideways and
remove it.
7. Place a jackstand close to the transmis
sion tailshaft. Lower the jack until the trans
mission rests on the stand. Remove the jack
and the wood block.
8. Place a drain pan under the transmis
sion pan. If the pan has a drain plug, remove
it and allow the fluid to drain.
9. If the pan does not have a drain plug,
remove the pan bolts from one side of the
pan and loosen the rest of the bolts. This will
allow the pan to partially drain. Remove the
remaining pan bolts and carefully lower the
pan away from the transmission.
NOTE:
If the transmission fluid is dark or
has a burnt smell, transmission damage is
indicated. Have the transmission checked
professionally.
CAUTION:
If the pan sticks, carefully tap
sideways on the pan with a rubber mallet
or a plastic hammer to break the pan loose.
DO NOT dent the pan. Avoid prying the
pan off with a screwdriver
—
this can bend
the pan or crack the transmission case.
10. Empty the pan, remove the gasket
material, and clean the pan with solvent (car
buretor cleaner works well).
11. Remove any gasket material which may
remain on the transmission case.
12. Remove the transmission filter from the
valve body. The filter may have either a fi
brous or screen filtering element and is re
tained by one or two fasteners.
13. Install a new filter using a new gasket
or O-ring (TH400's).
NOTE:
If the transmission uses a filter
having a fully exposed screen, it may be
cleaned and re-used.
14. Install the pan using a new gasket.
Tighten the bolts to 12-14 ft. Ibs. in a criss
cross pattern. Recheck the bolt torque after
all of the bolts have been tightened once.
15. Add either Dexron or Dexron II trans
mission fluid through the filler tube. See the
Capacities Chart to determine the proper
amount of fluid to be added.
CAUTION: DO NOT
OVERFILL the
transmission; foaming of the fluid and sub-
sequent transmission damage due to slip-
page will result.
16. With the gearshift lever in PARK, start
die engine and let it idle. Do not race the
engine.
17. Move the gearshift lever through each
position, holding the brakes. Return the le
ver to PARK, and check the fluid level with
the engine idling. The level should be be
tween the two dimples on the dipstick, about
Vs.
in. below the ADD mark. Add fluid, if
necessary.
18. Check the fluid level after the vehicle
has been driven enough to thoroughly warm
up the transmission. Details are given under
Fluid Level Checks earlier in the Chapter. If
the transmission is overfilled, the excess must
be drained off-
REAR
AXLE
Refer to the Maintenance Intervals chart for
information on when to change the fluid.
1. Run the vehicle so the lubricant reaches
operating temperature.
2. Position a drain pan under the rear axle.
3. Remove the axle housing cover and gas
ket and drain the lubricant.
4. Clean the gasket sealing surfaces and
install the cover with a new gasket.
5. Torque the cover bolts in a crosswise
pattern to 20 ft. Ibs.
6. Add 4 oz. of rear axle lubricant additive
(GM 1052358).
7. Use a suction gun or a squeeze bulb and
refill the differential housing to a level within
%" of the filler plug with rear axle lubricant
(GM 1052271) or equivalent. (See the Capac
ities Chart),
8. Install the filler plug.
COOLANT
Refer to the Cooling System Section under
Routine Maintenance. Observe the recom-
mended specifications for aluminum, if nec-
essary.
Chassis Greasing
Chassis greasing can be performed with a
pressurized grease gun or it can be per-
formed at home by using a hand-operated
Содержание 1963 Corvette
Страница 29: ...3 0 1973 3 0 15 18 Is 454 8 18 24 15 4 0...
Страница 36: ...GENERAL INFORMATION AND MAINTENANCE 31 CM E 8 in 1 o s 1 O 1 8 o o o o CD o o o CO E o o o co JD in fCD I ts...
Страница 83: ...OHMMETER OHMMETER Stator testing perforated case models...
Страница 125: ...Wear ridge must be removed before piston removal...
Страница 161: ...14 Vacuum piston 15 Vacuum piston spring 16 Pump plunger assembly 17 Pump plunger return spring 18 Primary float...
Страница 205: ...EMISSION CONTROLS AND FUEL SYSTEM 187 8 CO 8 8 8 8 inCM CO 8 CM I I I IS N ino 1...